Factory Digital Twin
The Smart Data Warehouse
See the Right Information - Create the Right Schedule - Make the Right Moves
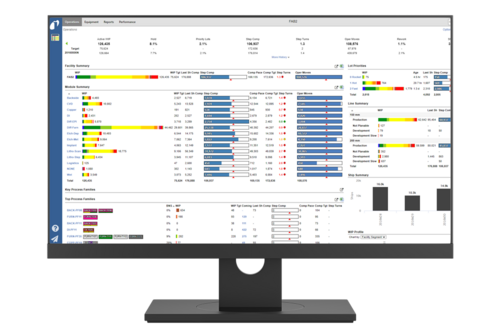
The FPS Digital Twin is the most critical building block for developing a Smart factory. It collects all the real-time operations events to compute cycle time and throughput data to drive powerful applications.
Real-Time Factory Digital Twin
The FPS Digital Twin easily combines and organizes all of the complex factory data required to visualize and simulate the real-time factory conditions. This data is used to power critical applications such as Factory Scheduling and Metrology Sampling enabling optimal WIP movement and management throughout the factory.
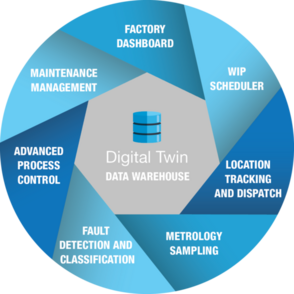
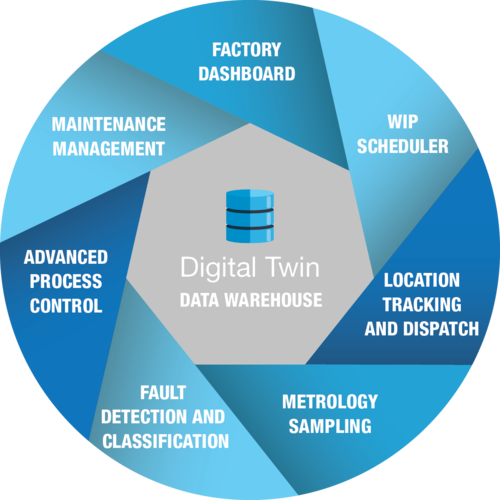
Integrate With all Factory Systems
- MES
- AMHS
- Equipment Integration
- Fault Detection
- Advanced Process Control
- Statistical Process Control
- Planning
- Maintenance Managment
- Any other systems
The FPS Digital Twin common platform enables all factories to have the same look, feel, and messaging regardless of the type of other systems installed. This simplifies the installation of other FPS applications and enables end-user development of core software systems.
Automatic Cycle Time and Throughput
The FPS Digital Twin automatically calculates cycle time (CT) and throughput (THP) from lot and substrate event data. The Digital Twin calculates process end times and arrival times in operations multiple steps away. Cycle Time and Throughput data are what the FPS Factory Schedulers use to look into the future and optimize the flow of Work in Process. It is also what Next Move relies on to call out upcoming and required operator actions. The Digital Twin along with the Factory Dashboard also provides all the tools needed to understand the quality and accuracy of the data held within the Digital Twin. Through comprehensive analysis, the system can quickly identify tool sets where event data is not reliable enough to generate the required state information, and where external or manually overriding data should be used.
Over Two Decades of Refinement and Industry Wisdom
The Digital Twin is a repository of industrial engineering knowledge and best practices from across the industry. Besides key features like Enhanced Tool Performance states, Enhanced Cycle Time, and Throughput, there are other statistics like: transit times, lot ships, line balance quantities, test wafer data, and more.