FDC Semiconductor Software
AI Enhanced Fault Detection and Classification Software for Semiconductor Manufacturing Process Control
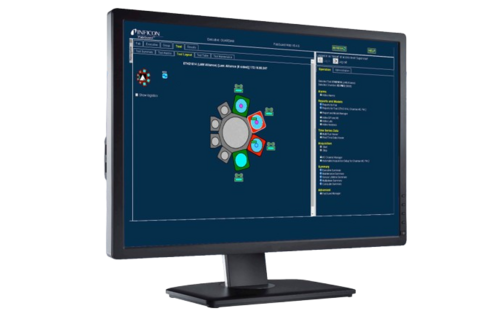
INFICON FDC: Predictive Maintenance & Process Optimization
INFICON's Fault Detection and Classification (FDC) solutions provide semiconductor and high-tech manufacturers with a powerful, data-driven approach to process control and predictive maintenance. By detecting variations in real time, INFICON helps fabs maintain stability, maximize efficiency, and reduce operational risks.
- Minimize Downtime: Detects and addresses tool issues and process drift before they impact yield, ensuring uninterrupted production.
- Improve Yield: Identifies subtle deviations early to reduce scrap, rework, and process inefficiencies.
- Enhance Productivity: Optimize tool performance and maintenance schedules, reducing human error and unplanned interventions.
- Reduce Costs: Lower operational expenses by improving efficiency, minimizing waste, and extending equipment lifespan.
- Gain Actionable Insights: Convert complex manufacturing data into clear, real-time intelligence, empowering factories to make proactive, data-driven decisions.
INFICON offers a range of proven, powerful, integrated software solutions designed to meet the diverse needs of modern manufacturing environments. Each solution builds upon the others, providing a scalable and adaptable FDC system. Our techniques are designed for success.
Featured Products

The foundation of INFICON's FDC system, FabGuard FDC provides real-time data integration, process control, analysis, and visualization, enabling engineers to predict and prevent process excursions. This is a leading FDC semiconductor tool.
- Seamless integration of process equipment and sensor data, comparing current performance to established baselines
- Edge computing for real-time response, including immediate alarms
- On-premises or cloud-based deployment
- Powerful run-by-run and real-time analysis capabilities
- World-class connectivity to sensors, gauges, IoT devices, and process tools, including temperature and pressure sensors
- Automatic Machine Learning (with SmartFDC® integration) for process and sensor data

SmartFDC automatically learns your processes and identifies anomalies, providing unparalleled fault detection and diagnostics capabilities without extensive configuration. SmartFDC®
- Automatic Machine Learning of equipment processes
- Comprehensive visualization and analysis tools
- Augments existing 3rd party FDC systems
- Easy-to-use interface for engineers of all skill levels
- Reduced implementation time and cost - improving the ability to quickly deploy FDC.

A knowledge-based, decision support system that streamlines maintenance activities, ensuring "First Time Right" repairs and minimizing downtime by providing actionable information. An essential part of a complete FDC system.
- Step-by-step guidance for preventative and corrective maintenance
- Comprehensive root-cause analysis tools, helping to discover the source of issues.
- Maintenance and activity tracking
- Flexible and dynamic workflow definition, adapting to various maintenance projects.
- Supports Best Known Methods (BKMs)

Subfab and Facilities Extends FDC capabilities to the subfab and facilities, enabling comprehensive monitoring and control for a greener, more efficient factory.
- Smart control and energy savings
- Condition-based consumption of resources
- Regulatory compliance and reporting
- Increased FDC tool and process fidelity
- Predictive maintenance scheduling, based on real-time parameter monitoring.
Seamlessly connects to a wide range of data sources, including sensors, gauges, tools, IoT, and other devices, and existing FDC systems. This includes comprehensive data collection.
Provides immediate insights into equipment performance, enabling rapid response to deviations with advanced fault detection software. Engineers can quickly analyze data to identify the root cause.
Leverages advanced algorithms to automatically learn processes, detect anomalies, and predict potential issues before they occur to provide automatic process control.
Designed for ease of use by engineers of all skill levels, with intuitive dashboards and visualizations.
Offers flexible configuration options and supports custom PyTorch for deep learning FDC solutions.
Easily scales from single-tool deployments to fab-wide implementations along the entire production line.
Connects with MES, SPC, and other factory automation systems for a unified environment, providing valuable feedback to optimize processes.
Solutions possible at the Edge, or in the Cloud.
Software-Driven Insights and Capabilities
Factory Dashboard
The Factory Dashboard is the principal operations reporting tool used by industry-leading fabs around the world.
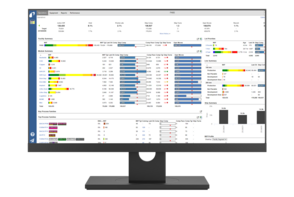
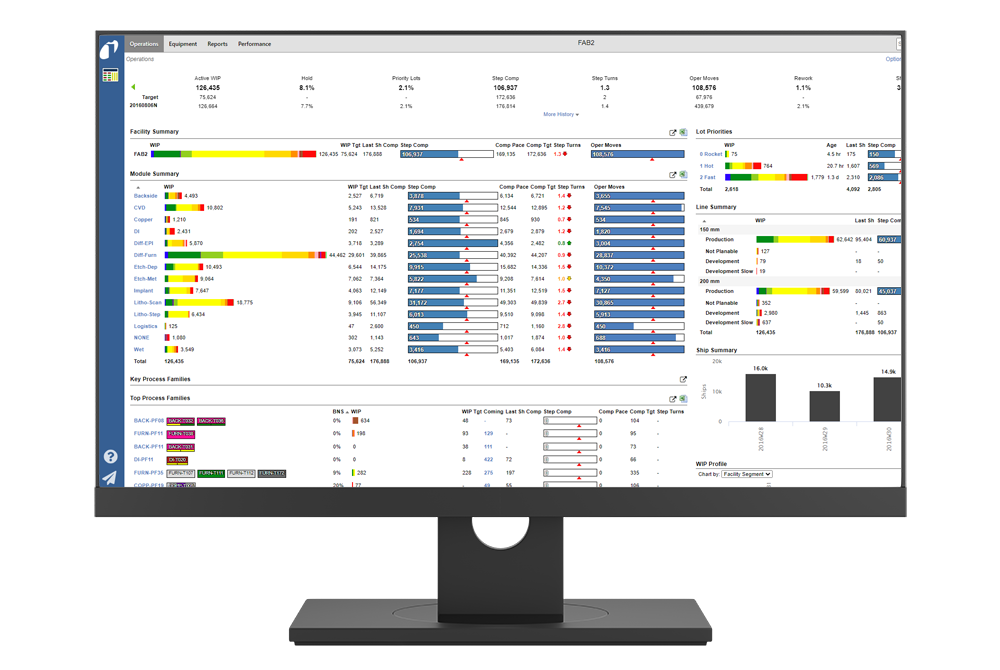
Factory Digital Twin
The Factory Digital Twin is the most critical building block for developing a Smart factory. It collects all the real-time operations events to compute cycle time and throughput data to drive powerful applications.
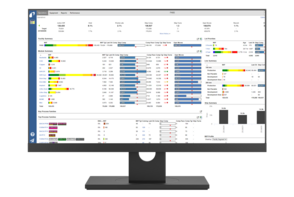
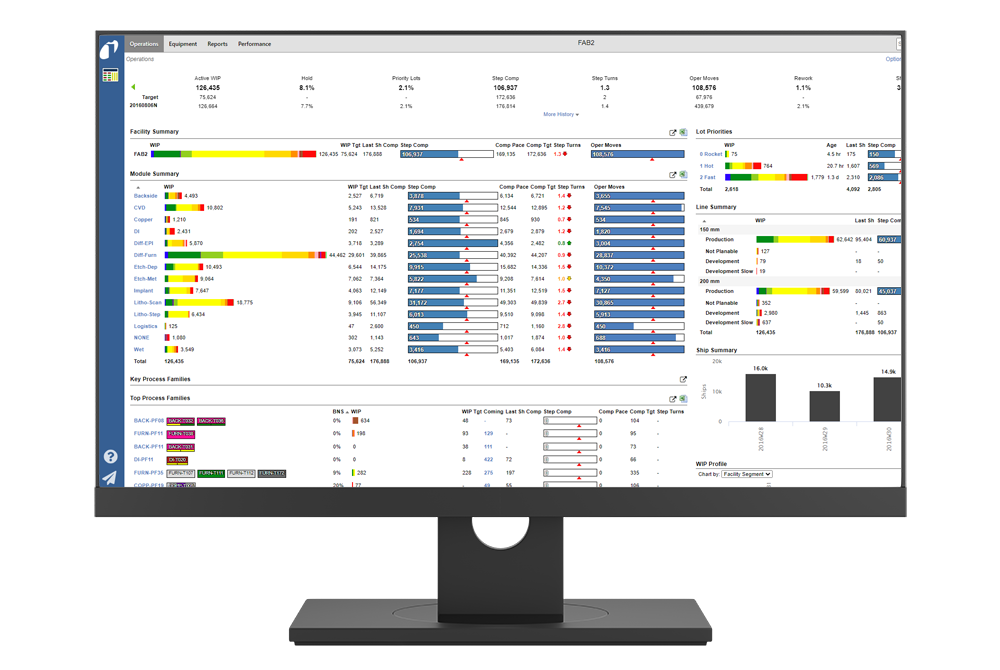
Factory Scheduler
Factory Scheduler utilizes Advanced Heuristics, Linear Programming, Optimization, and Intelligent Search Algorithms to generate a real-time optimized schedule that can be easily tuned to meet your manufacturing needs.
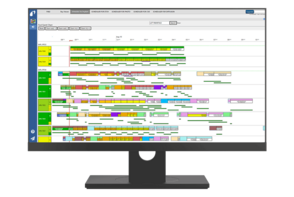
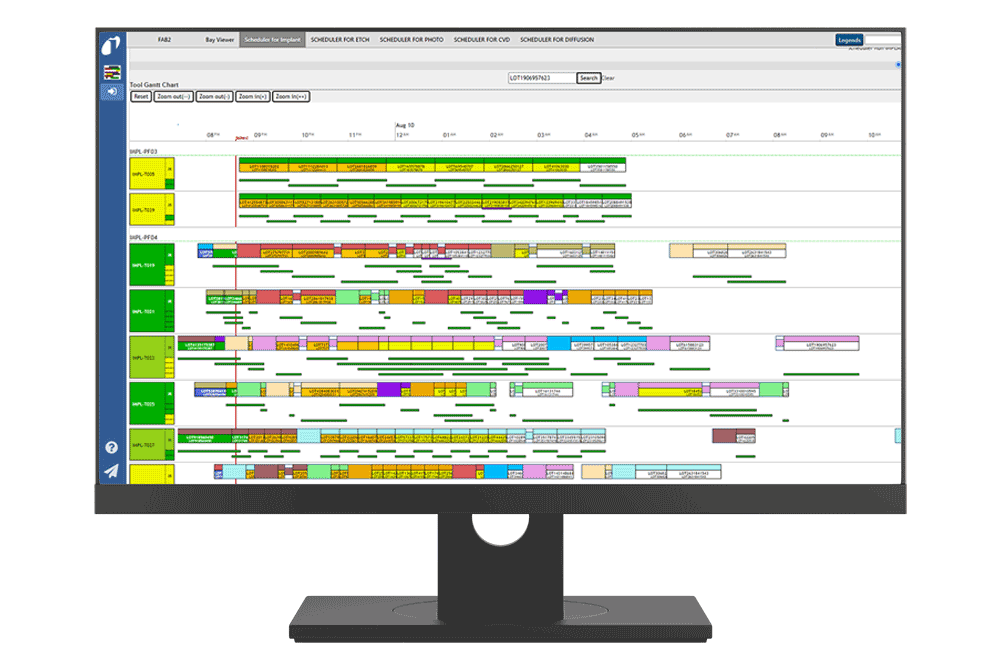
The INFICON Advantage
Expertise You Can Trust
INFICON is a leading provider of innovative instrumentation, critical sensor technologies, and advanced semiconductor software for the semiconductor and related industries. Our team of experienced process and equipment engineers is dedicated to helping customers achieve their manufacturing goals through:
- Deep Industry Knowledge: Extensive experience in semiconductor manufacturing and related high-tech industries.
- Global Support: Worldwide network of sales and service offices to provide responsive support.
- Custom Solutions: Tailored solutions to meet specific customer needs.
- Continuous Innovation: Ongoing development of cutting-edge technologies to address the evolving challenges of modern manufacturing.
Real-Time Monitoring and Alarming via Advanced Software Capabilities
Continuous Monitoring and Fault Detection
INFICON's FabGuard FDC software provides real-time monitoring of critical process parameters through its sophisticated data processing and analysis engine.
This continuous monitoring, driven by the software's algorithms, is essential for effective fault detection. The FabGuard software compares incoming data streams against pre-defined or dynamically learned performance benchmarks.
Proactive Alerts and User-Configurable Alarming Protocols
When deviations occur, the software proactively generates alerts and notifications, enabling operators and engineers to intervene before minor issues escalate.
The software's user-configurable alarming protocols allow for customized thresholds and notification methods, ensuring rapid response to process anomalies. FabGuard's software handles large data volumes in real-time, enabling timely adjustments that maintain production quality and prevent defects.
This software-driven approach is crucial for optimizing the manufacturing process.
Take the Next Step and Schedule your Demo Now
A core strength is its software's ability to seamlessly integrate with a wide variety of manufacturing equipment and data sources. This goes beyond just physical connections to include sophisticated data acquisition and communication protocols.
FabGuard's software acts as a central hub, expertly collecting and normalizing data from diverse sources such as process tools, sensors, gauges, IoT devices, and subfab/facilities components.
This integration creates a unified platform, allowing data from disparate sources to be analyzed together. FabGuard software facilitates data exchange and informed decision-making, supporting collaboration across process tools, metrology devices, and manufacturing data management systems. Ultimately, it provides a complete and accurate picture of the entire production environment for better control and optimization.