Real-Time Ampoule Monitoring and Leak Detection in Semiconductor Processes
INFICON SemiQCM sensors help fabs avoid disruptions, ensuring enhanced process stability and reducing waste
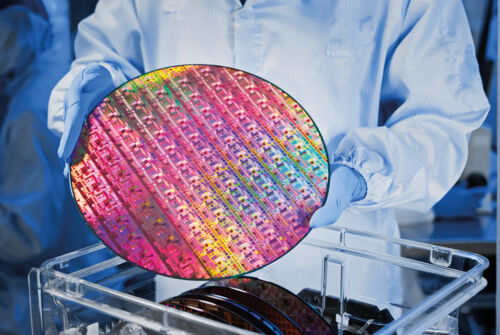
In the semiconductor industry, precision and consistency in fabrication processes are crucial. Advanced deposition techniques like chemical vapor deposition (CVD) and atomic layer deposition (ALD) rely on ampoules to store and dispense precursors to form thin films with exacting thicknesses and properties. If an ampoule runs dry mid-process without timely detection, it can result in film non-uniformities, defects, and device failures, jeopardizing the integrity of an entire wafer batch. Such disruptions degrade yield, escalate production costs, and waste valuable materials.
An INFICON SemiQCM® SR Sensor or SemiQCM® CR Sensor installed on the foreline of a semiconductor CVD chamber can detect faults with precursor delivery in real time. Using quartz crystal microbalance technology, the SemiQCM sensor combined with the INFICON IMM-200 frequency monitor can detect even the slightest changes in mass variations, providing real-time insights into precursor flow dynamics. Precursor delivery failures can be identified after the processing of as few as one wafer in some cases when the precursor has a high boiling point.
A great example demonstrating this achievement is molybdenum (Mo) precursor monitoring. By strategically positioning SemiQCM sensors along the foreline of semiconductor processing tools, where the temperature is lower than that of the process chamber, the sensors can detect changes in molybdenum pentachloride (MoCl5) or molybdenum dichloride dioxide (MoO2Cl2) precursor vapor condensation. As precursor (MoCl5 or MoO2Cl2) accumulates, it induces measurable frequency shifts due to the added mass.
A noticeable frequency drop corresponds to the accumulation of condensed precursor on the SemiQCM sensor, indicating the presence of precursor in the system. In contrast, a stable frequency suggests that no precursor is condensing on the sensor, signifying that the ampoule is depleted. By continuously monitoring these frequency variations, the SemiQCM sensor accurately detects precursor depletion, triggering alerts or automated responses to maintain process stability.
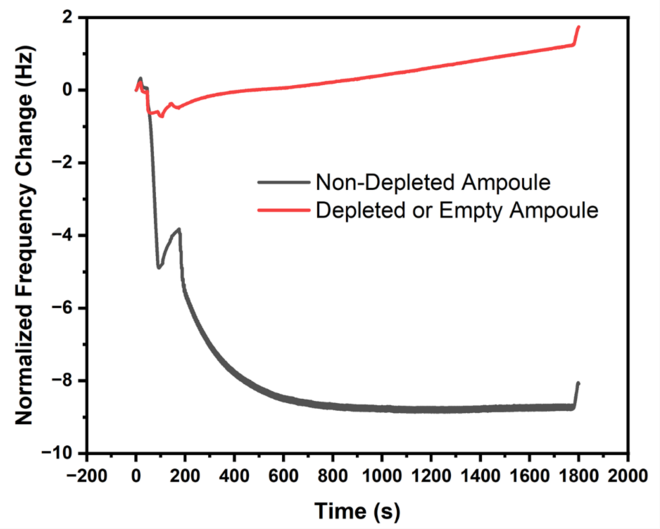
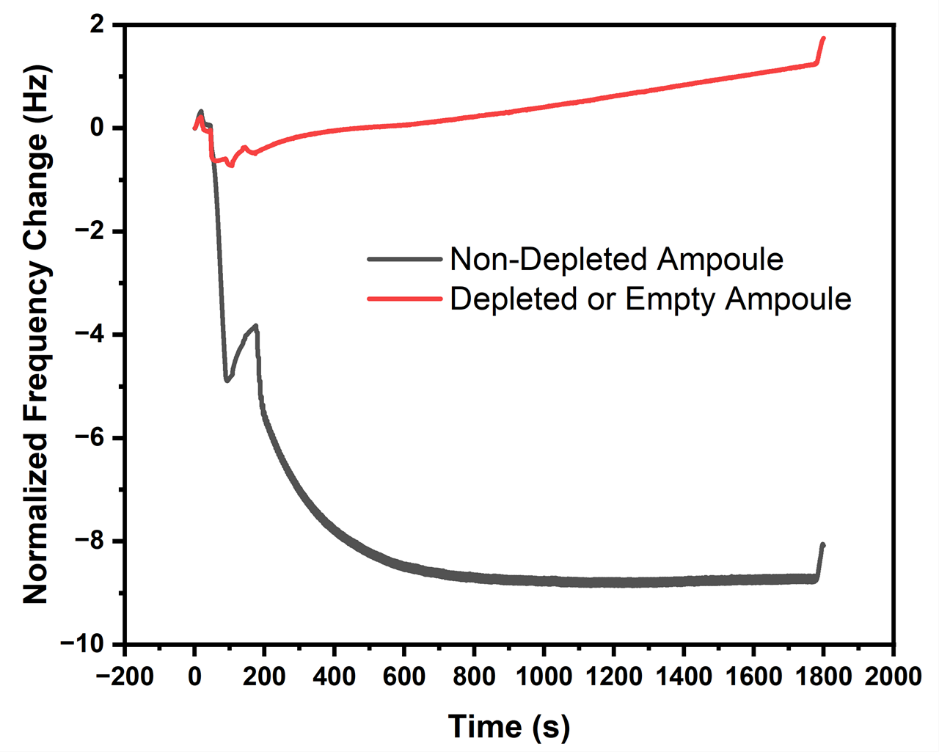
Learn more about ampoule depletion detection and leak detection with an INFICON SemiQCM sensor: Download the App Note
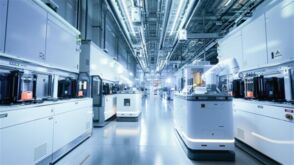
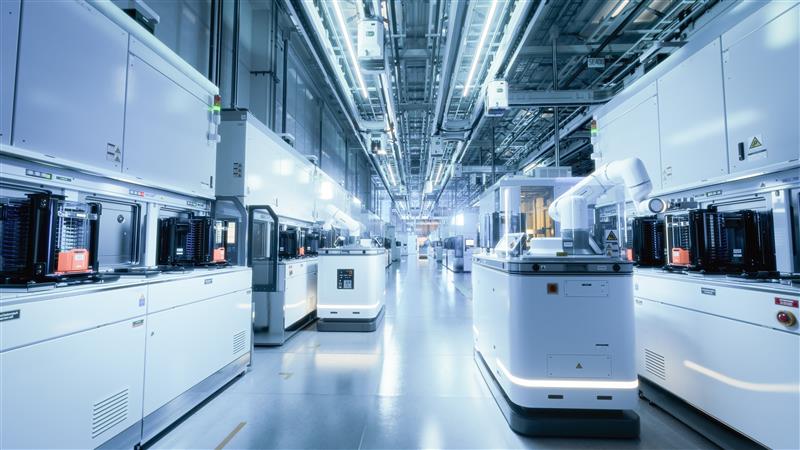
This continuous monitoring also allows the SemiQCM sensor to identify potential leaks within the chamber or processing system, ensuring enhanced process stability and reliability.
Under leak conditions, the SemiQCM sensor exhibits a more significant frequency shift due to oxygen (O2) intrusion into the carrier gas line, which reduces precursor (MoCl5 or MoO2Cl2) partial pressure and disrupts deposition. While the wafer experiences severe thickness loss due to precursor starvation, any MoCl5 or Mo on the SemiQCM sensor reacts with O2, forming a high-density Mo/O compound. This oxidation drastically increases the detected mass, causing a much larger frequency drop compared to normal conditions. This distinctly different frequency shift indicates abnormal precursor behavior, allowing for early leak detection and preventing potential process disruptions.
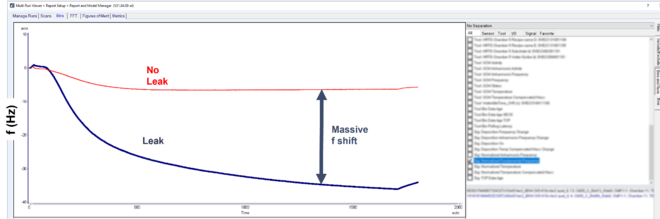
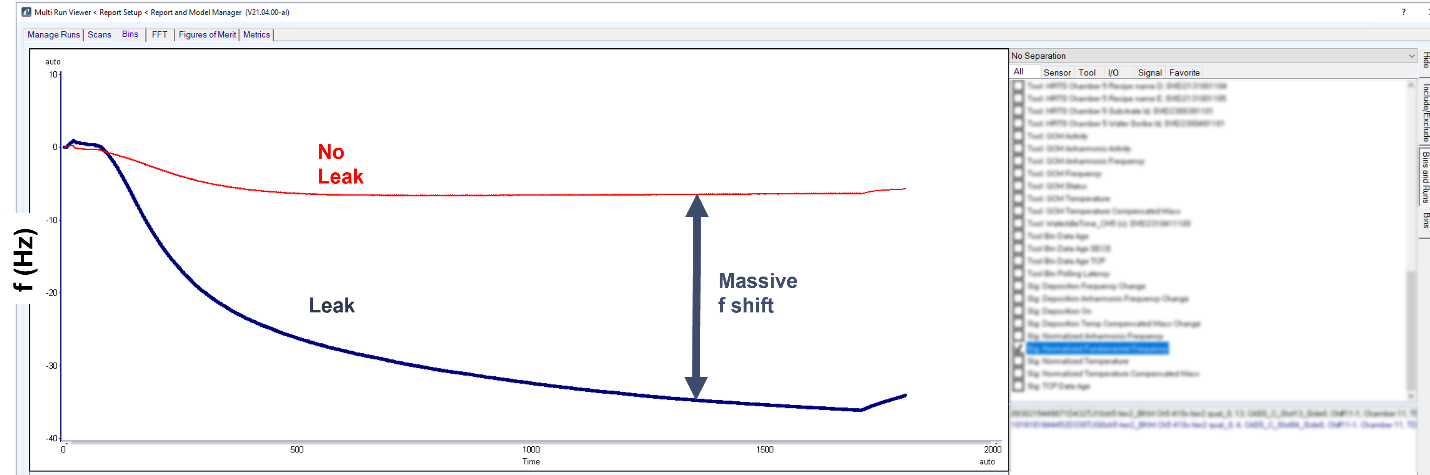
As semiconductor manufacturing continues to expand worldwide, unwavering precision and consistency at every stage of fabrication is crucial. By leveraging the benefits provided by a SemiQCM sensor, semiconductor manufacturers can ensure real-time process stability, minimize defects, and optimize production efficiency.