What Makes an Effective Daily Fab Status Meeting?
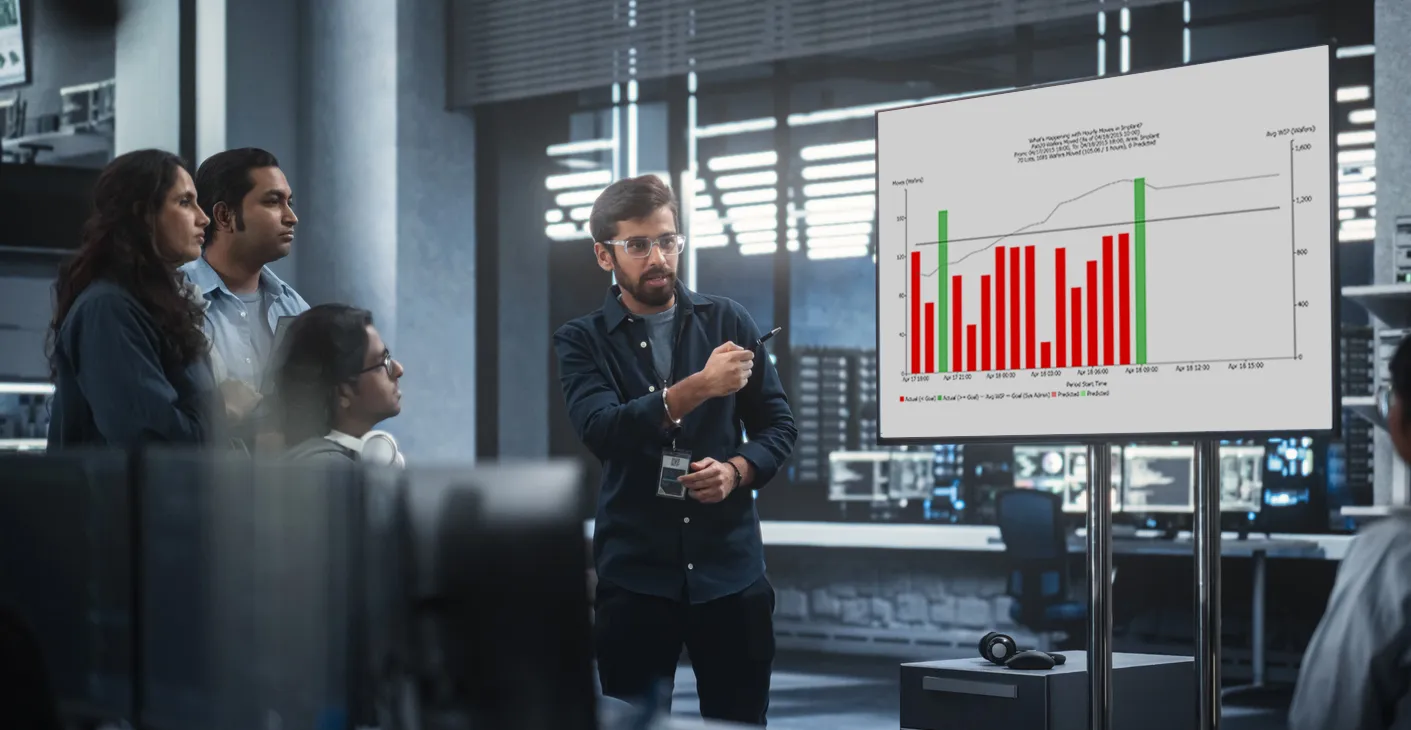
Nearly all fabs hold a daily fab status meeting. Usually less than an hour long, this meeting is the daily get-together for the fab manager and production, equipment, and process managers. With so many people in the room and the opportunity cost of what these attendees could accomplish instead were they to have an uninterrupted hour of time at their primary job, this article explores, “What elements makeup an effective daily fab status meeting?”
1) To distribute relevant information (the “State of the Union” for the fab)
The distribution of information often takes most of the allotted time during a fab status meeting. Examples of what is discussed include:
- Review down tools, report the reason for the current delay (waiting for parts, waiting for install, waiting for qual, etc.), the impact on production, and an estimated uptime.
- Review WIP location across the line (by priority or product family).
- Review constraint performance for the prior day and week-to-date.
- Review progress toward daily and weekly goals.
- Review each rocket lot, report its current location, holdups yesterday, and expected travels today.
- Review moves/turns/scrap/shipments performance for the prior day and week-to-date.
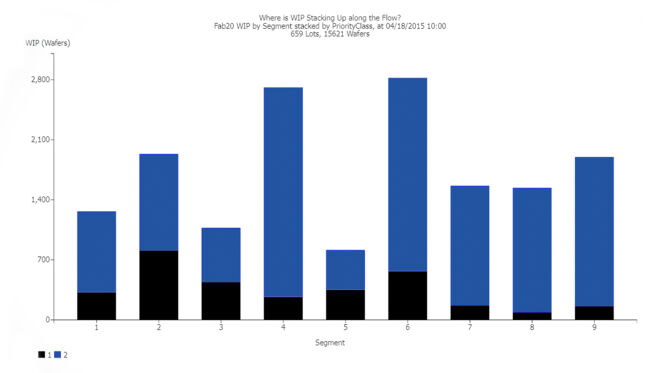
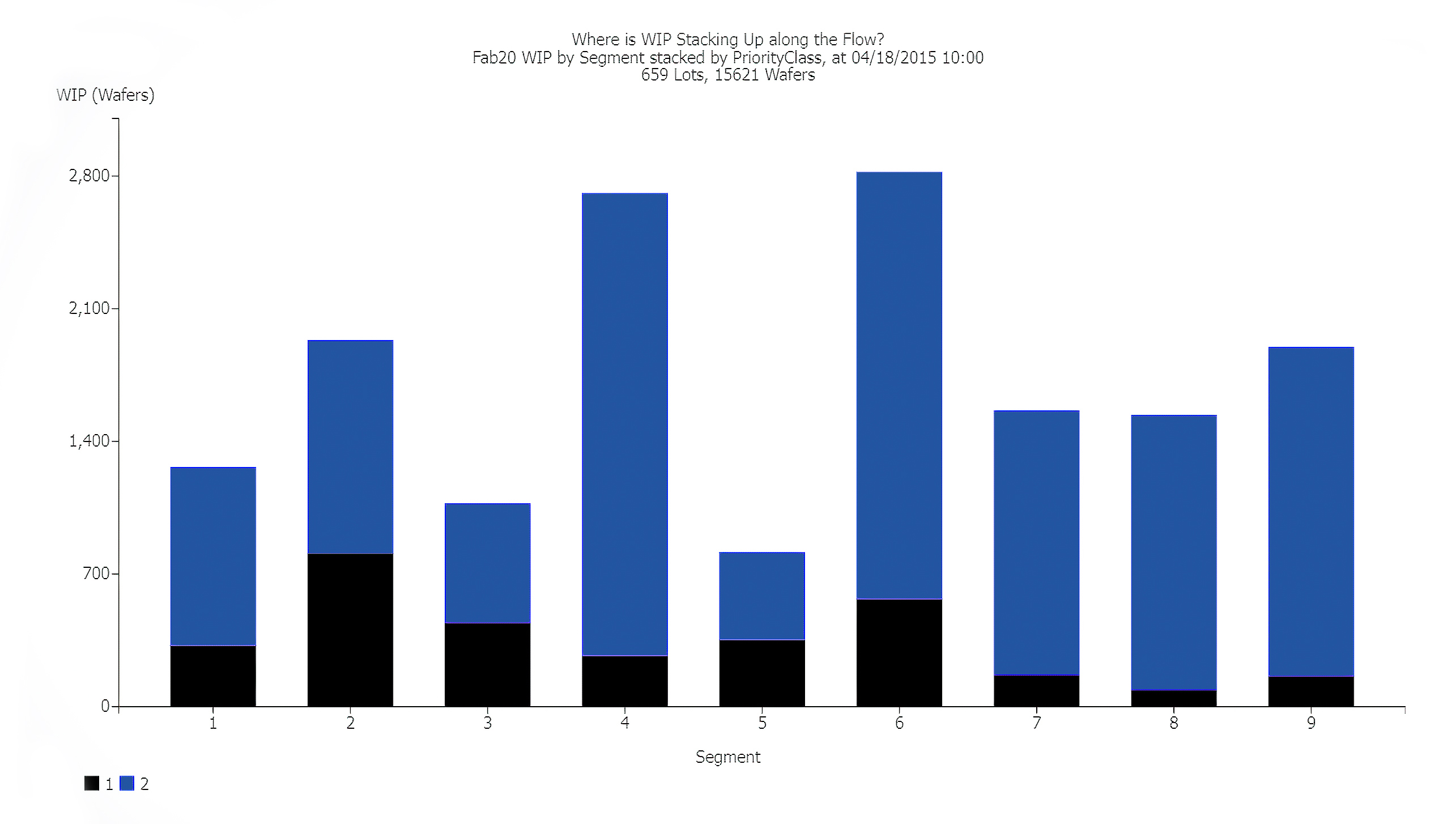
2) To hold individuals responsible for meeting goals
As part of the review of progress against goals, individuals can be put on the spot at fab status meetings if the performance for their area is falling behind (as shown with the Implant moves in the image to the right, generated from our FabTime Flexible Reporting module, with poor performance relative to goal over recent hours). Depending on company culture, these encounters can range from a friendly jousting to an emotionally charged confrontation.
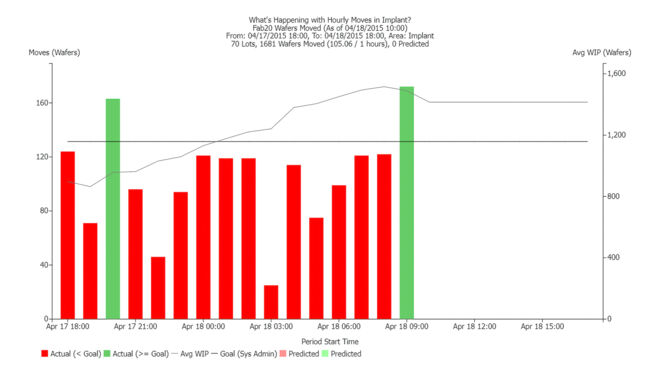
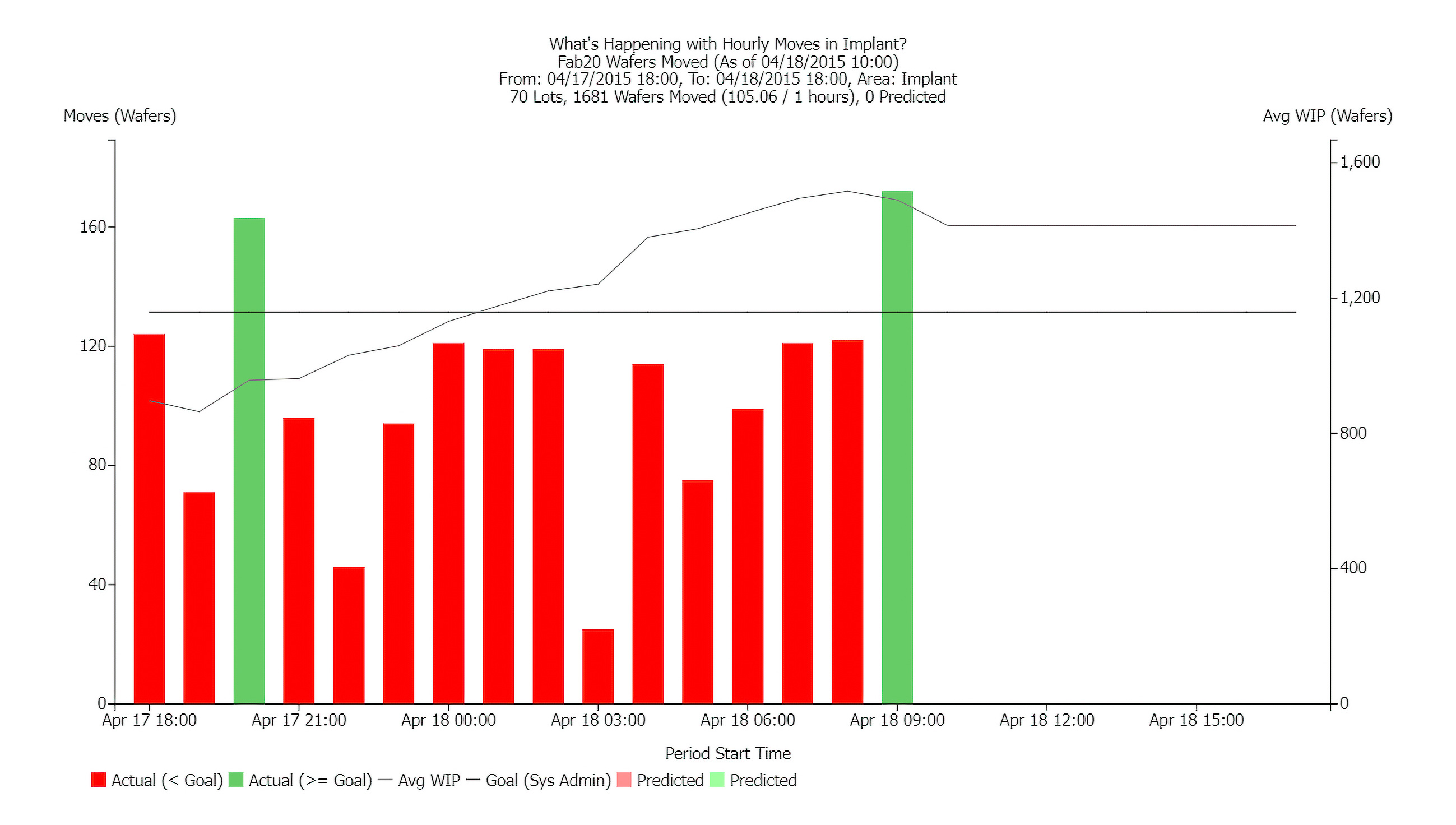
3) To make necessary decisions
Decisions regarding priorities, resources and support can be made during the status meeting, such as:
- Elevating the priority of a particular lot due to a request by its owner.
- Prioritizing limited equipment engineering resources against down tools, improvement projects, etc. Equipment personnel know what is happening with down tools, equipment install, etc. Production personnel know the relative pain of work that cannot be processed due to equipment problems. Between the two sides, an agreement must be reached on priorities.
- Scheduling requests by CIM or IT for support system downtime.
4) To brainstorm solutions to an important problem
A small portion of the agenda can be allocated to brainstorming. This brainstorming often appears in an ad-hoc way in response to a report that is being given, e.g.:
- A constraint tool was starved for nearly an hour this morning. Why wasn’t there sufficient WIP to keep it running? What needs to change to keep it busy in the future?
- Scrap was a problem yesterday at operation X. What happened and can we prevent it from happening again?
- WIP is piled up in the front end of the line, what can we do about that?
In general, brainstorming is likely done elsewhere, and the results are reported at the morning meeting.
How Should the Daily Fab Status Meeting Be Structured?
Suppose the time allocation at a typical fab status meeting is:
- 70% to distribute information.
- 20% to hold individuals accountable.
- 5% to make decisions.
- 5% to brainstorm solutions.
Is this the right mixture? Are these the right things to do each morning? Is there a way to prune topics that are not required, to leave time for those items that are important and can only be accomplished in a meeting of production, equipment, and process personnel? It is recommended that the team return regularly to first principles, say once a quarter, and ask:
- What is the purpose of our fab status meeting? Is our meeting agenda structured to achieve this purpose?
- Is each topic or report on the agenda still relevant, or was it added in response to a special situation that no longer exists?
- How good are we at assigning responsibility for necessary actions that come from the morning meeting?
- How good are we at following up to confirm that assigned actions have been completed, or cancelled if no longer necessary?
- Can we make our presentation of information more compact, so that we may cover more material in the same time, or the same material in less time?
- Is there communication that we can have outside of the fab status meeting, to reduce the time required for the meeting itself?
- Can we improve our productivity by decreasing the amount of preparation time required for the meeting?
These last three are areas in which Smart software solutions from INFICON can help.
What Content Is Most Important to Cover in the Fab Status Meeting?
The preceding sections convey general thoughts about the structure of a daily fab status meeting. But what about the content? What’s most important to look at? Three categories of content that are helpful to include here are current problems, KPIs, and predictions.
Problems: The most value-added thing to cover in the daily status meeting is the list of current problems or anomalies, particularly those where decisions or action are required. This might include:
- Bottleneck tools with a significant quantity of “standby-WIP-waiting” time and/or “post-processing time” in the past day. These tools may lack sufficient operators to avoid forced idle time.
- Tools that are currently down and have been down for some number of hours.
- Hot lots that are not in process (especially hand-carry lots).
- Hot lots and/or lots for key customers that are behind schedule.
- Lots on hold for more than some period of time.
- Operations that have WIP waiting where there is only one qualified tool (unless that tool is a true one-of-a-kind tool).
- Tools that are cross-qualified, but are registering fewer moves than expected. Often this is due to soft dedication (operator preferences).
- Lots that have reached a “future hold” step where the engineer is out of office.
- Tools where the hours of WIP waiting to be processed per tool are greater than shift length (these are short-term bottlenecks).
- Tools where the average x-factor per visit for lots moved recently is highest in the fab (these are cycle-time bottlenecks).
Of course, it’s most useful to discuss these issues if each discussion concludes with a plan of specific action by specific people. Something that we’re excited to be working on at INFICON is generating a list of these problems automatically, and ranking them by impact on fab performance, so that your precious meeting time can be used to address your most pressing issues.
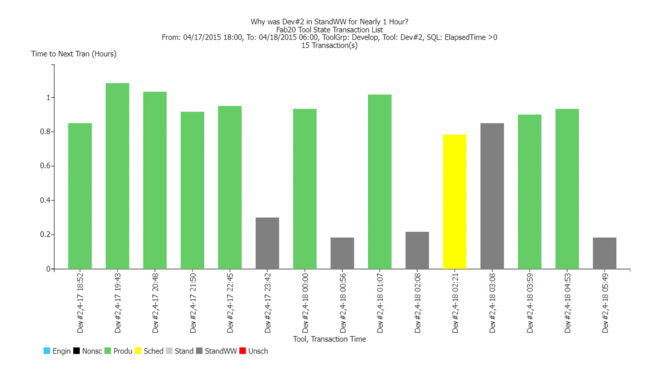
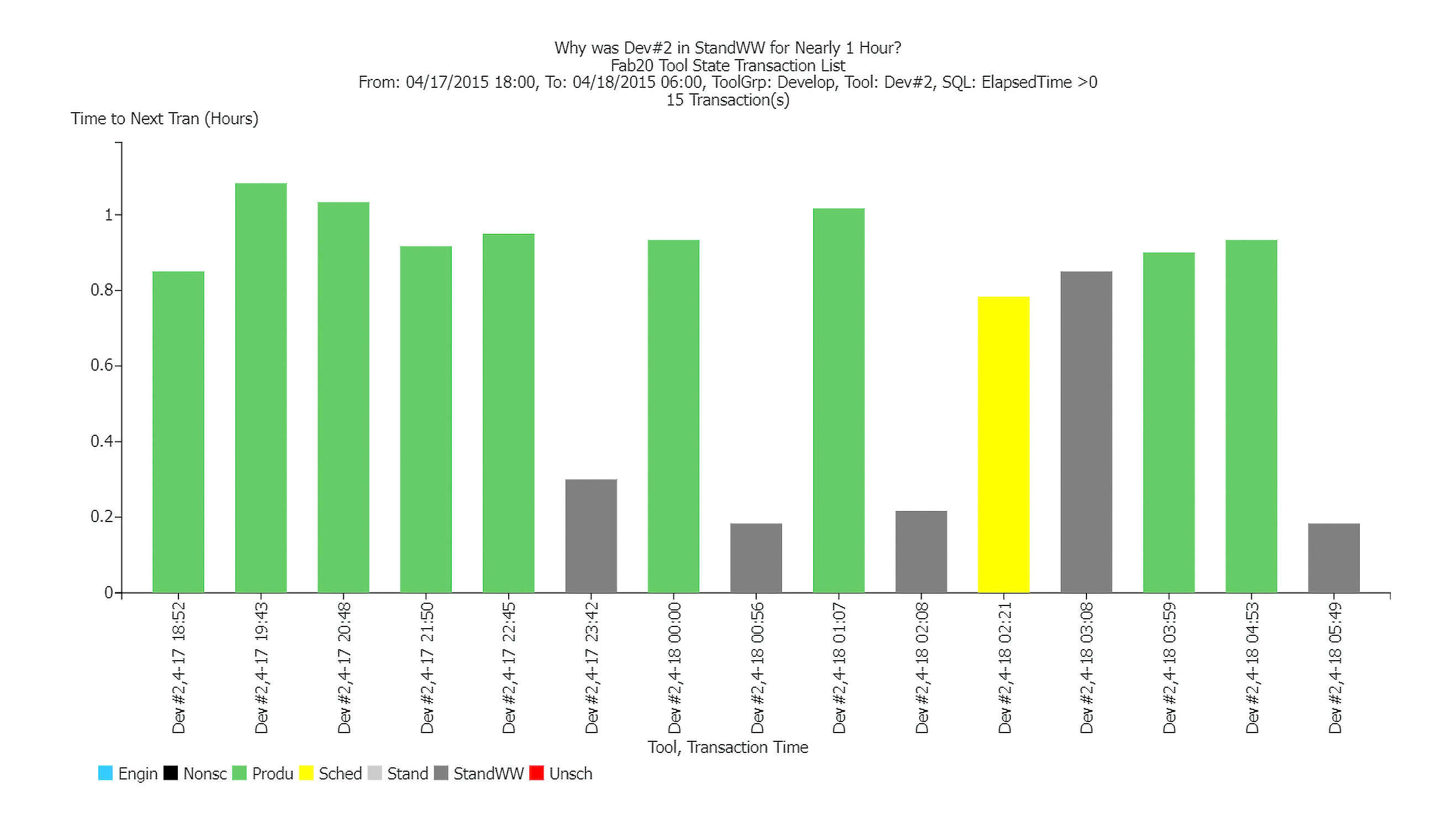
KPIs: It remains important to keep an eye on the fab’s overall key performance indicators, including:
- On-Time Delivery and Cycle Time for shipped lots
- Starts
- Shipments
- Moves
- WIP (total and profile by segment of the line)
- WIP Turns (moves / average WIP)
- Scrap and Risk WIP - Risk lots are marked as not shippable but not scrapped yet
- Priority Lots, Lots on Hold, and Idle or Static WIP (WIP that has been in queue for more than some threshold, e.g., 12 hours)
- OEE Outliers - Break down OEE into its components: Availability, Performance, and Quality, to identify areas for improvement in equipment efficiency
- Current Capacity Bottlenecks by Tool Group and Area
These are core metrics that demonstrate the overall health of the fab. In all cases, these charts should be displayed relative to a goal, either an automated goal, or a chart stripe that indicates a goal region. Looking at the current data as well as the trend for the week gives a manufacturing team a quick idea of the fab’s progress.
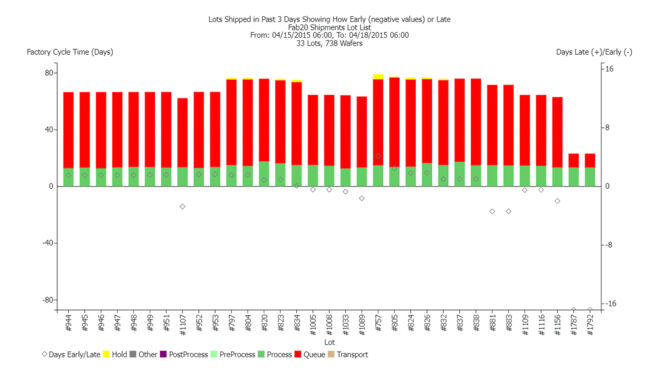
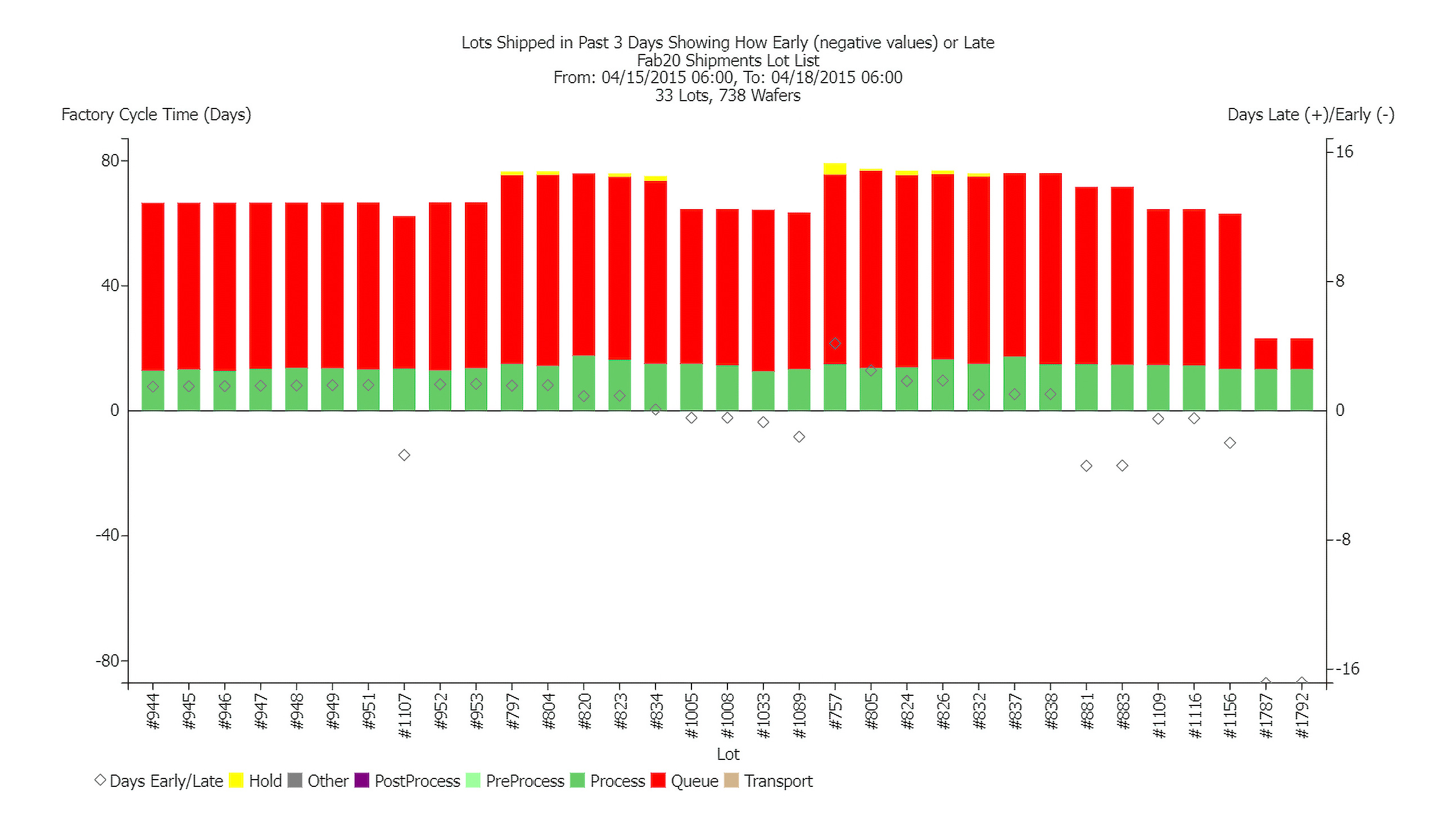
Predictions: You will also want to keep an eye on expected future performance. The idea here is to make sure that the outcomes predicted by current conditions are acceptable. If not, it’s better to learn about any problems now, so that you can course-correct while there’s still time. Some things to look at here include:
- Forecast outs: What WIP do you expect to ship this week? Will it be on schedule?
- Future cycle time: Based on current performance, what do you expect your cycle time to be in the future? A metric to use here is Dynamic Cycle Time, as discussed in the FabTime Newsletter Issue 24.03. Dynamic X-Factor can also be used, as discussed in Issue 9.04. If you would like a copy of a past newsletter, contact https://www.fabtime.com/contactfabtime.php
- Planned and predictive maintenance: What major scheduled maintenance do you know is going to take place in the next few days? Are there measures that should be taken to mitigate the impact of these events?
Fabs of the future will become better at using AI and machine learning to predict output, cycle times, process problems, and both scheduled and unscheduled downtime events. INFICON is currently working with manufacturers to increase the use of AI in factory operations and process control. This includes Smart Scheduling and Machine Learning fault detection techniques.
Conclusions
The daily status meeting sets the tone for the fab. Fabs that hold effective daily status meetings are also likely to be effective at achieving their manufacturing goals. A morning meeting is effective if it routinely achieves its stated purpose, whether that is to distribute information, hold individuals accountable, make decisions, brainstorm solutions, or another purpose specified by fab management.
Want to Learn More About our Products and Applications?
Our newsletter offers regular updates on our latest products, applications, upcoming events, and other interesting news.