Soapy Water Leak Detection: A Method with Limitations
The Hidden Costs of Using Soapy Water for Leak Detection
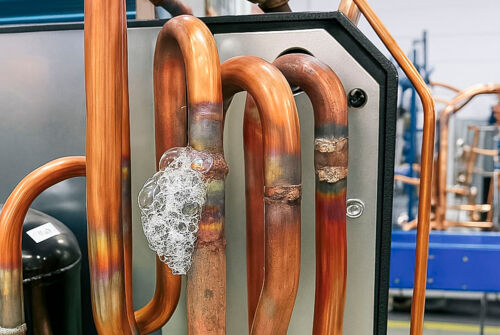
For decades, the soap and water method has been a go-to tool for leak detection in pipes, valves, and fittings. The technique is as simple as it is effective—apply a soapy liquid to the suspected area, observe, and wait for bubbles to reveal a leak. No bubbles? No leak. The visual simplicity of the soap solution test is why many users continue to rely on it.
Like any tool, the soapy water test has both advantages and drawbacks. This article will explore the strengths and limitations of using soap and water for leak detection, offering valuable insights on its cost-effectiveness and key considerations.
Advantages of the Soap and Water Method
- Ease of Use: Applying soap and water requires no special training or expertise. Simply brush, spray, or wipe the solution onto the area in question and observe.
- Straightforward Interpretation: The results are easy to understand. Bubbles mean a leak, and no bubbles mean no leak.
- Inexpensive: Soap and water are accessible, cost-effective materials. There are no expensive tools or equipment required.
- Non-Invasive: Unlike some methods that involve pressurizing systems, soap and water testing is “gentle” and can hardly damage the system being tested.
Drawbacks of the Soap and Water Method
- Limited Efficiency on Large Leaks: Very tiny leaks may go unnoticed. The soap method is effective for detecting larger leaks (typically down to around E-3 mbarl/s).
- Gravity Challenges: Soap solutions tend to flow downward due to gravity, making it difficult to keep the solution on joints, especially vertical or overhead ones. This can lead to incomplete coverage and missed leaks.
- Out-of-Sight Areas: Pipes and fittings are sometimes located in hard-to-reach or poorly lit areas. These factors can make it nearly impossible to observe potential bubbling.
- Sharp Edges: Some surfaces, such as sharp metal edges or irregular fittings, can pop bubbles before they fully form, making leaks harder to detect.
- Time-Consuming Clean-up: After testing, the soapy residue must be cleaned and dried, especially in environments where cleanliness is critical, such as food processing or medical applications.
- Hazard Risks: Using slippery substances increases the chances of accidents, such as slips and falls, which can be particularly dangerous in workplaces with heavy machinery or elevated platforms.
- Soap can Block Smaller Leaks: The surface tension of the soap solution can create a thin, almost "sticky" film over the leak site. This film may act like a barrier, partially or completely covering the leak and preventing tracer gases or other detection methods from finding it later.
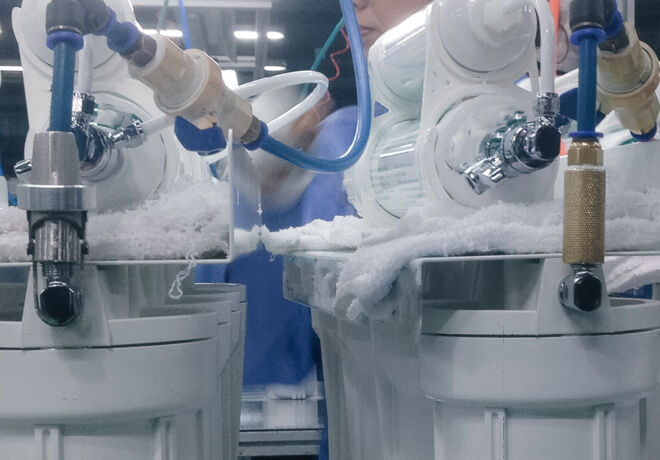
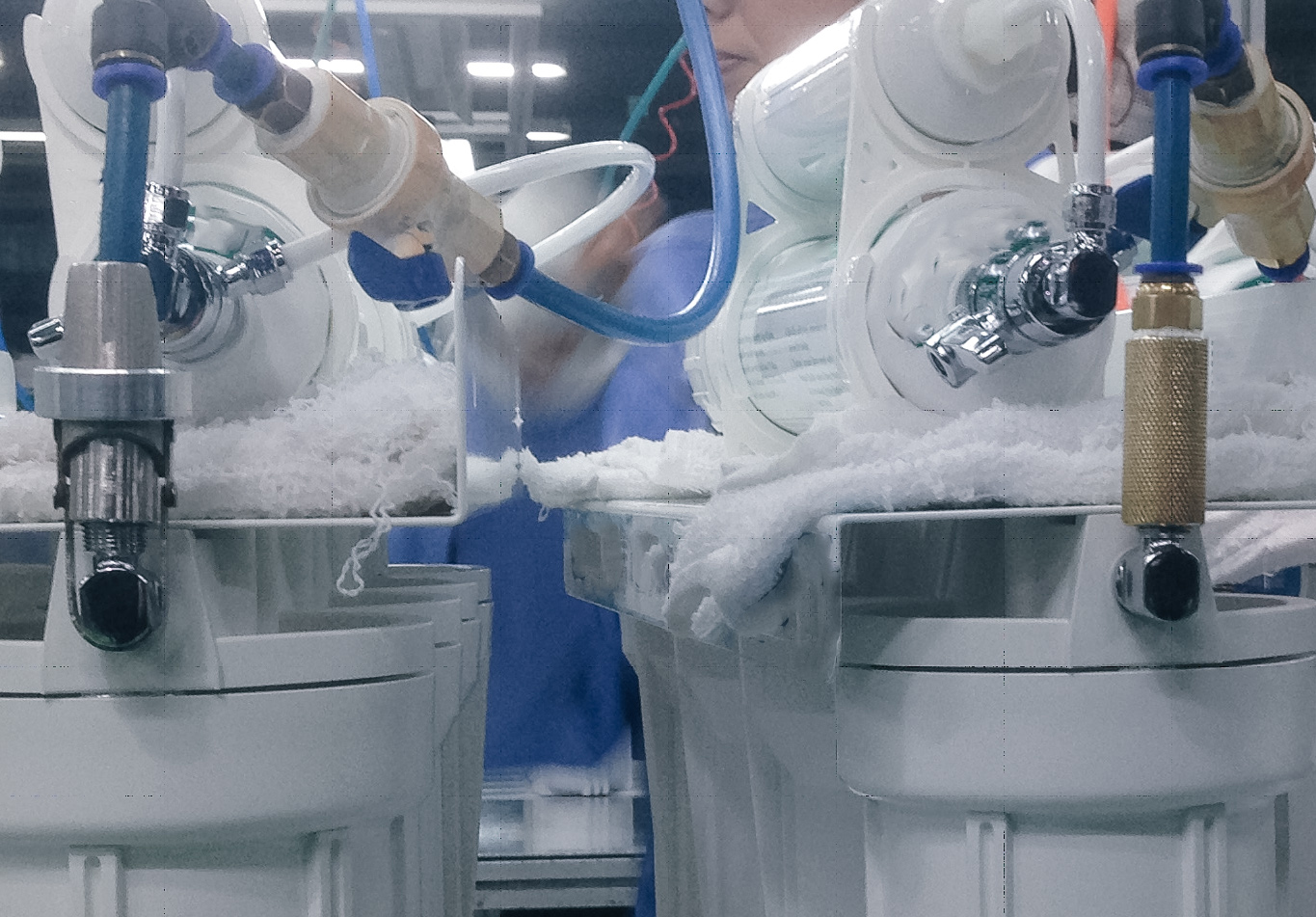
A User’s Perspective: The Viscosity Dilemma
Viscosity plays a significant role in how well the solution adheres to surfaces and forms bubbles. A solution with lower viscosity might flow off too quickly, especially on vertical or inverted surfaces, reducing its effectiveness in detecting leaks. Conversely, a solution with higher viscosity can cling better to surfaces, allowing for more effective bubble formation, but if it's too thick, it might fail to bubble easily, especially for smaller leaks.
Users commonly experience problems when relying on soap and bubble formation to detect micro leaks. While the method excels at spotting larger leaks, its precision falters when dealing with very slow leaks.
Cost-Effective Leak Detection with a Fast Return on Investment
When considering industrial leak detection for low volume or repair lines, soap spray and water bath are often favoured due to cost concerns. However, cost-effectiveness in leak detection should be considered as a comprehensive factor, not just the initial investment. While up-front costs are often the focus, the payback aspect is just as important for evaluating the overall value. In many cases, technologies that initially appear more expensive can provide significant long-term savings through faster leak detection, reduced warranty claims, and ultimately enhance a company's reputation and trustworthiness with customers.
The Sentrac leak detector fills the gap between low-cost methods and costly, advanced leak detection solutions. It offers a compelling alternative with a short payback period, thanks to its modest purchase price and minimal installation and maintenance costs. By moving to Sentrac, even the smallest leaks are detected quickly and accurately making it a worthwhile investment for industrial users.
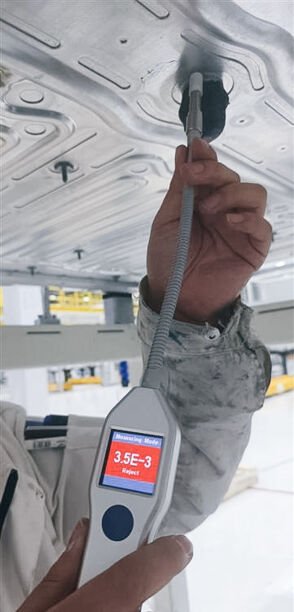
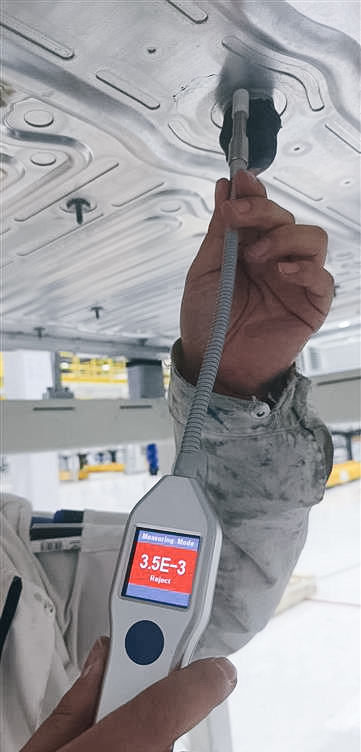
Still using traditional leak detection methods?
Are you still using traditional leak detection methods such as water bath or soap spray and looking for a more efficient solution? Download this paper or watch our on-demand webinar and learn more about efficient hydrogen sniffing leak testing.
Want to Stay Updated on Leak Detection?
Our newsletter offers regular updates on our latest products, applications, upcoming events, and other interesting news.