Optimize Selective Etch Processes with Residual Gas Analysis
By better understanding and controlling etching dynamics, manufacturers can achieve improved device uniformity and reduced variability.
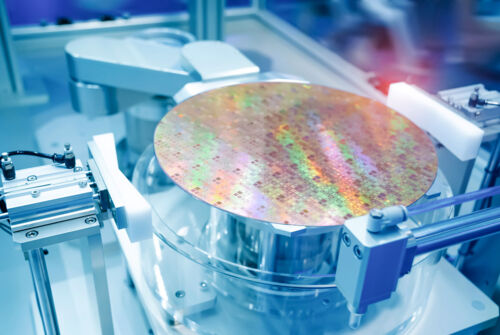
Semiconductor manufacturing is at the heart of technological advancement, driving innovations in electronics, computing, and communication. As devices become more powerful and compact, the industry is pushing the boundaries of miniaturization, striving to fabricate high density chips at the nanometer scale. This presents unique challenges for complex device structures within the transistor, particularly in the etching processes.
INFICON is at the forefront of addressing these challenges, leveraging our expertise in advanced instrumentation and sensor technologies. By providing solutions such as next-generation mass spectrometry and in situ gas analysis, INFICON is helping manufacturers optimize etching processes, ensuring precision and efficiency in semiconductor fabrication.
Selective Etching in Semiconductor Manufacturing
Etching is a fundamental process in semiconductor manufacturing, playing a critical role in chip fabrication. Traditionally, etching intentionally removes and deposits material to create structures on a silicon wafer. The process begins with a substrate, typically covered with an oxide layer, followed by the application of a photoresist. This setup undergoes lithography, where light exposure alters the photoresist, allowing selective removal of exposed areas to form precise patterns. These patterns guide the etching process, enabling the construction of intricate structures within a chip. This creates a harsh environment for sensors.
With the move to 3 nanometer node and below, Gate-All-Around (GAA) structures mark a significant evolution in semiconductor design from FinFET, requiring etching processes that can move beyond traditional straight-line etching to accommodate complex 3D structures. This demands higher precision and control, as manufacturers must etch both vertically and laterally to achieve desired configurations.
Selective etching involves tailoring the etching process to target specific materials while preserving others, enhancing the ability to create complex device structures with high accuracy. Selectivity is crucial for optimizing GAA chip design and ensuring uniformity and quality in the final product. At smaller scales, precision becomes paramount, as even minor deviations can have a substantial impact on device performance and quality. The intricate structures required for advanced chips demand etching techniques that can navigate multi-directional challenges, ensuring that materials are removed and deposited with exacting accuracy.
One of the primary challenges faced by semiconductor manufacturers is controlling etch rates and selectivity to achieve the desired device configurations. This must be meticulously managed to ensure the etching process aligns with the design specifications, maintaining the integrity and functionality of the chip.
INFICON’s expertise in sensor technologies and real-time gas analysis provides valuable insights, helping to refine etching processes to meet the demands of next-generation semiconductor devices.
Selective Etch Process Optimization
The Transpector APX mass spectrometer from INFICON is designed to withstand the harsh environments typical of advanced etching processes. Equipped with specialty coatings and heating capabilities, the APX is durable and reliable even in the harshest conditions.
Utilizing in situ gas analysis can give manufacturers more real-time insights into the chemical reactions occurring during etching. By analyzing the gases involved, manufacturers can optimize their processes, enhancing precision and control over etch rates and selectivity. This capability is crucial for better understanding how to enhance the selective etch process.
INFICON sensors play a pivotal role in real-time chemistry monitoring, providing a window into the complex dynamics of etching. They enable manufacturers to observe and adjust processes on the fly, ensuring optimal performance and quality. By leveraging these advanced tools, manufacturers can better understand the intricacies of their etching processes, leading to improved device uniformity and reduced variability in semiconductor fabrication.
Optimize Your Processes
Contact us today to explore how our solutions can support your process development and help you achieve your manufacturing goals: Fill out our form
Process Development and Optimization
INFICON collaborates with Integrated Device Manufacturers (IDMs) to refine their etching processes. By gaining deeper insights into their etching dynamics, leading to significant improvements in process control and device quality. This collaboration enables IDMs to optimize their etch rates and selectivity, ensuring that their chips meet the stringent requirements of sub-3 nanometer technology. These partnerships demonstrate INFICON’s commitment to advancing semiconductor technology and supporting the industry’s evolution.
As the semiconductor industry advances toward sub-3 nanometer technology, the challenges and innovations in etching processes become increasingly significant. With the demand of unprecedented precision and selectivity, manufacturers must navigate these complexities to ensure device performance and quality, making the role of innovative etching technologies more crucial than ever.
INFICON stands out as a key partner in this evolving landscape, offering cutting-edge solutions such as next-generation mass spectrometry and real-time gas analysis. These innovations provide manufacturers with the insights needed to optimize their etching processes, ensuring precision and efficiency in semiconductor fabrication. By better understanding and controlling their etching dynamics, manufacturers can achieve improved device uniformity and reduced variability.