Hydrogen Leak Detection in Potentially Explosive Environments
How to safely search for leaks on aircraft fuel tanks
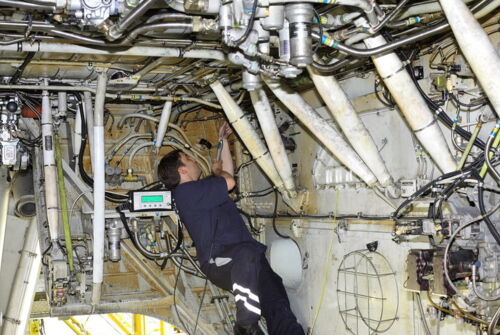
Wing fuel tanks and other hazardous locations, where fuel leaks can lead to explosive atmospheres, require stringent safety measures to protect personnel and ensure system integrity. Fuel leaks present significant risks, including fire hazards and potential system failure, making leak detection and prevention critical in maintaining safety. Effective detection methods are essential for identifying leaks early and mitigating the dangers associated with fuel exposure in these high-risk environments.
Hydrogen leak detection in potentially explosive environments is a critical aspect of industrial safety, aimed at identifying and mitigating the risks associated with the use of this gas. As industrial processes continue to evolve, ensuring the development and implementation of effective hydrogen leak detection technologies is crucial to upholding a secure and productive work environment.
INFICON is a pioneer in hydrogen leak detection and has expert knowledge on the specific challenges present in potentially explosive settings, as well as on the leak detection technology used to safeguard against the potential dangers inside these environments.
The solution from INFICON
Extrima® is an intrinsically safe hydrogen leak detector certified for Zone 0 and Division 1, Class I, locations which means that it is allowed also under conditions where explosive atmospheres exist even under normal operating conditions. It is further rated for locations with gases in all gas groups (excluding acetylene) and with ignition temperatures at or above 200°C (392°F). The detector is designed for use under the toughest physical conditions, with IP67 rating and material selections to withstand very aggressive chemical substances.

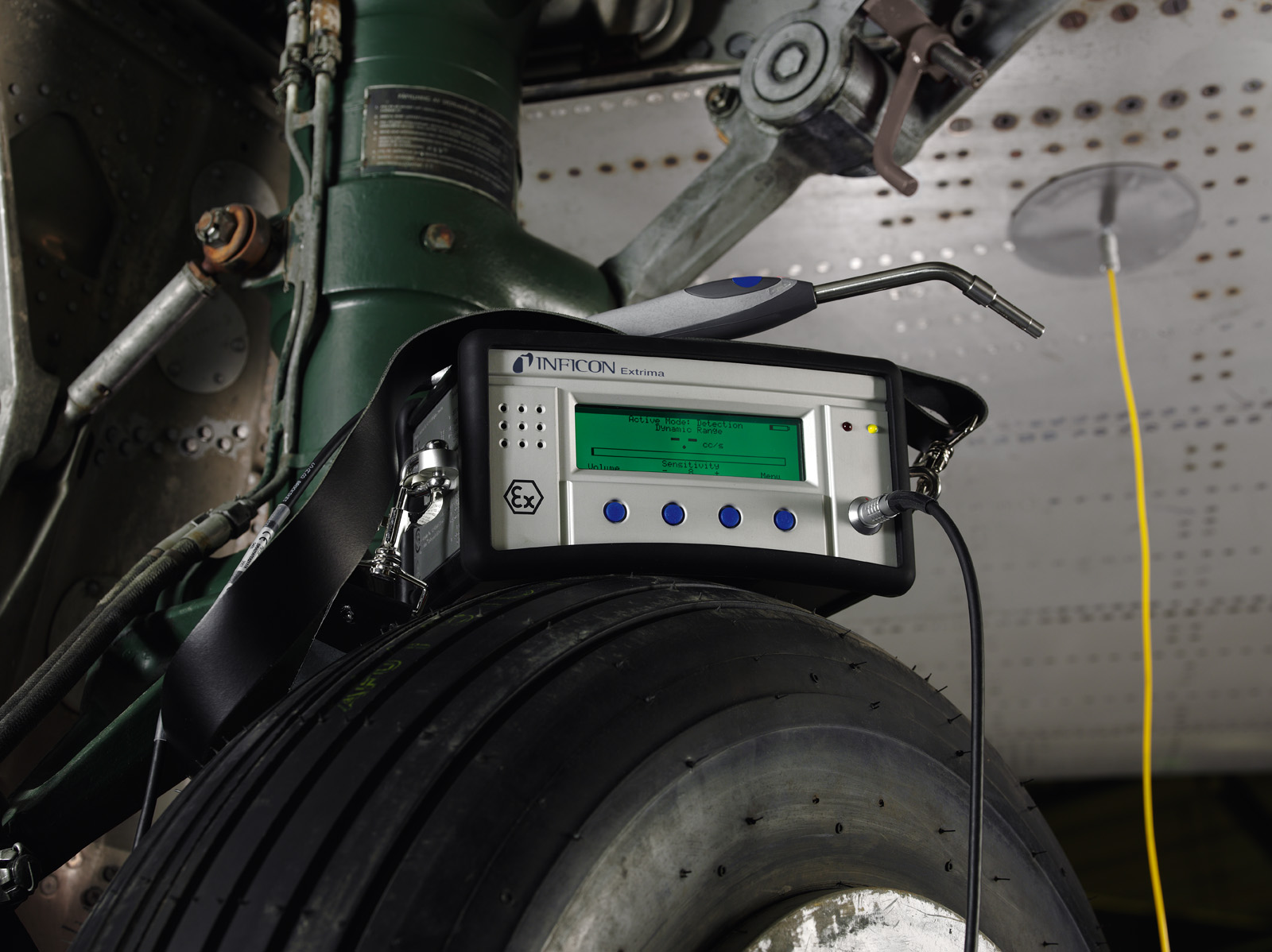
One example of such harsh environments where Extrima has been successfully employed is in integral fuel tanks on aircraft. Traditional methods of locating the source of spotted leaks involve draining the tank and locating the same spot inside the tank. Thorough analysis of the construction should be used to determine if further resealing is required. The tank is then refueled after completed repair to verify that the leakage has been eliminated. If not, which is quite common, the whole procedure, including defueling, sealant stripping, cleaning and so on must be repeated.
Using tracer gas is much faster and more reliable. The US Air Force, Technical Manual TO 1.1.3 mentions the hydrogen-nitrogen method as the most sensitive method for locating the leak source.
Use an injection pad or mastic and tube adapters to connect gas to the leak exit point on the skin of the aircraft. Feeding the hydrogen mixture to the exit point, the gas will follow the leak path and escape at the leak source, that is the point where the fuel passes the seal into the structure.
Using a highly sensitive, selective and fast leak detector is key to quickly identifying the leak source. Being inside the tank, the detector must also be intrinsically safe for highest risk environment. This means for Zone 0 or Class I, Division 1 in the older US system.
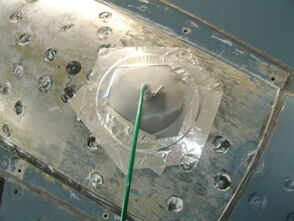
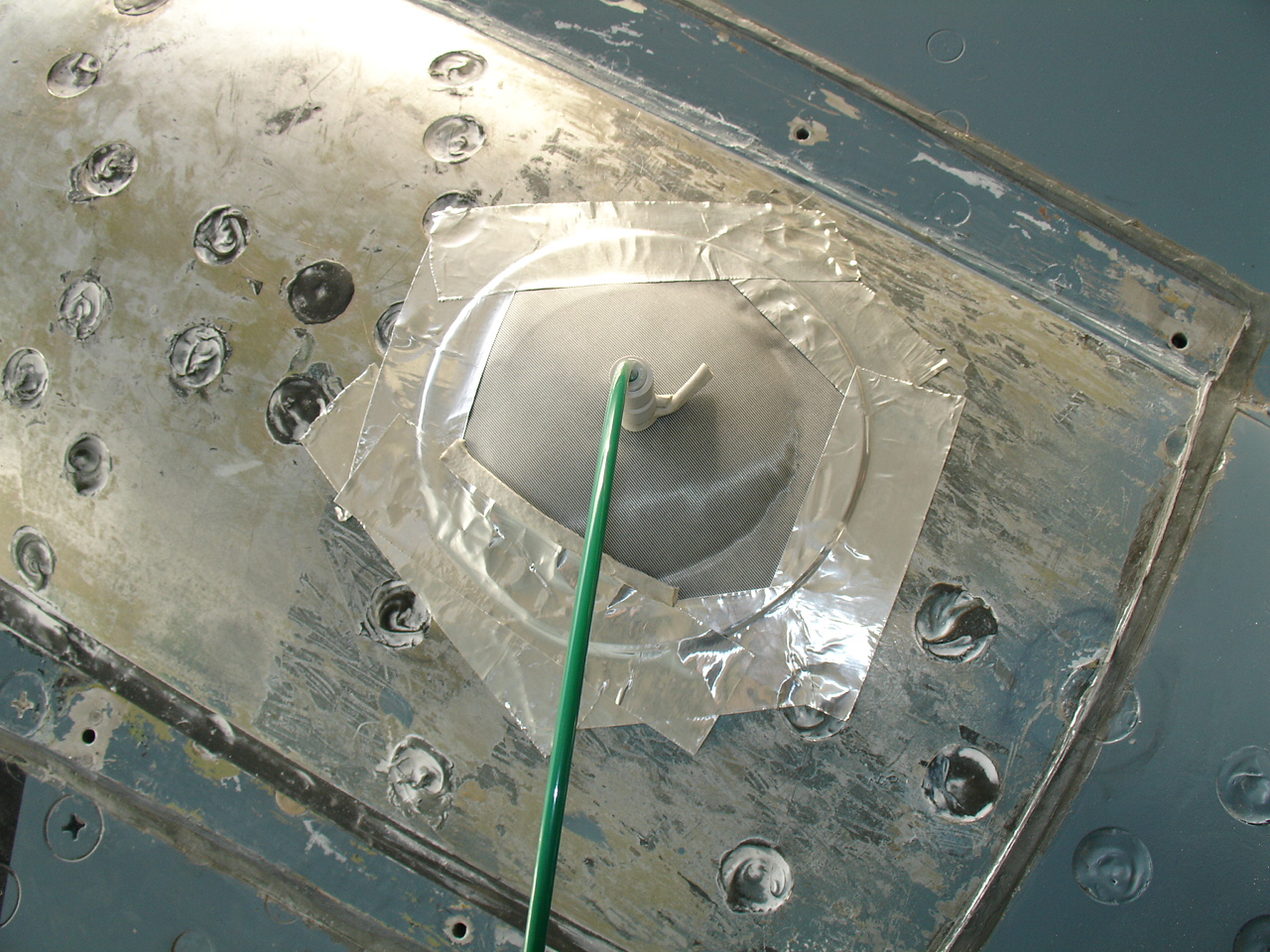
The Ex-certified Extrima hydrogen leak detector fulfills all these requirements and allows safe, fast and precise location, repair and verification of leaks in aircraft wing tanks.
The process starts by attaching a specially developed patch to the external surface of the wing where the leak has been observed. A cylinder of forming gas, a non-flammable mix of hydrogen and nitrogen, is then attached to the patch and gas is fed backwards, at low pressure, through the leak into the wing tank. The operator brings Extrima into the tank and starts pinpointing the source of the leak. This drastically reduces the area needing to be resealed. A successful repair can also easily be verified by again feeding gas to the patch and check that gas is no longer escaping inside the tank. This verification is fast and easy and eliminates the need of repeated refueling.
The technology used in Extrima is based on the proprietary hydrogen sensor developed and manufactured by INFICON. This sensor is highly sensitive and selective, which makes it ideal for applications where small leaks in the ppm range need to be found without the risk of false alarms from external combustible gases, like JET-fuel vapor in this example. The instrument’s unique search signal quickly guides the operator to the leak, even at increased background concentrations of hydrogen.
Extrima is suitable for any application where high sensitivity and selectivity for hydrogen is required. An example would be hydrogen blending in natural gas applications, where cross sensitivity to methane could be a problem with alternative technologies. The device is ideal for any scheduled or emergency leak detection work, as well as for leak tightness control after maintenance and repair of systems in hazardous areas requiring the highest level of intrinsic safety. Examples are installations such as hydrogen storage facilities, steam reformers and electrolyzers.
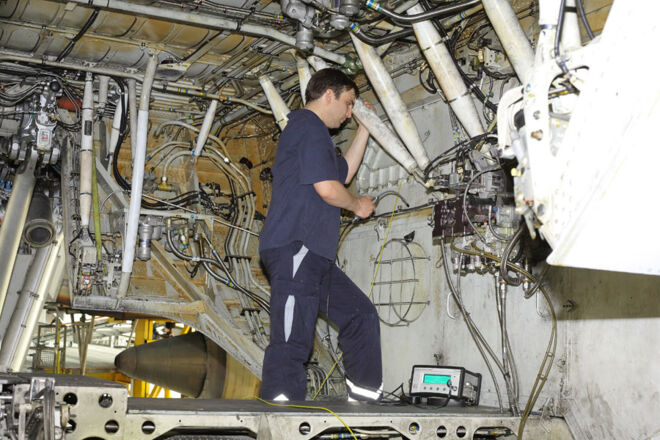
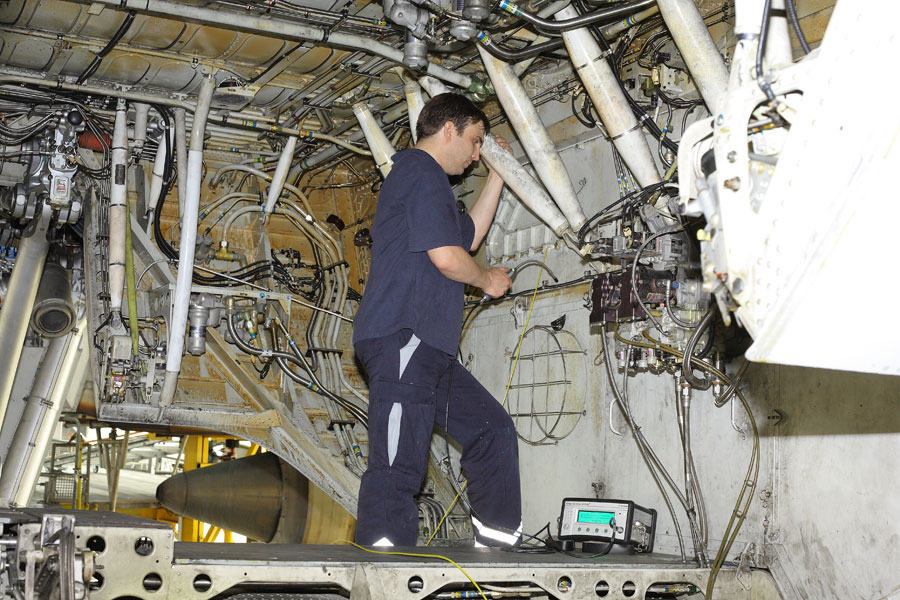
Do you want to know more?
If you want to know more about how to safely search for leaks on aircraft fuel tanks, check out the Extrima Hydrogen Leak Detector and its innovative portfolio of accessories or download our Application Note!
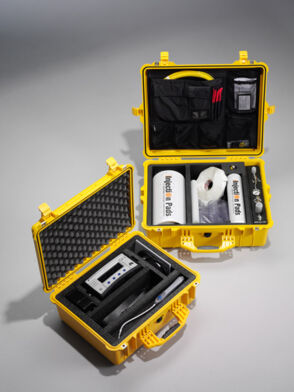
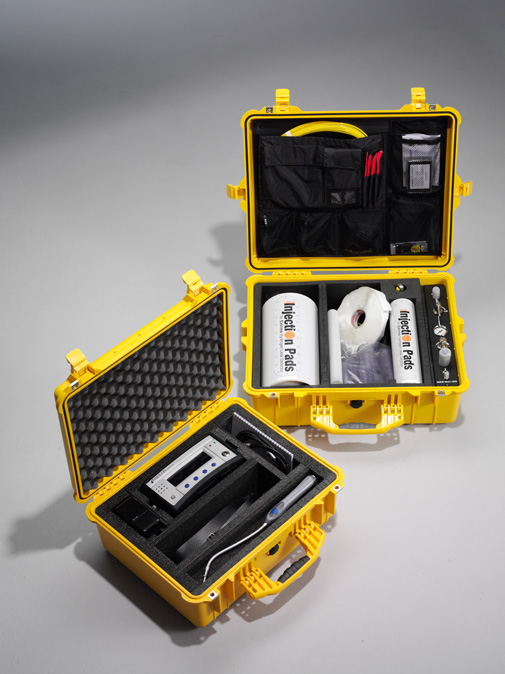