Advanced Packaging in Next-Gen Semiconductor Nodes
As devices get smaller and chips become denser, manufacturers need to increase performance while minimizing power consumption and footprint.
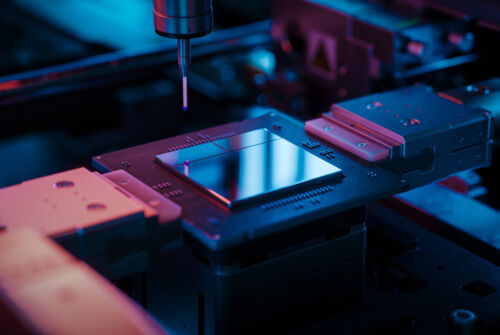
Semiconductors are the backbone of modern technology. As devices get smaller and chips become denser, manufacturers are looking for ways to continue increasing performance while minimizing power consumption and footprint. This is where advanced packaging plays a critical role.
The guiding principle for scaling chips has been Moore’s Law, which states that the number of transistors on a chip doubles approximately every two years. With the proliferation of AI technology and the need for higher processing and memory capacity, semiconductor technology must continue to progress. However, as transistor sizes continue to shrink, there are physical limits to how small individual components can get.
Advanced packaging allows companies to combine chips of different types into a single module that maximizes the performance of each individual chip. This shift from single-chip designs to multi-chip and chiplet-based systems enables higher levels of integration and better optimization of performance, as opposed to simply shrinking chips further.
Why Advanced Packaging Matters
As Moore’s law runs up against the physical constraints of two-dimensional shrink, and the limits of vertical transistor design are becoming more apparent, advanced packaging technologies are becoming the key to unlocking further performance gains. Rather than continuing to shrink single chips, advanced packaging allows for new ways to integrate multiple chips, making the most out of each component’s capabilities.
Technologies like interposers, substrates, and 3D stacking are enabling this new generation of chips. By stacking chips in 3D configurations or connecting them through 2.5D interposers, manufacturers can achieve more performance and power efficiency without needing to shrink the chip itself.
Advanced packaging not only keeps chips smaller and more efficient, but allows for more powerful, versatile systems. It becomes the key innovation for continuing to meet the demands of next-generation devices.
See INFICON at Semicon West!
Phoenix | Oct. 7-9, 2025
Booth #1391
The Role of Semi Fabs in Advanced Packaging
Semiconductor fabrication facilities, or semi fabs, are integral to the semiconductor manufacturing ecosystem, especially as advanced packaging technologies continue to evolve. These facilities are crucial for integrating various manufacturing steps, ensuring precision in the assembly of multi-chip and chiplet-based systems. As hubs of innovation, semi fabs drive the development of new technologies and methodologies, such as 3D stacking and interposer integration, which are vital for achieving enhanced performance and efficiency in semiconductor devices.
Semi fabs are also tasked with maintaining high standards of quality. They employ advanced process control solutions to monitor and optimize critical processes, ensuring that semiconductor devices meet rigorous benchmarks. The complexity of advanced packaging requires semi fabs to operate with maximum efficiency, which involves optimizing manufacturing processes and coordinating supply chain logistics. Solutions designed to streamline operations and reduce bottlenecks are essential for enhancing overall productivity, making semi fabs indispensable in the advancement of semiconductor packaging.
Solving the Supply Chain Puzzle
As advanced node packaging becomes more complex, so does the challenge of coordinating its manufacturing process. Modern multi-chip and chiplet-based designs require multiple components to be integrated into a single package. This shift demands a tightly coordinated supply chain, where different materials and parts, often from separate facilities, must arrive at the right place at the right time.
For some manufacturers, completing a single advanced package means sourcing materials from three different factories simultaneously. Any delay in one part of the supply chain can stall production, leading to inefficiencies like excess inventory buildup in one location while another facility sits idle. To mitigate these challenges, companies must treat the supply chain like an extension of the fab itself, carefully scheduling the output of one facility to align with the input needs of another. Fab scheduling solutions like Factory Scheduler from INFICON are inherently designed to solve these kinds of problems to optimize both front-end manufacturing along with advanced packaging logistical challenges.
Beyond logistics, backend equipment reconfiguration adds another layer of complexity. Swapping out components to accommodate different packaging designs can take 12-24 hours, making real-time scheduling and optimization essential. Advanced process control solutions like FabGuard® FDC from INFICON play a role here, particularly in vacuum and chemical processes critical to packaging. However, in the backend, where many tools are self-correcting, manufacturers must carefully weigh the ROI of investing in additional sensors and monitoring systems.
Want to Learn More?
Contact INFICON to learn more about our solutions by filling out this form.
Integrating Sensor Technologies
Many processes employed in advanced packaging manufacturing steps are very similar to front-end silicon manufacturing which require both patterned etch and metal deposition steps to create the desired system design, only in this case these processes are deployed at the substrate level. INFICON’s gas sensor portfolio of RGAs, SP-OES, vacuum gauges and leak detectors are all well-proven to support and enhance that kind of manufacturing environment by improving yield and reducing tool down time.
Sensors play a vital role in monitoring and optimizing the complex processes involved in multi-chip and chiplet-based designs, including:
- Real-time Process Monitoring: Residual Gas Analyzers (RGAs), Self Plasma Optical Emission Spectroscopy (SP-OES), and RF sensors are essential for monitoring the chemical processes involved in etching and deposition. These sensors provide detailed insights into the composition and behavior of gases, allowing for contamination control and precise optimization of manufacturing steps.
- Vacuum Management: Vacuum components are crucial for maintaining the necessary conditions for advanced packaging processes. They ensure that vacuum levels are consistently monitored and adjusted, preventing process variation and ensuring the integrity of the packaging.
- Leak Detection: INFICON's leak detectors are designed to identify and mitigate potential leaks in packaging systems. This capability is vital for maintaining the quality and reliability of semiconductor devices, as even minor leaks can lead to significant performance degradation.
The integration of sensor technologies not only enhances the precision of packaging processes but also contributes to overall manufacturing efficiency. By reducing tool downtime and improving yield, sensors play a key role in optimizing production workflows and ensuring that advanced packaging meets the demands of next-generation semiconductor nodes.
As semiconductor packaging continues to evolve, companies must optimize scheduling, process control, and supply chain coordination while protecting their product to maximize overall efficiency. The next generation of performance depends not only on innovative packaging designs but also on ensuring that every component arrives, integrates, and functions seamlessly within an increasingly complex manufacturing ecosystem.
Meeting Demands of the Future
To maintain the pace and meet the demands of the latest technological innovations the role of advanced packaging in next-generation technology nodes becomes increasingly important. The shift to multi-chip and chiplet-based designs represents a significant departure from traditional approaches, enabling continued innovation even as transistor scaling slows down. By leveraging advanced technologies, manufacturers can create more powerful, efficient, and flexible systems that meet the demands of the future.
INFICON sensors are tailored to support a wide range of applications, ensuring product safety, increased yield and maximum productivity.
INFICON core technologies include mass spectrometry, quartz crystal microbalance, RF DC detectors, optical sensors, vacuum gauges and leak detectors.
INFICON Intelligent Manufacturing Systems deliver cutting-edge solutions to optimize semiconductor production, enhance quality control, and maximize operational efficiency.