Factory Scheduler
The most Powerful, Efficient, and Smart Scheduling System for Industry 4.0 Factories
Tune the output of your factory with Scheduling to optimize: line linearity, turns, cycle time, equipment throughput and utilization, labor productivity and on time delivery.
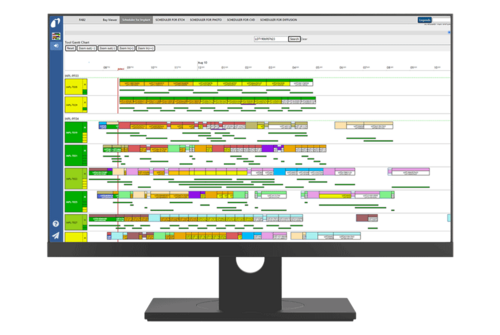
Smart Scheduling for Smart Factories
The INFICON Factory Scheduler is built on over 20 years of manufacturing and operations experience building optimized and robust WIP schedulers for all areas of the factory.
The Factory Scheduler utilizes Advanced Heuristics, Linear Programming, Optimization, and Intelligent Search Algorithms to generate a real-time optimized schedule that can be easily tuned to meet your manufacturing needs.
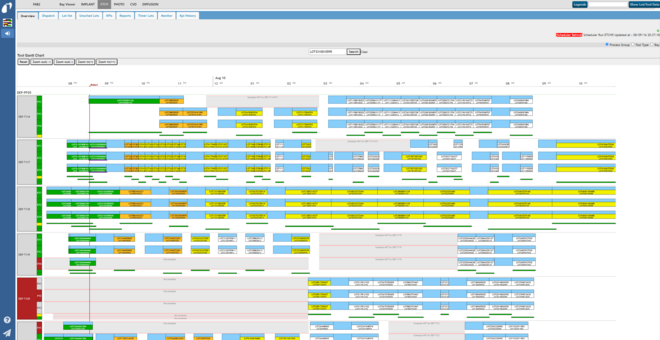
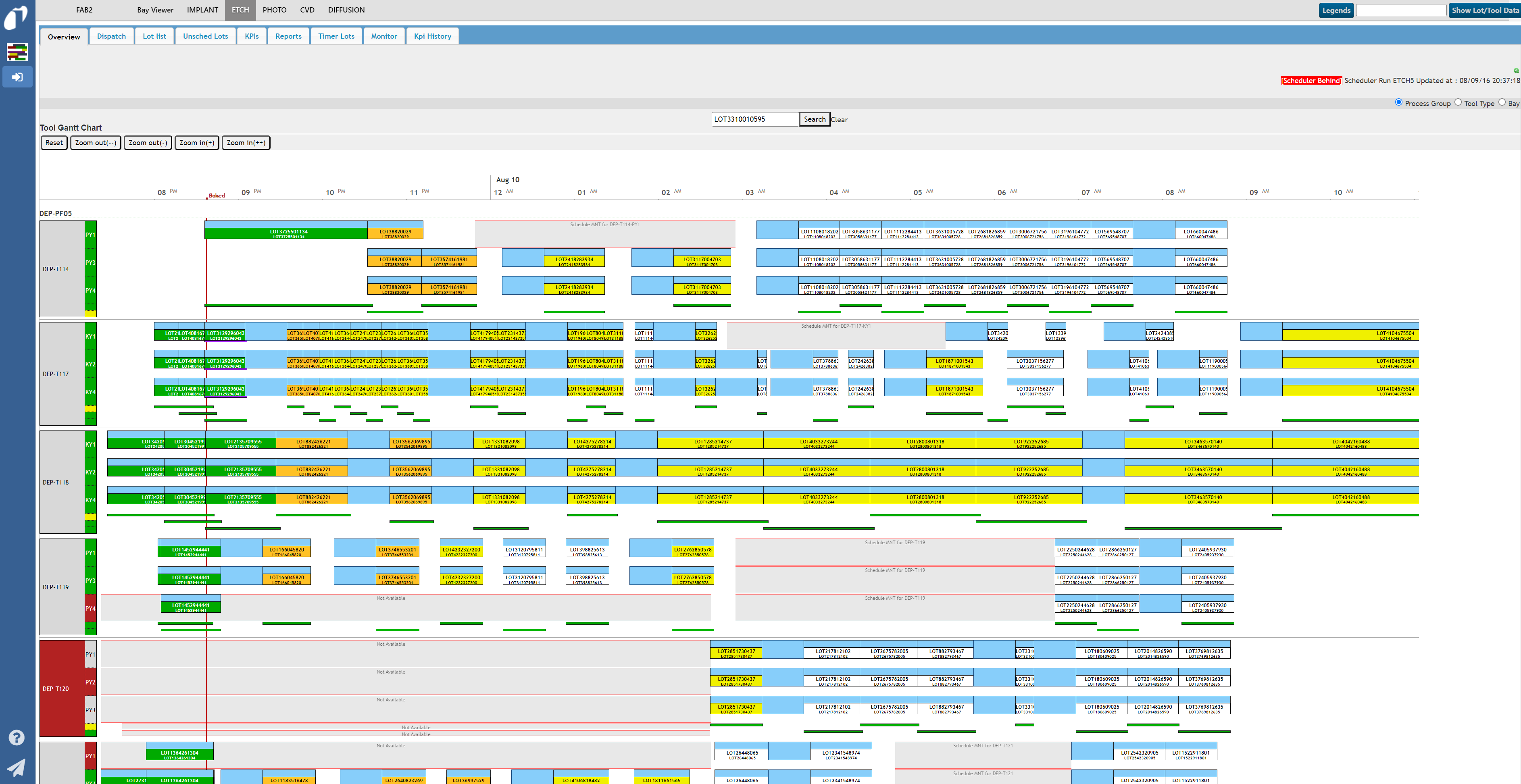
INFICON schedules more than 2,000,000 substrates per day in semiconductor factories AROUND the world.
Scheduling is NOT Dispatch
Dispatch rules are not sufficient to manage the WIP for a modern factory. While their execution is simple and better than purely manual decisions, they are difficult to maintain as they cannot automatically adjsut to changing factory conditions. When compared to scheduling dispatch rules have considerable drawbacks:
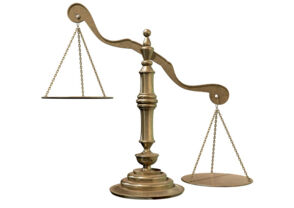
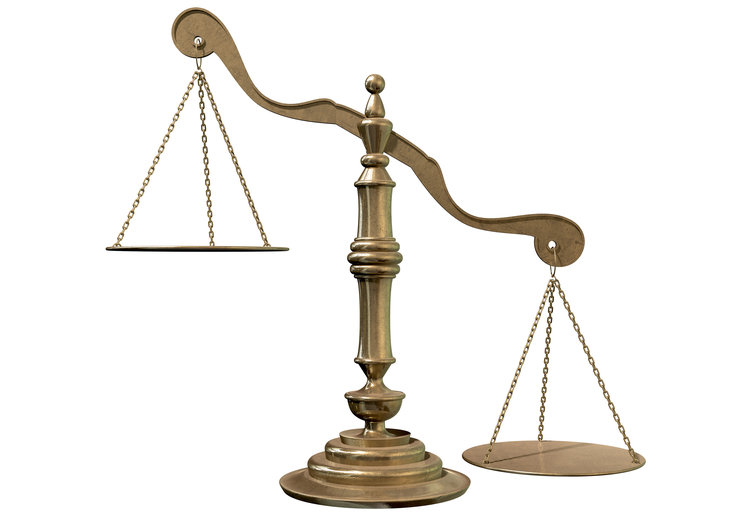
- Dispatch rules do not forecast results. If I run this lot now, will it be able to finish its queue timer 6 steps from now?
- Each local step must have its own logic, which can be out of sync or in conflict with upstream or downstream rules
- Rules are difficult to quickly adjust to changing needs
- Global business goals are difficult to formulate in the language of local dispatch rules
- Rules typically only consider lots at station, and not those arriving soon or downstream
- The results of changing dispatch rules are very hard or impossible to test in advance
- Look ahead. A scheduler will stop a lot if a queue timer will expire
- See the whole line. Factors like line balance, down toolsets, WIP holding are comprehended
- Incorporate setup changes, reticle switches, movement penalties, etc.
- Comprehend upcoming maintenance events
- Provide true balancing of local and global priorities
- Facilitate centralized business logic, and give Fab managers the controls
- Allow changes to be tested hypothetically, without affecting production
- Open up smart manufacturing integration opportunities - A system that "knows" where WIP will be creates opportunities for managing pumps, abatement units, etc.
Facility and Area Scheduling
For small factories, a single Area Scheduler can be powerful enough to schedule all the WIP in the facility. For most high volume factories, INFICON will install a group of several Area Schedulers working together. Area Schedulers feature modular logic to accommodate the specific complexities of the area being scheduled - Lithography, Diffusion, Implant, Test, Dicing, etc. They also communicate with each other to optimize global priorities.
Understand Decisions
The Scheduler Gantt Chart shows when and where lots will run and how the decision was made. The intuitive user interface will display the reasons that led to the placement of the lot on the schedule, broken down by the importance of each priority. This enables engineers to see the imact of the current schedule on downstrean steps.
Not Just a Replacement, But Something New
INFICON Schedulers open up entirely new factory capabilities. Consider an example of a tool with an expensive abatement system that Fab managers have targeted for cost reduction. The system has a warm down mode which reduces the cost of operation by 95%, but that is only used during tool PMs. The Factory Scheduler can schedule around the tool when possible and with the right system integration can automatically trigger the abatement warm down when the tool is not needed. Like turning off the lights when leaving a room. Bottom line: the opportunities created by the FPS Factory Scheduler showcases the next generation of AI-Enabled factory of the future.
Smart Back-End Scheduling
WIP management and scheduling for semiconductor Back-End operations is becoming increasingly important. Line linearity, increased throughput and utilization, and accurately meeting ship targets is as important in the Back-End as it is in the Front-End. The INFICON Back-End Factory Scheduler uses advanced algorithms leveraging practical constraints and real time information to make a schedule based on current conditions and priorities.The schedule updates continuously and generates the full end-to-end schedule for the entire facility. This guarantees continuously relevant results amidst the dynamic conditions of the back-end facility. Delivery information from previous operations and front-end facilities are used as inputs for back-end sites enabling better planning and coordinated from die manufacturing to assembly and test.