FabRecover®
The Industry’s first dynamic decision support system
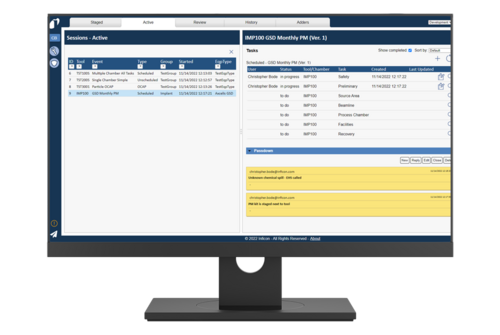
FabRecover provides dynamic, real time maintenance decision support, as well as visibility to maintenance history, to maximize tool availability and minimize support costs.
FabRecover drives the use of Best Known Methods (BKM), continuous improvement, and enhanced visibility into maintenance activities.
First Time Right Maintenance
FabRecover is a knowledge-based, decision support software platform that is specifically designed to help factories return tools to production quickly and correctly.
Responsive and heuristic guidance reduces variability through real-time support based on subject matter expertise gathered from across the organization.
Complete activity tracking gives visibility into maintenance work, thereby supporting cycles of learning and continuous improvement through data-driven analysis and review
Advantages
- Step-by-Step guidance
- Comprehensive root-cause analysis
- Maintenance and activity tracking
- Flexible and dynamic workflow
step-by-step, dynamic guidance and needed support for BKM work
root cause analysis and identification based on historical and heuristic data trends
modeled linkage between control system events, troubleshooting, and remediation
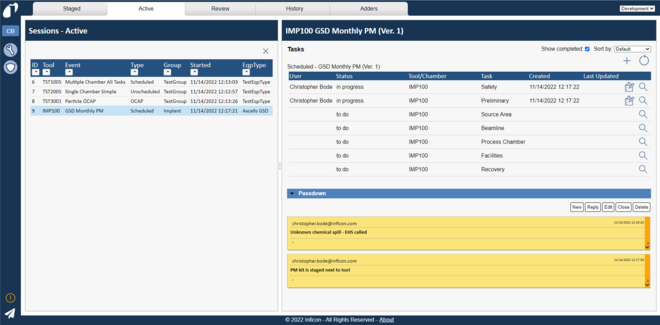
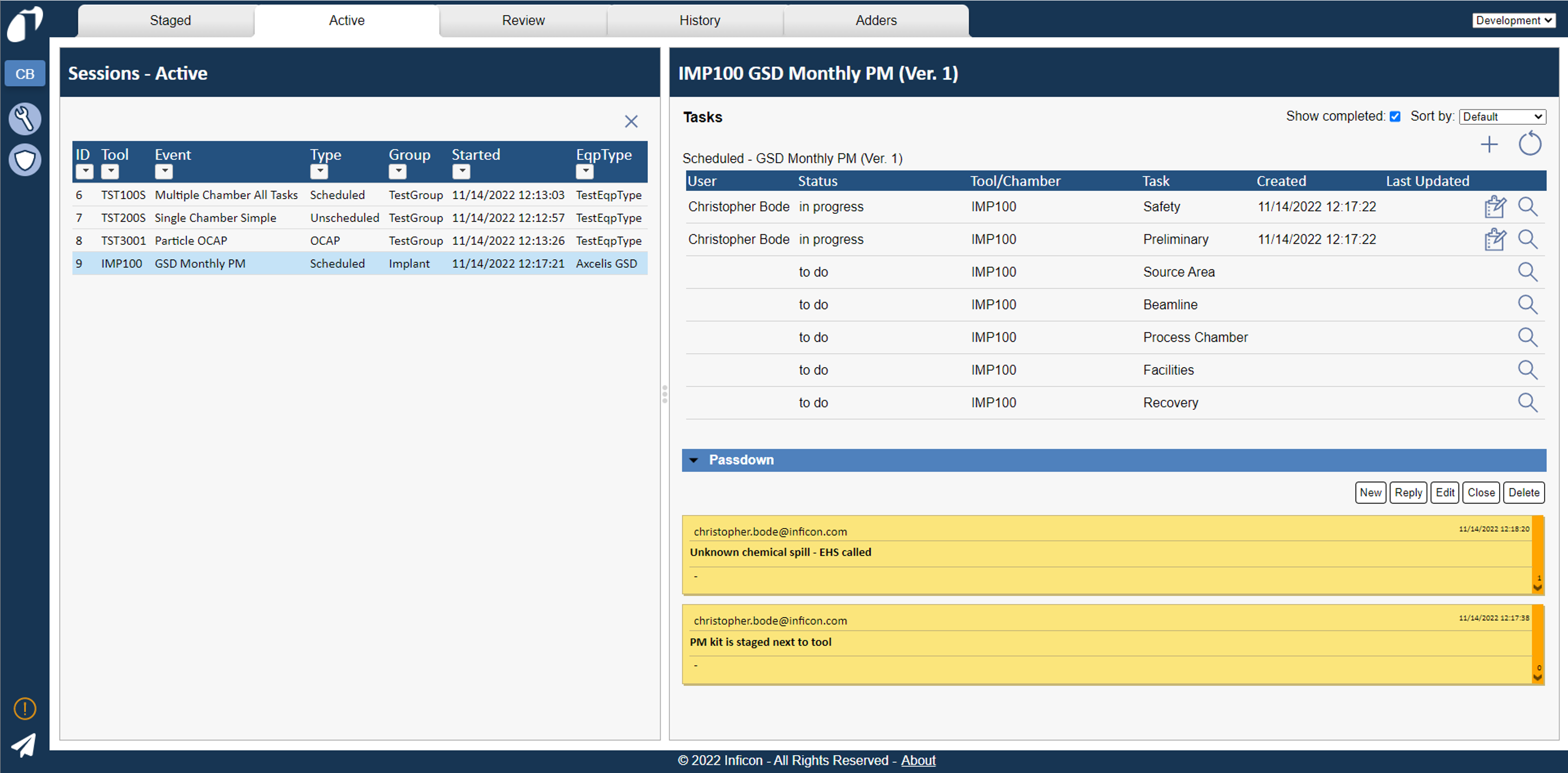
Scheduled Maintenance
Preventative Maintenance support begins with improved First Time Right (FTR) success by reducing maintenance execution variability. FabRecover provides the tools to detail necessary work including reference materials, input validation and business rule definition.
FabRecover supports users of varying levels of experience in following Best Known Methods for all activities which reduces training costs and increases efficiency and efficacy.
Flexible and dynamic workflow definition responds to different situations as they happen, whether addressing additional challenges or taking advantage of unexpected opportunities within each maintenance session, FabRecover guides engineers through the BKM process.
Unscheduled Maintenance
Decision networks help with root cause investigations using historical trends and corresponding corrective actions to provide insight into current investigations.
Expert knowledge is modeled to produce optimal investigation paths to reach known conclusions. Additionally, heuristic learning paired with dynamic guided support actively identifies the more or most likely root causes for precision and efficiency in root cause identification.
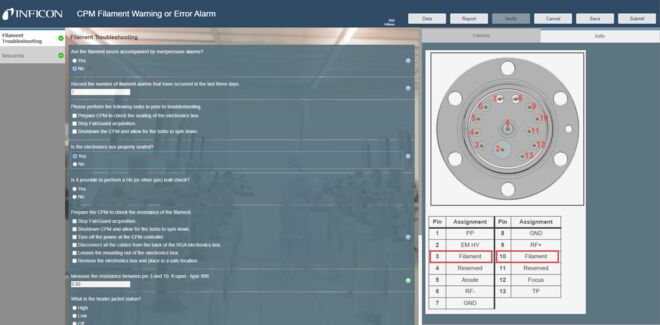
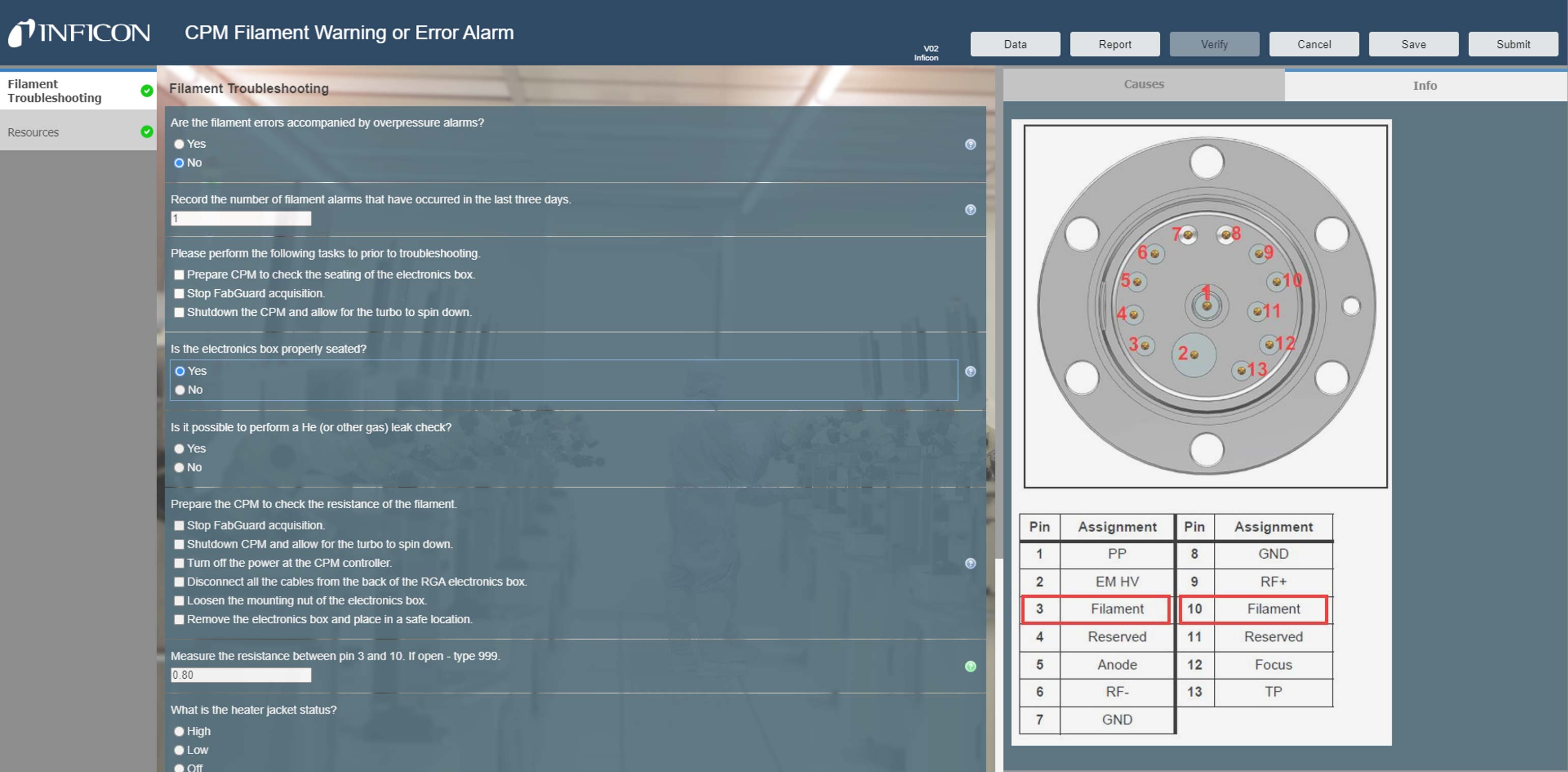
Expert driven solutions
Reduced development and training costs are possible through the Visual Designer and its user-friendly visual modeling platform. Subject Matter Experts (SME) are empowered to model smart business logic themselves — without coding or any prerequisite experience.
Out-of-the-box use case templates lower barriers to entry in creating maintenance workflows, that can be extended to address common needs and enforce prescribed standards of each factory.
Extensibility of the platform ensures that the platform can grow to meet specific customer challenges, and that incremental development can be leverages immediately across all use cases.
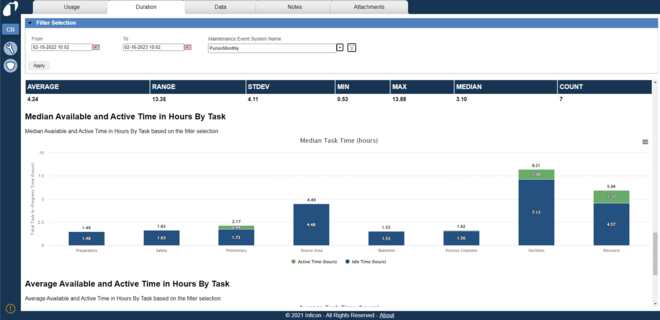
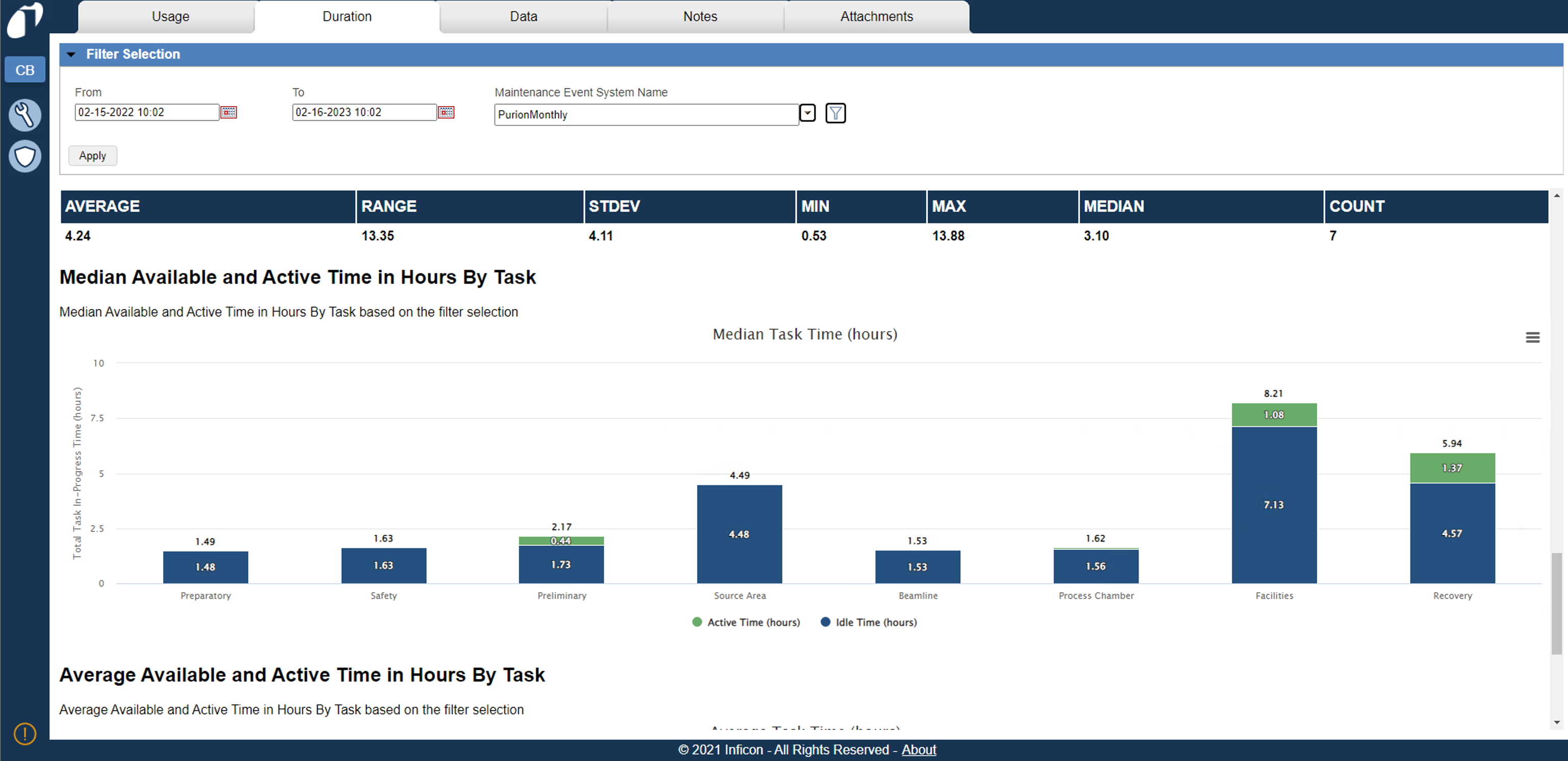
Interested in More?
Contact us to help you maximize your factory operations.