How Digital Twins Are Shaping the Future of Semiconductor Manufacturing
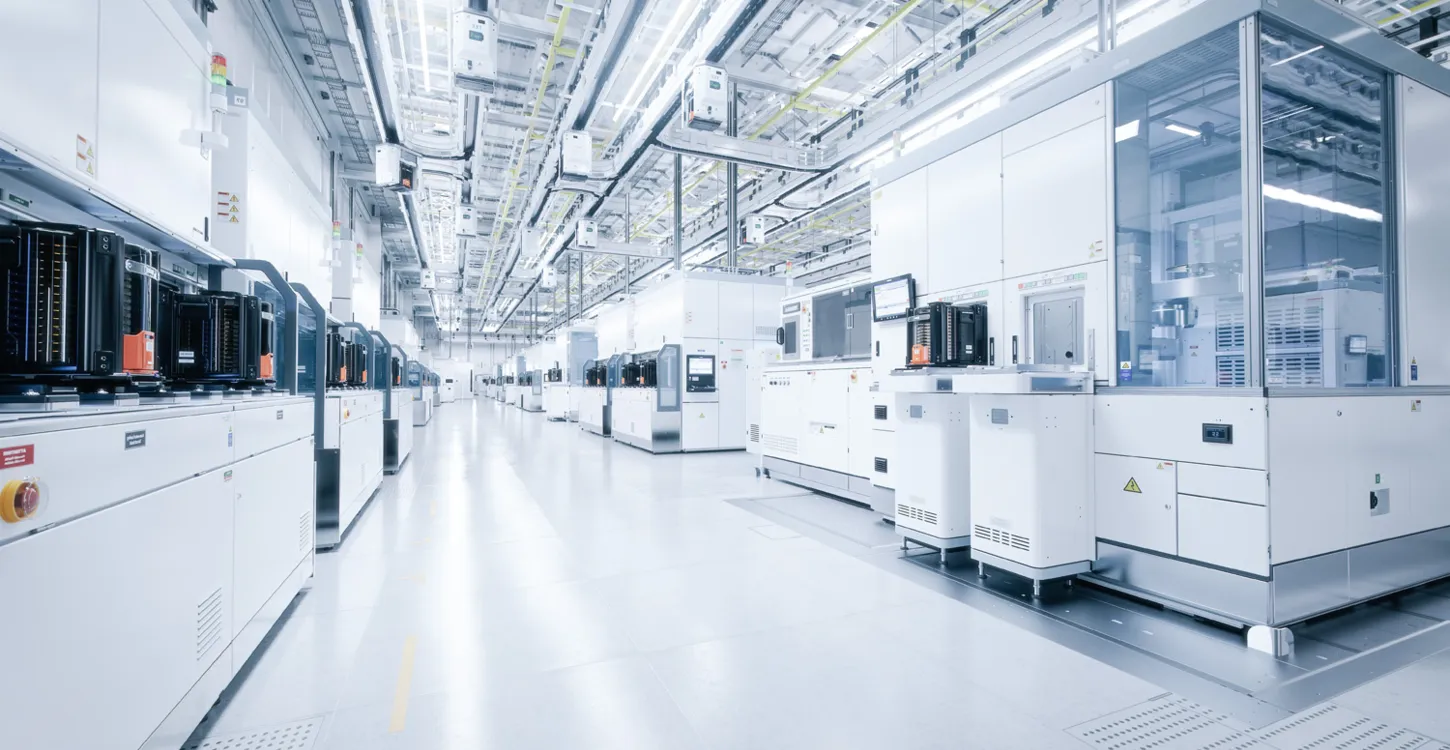
In today’s ever-evolving semiconductor manufacturing industry, ensuring operational efficiency and precision is critical. With factories handling thousands of process steps across hundreds of product types, semiconductor production is one of the most complex forms of manufacturing. Digital twin technology offers a real-time, predictive model of your factory’s processes, enabling smarter decision-making and significant improvements in operational efficiency. Read on to learn how digital twin technology from INFICON can help factories reach new levels of efficiency.
The Power of Digital Twins in Semiconductor Manufacturing
Digital twins serve as virtual replicas of physical entities, such as factory processes, equipment, or entire production facilities. They are designed to evaluate real-time data from machines, sensors, and systems, allowing factories to run predictive analyses on various operational scenarios. In semiconductor manufacturing, where we see extensive WIP (work in process) and the need to track tens of thousands of wafers, digital twins simplify complexity and deliver more precise, real-time monitoring and optimization.
Our partners who use INFICON digital twin solutions have experienced transformative improvements in production key performance indicators including: On-Time-Delivery (OTD), bottleneck tool OEE, and factory output. For instance, our Factory Scheduling and Operations Digital Twin solutions make autonomous decisions impacting tool and lot assignments ensuring smooth workflow and minimizing downtime.
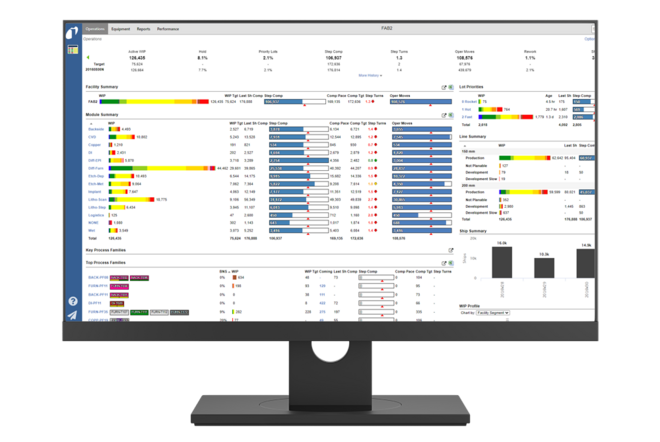
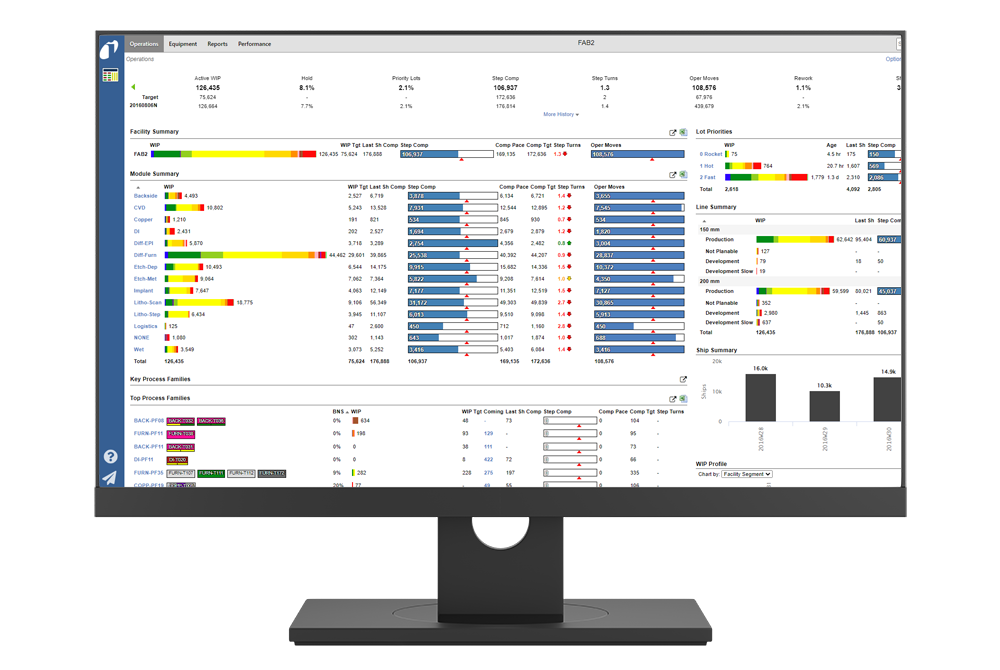
Enhanced Factory Scheduling and Resource Optimization
WIP scheduling, deciding where to place each lot in a factory to optimize performance, benefits greatly from a factory Digital Twin. Our customers have experienced remarkable results from our scheduling software, which can help increase on-time delivery by up to 20%, reduce cycle times by 25%, and boost factory outputs by 14%. By integrating digital twins with automated material handling systems, customers have achieved further improvements, such as increasing overhead transfer efficiency by 33% in large production environments.
Our digital twin technology isn’t just about making factories more productive. It’s about refining processes to conserve resources and minimize environmental impact, providing a foundation for sustainable manufacturing.
Integrating Digital Twins Across Manufacturing Levels
Manufacturers can implement digital twins at multiple levels—from process tools to entire factory operations. Our Tool based Digital Twin, for example, enhances individual equipment performance with precise anomaly detection and process monitoring using machine learning. On a broader scale, our Operational Digital Twin integrates factory-wide WIP movement, durable and consumable usage optimization and metrology sampling to ensure maximum efficiency across the factory. The culmination of these factory systems enables centralized autonomous control.
Imagine a future where factory control rooms unify digital twins across the entire production chain. This advanced system not only boosts factory efficiency but also leverages AI-driven insights to keep pace with production demands.
Our collaboration with industry thought leaders aims to build a roadmap for this vision, enabling the semiconductor industry to implement autonomous control rooms that redefine operational standards.
Explore how our digital twin technology can transform your production efficiency. Learn more about our comprehensive smart manufacturing solutions online here: Smart Manufacturing.
At INFICON TechDay2024, John Behnke presenting on how we are shaping the future of Smart manufacturing. Click the box below to watch!