Leak testing of Li-ion battery cells in mass production
Improvements in cycle times and throughput for high-speed testing
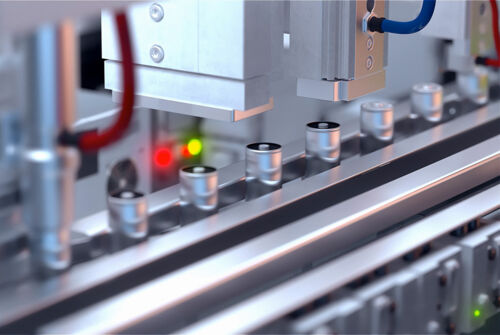
For the operational reliability and durability of modern traction batteries, the leak tightness of their smallest components is crucial: the lithium-ion cells. The housings of all cells must be tested for leaks during production. Flammable electrolyte must not be allowed to escape, nor must atmospheric moisture be allowed to penetrate the cell, as water can react with the electrolyte to form corrosive hydrofluoric acid. In addition, leaky cells reduce the capacity and service life of traction batteries. During production, careful leak testing is essential for quality assurance.
INFICON’s ELT3000 PLUS battery leak detector directly detects electrolyte solvent leaking from a cell into a vacuum test chamber. This makes it far more reliable than previous methods, such as pressure testing or helium bombing. INFICON has designed the ELT3000 PLUS to be just as suitable for use at manual workstations in development departments as for quality assurance in automated production lines. ELT3000 PLUS meets the need for speed that is an important factor in series production.
High throughput for mass production with powerful external vacuum pumps
Measures to reduce cycle times include:
- the smallest possible dead volume in the vacuum chamber
- the use of a particularly powerful external vacuum pump together with additional valves for evacuation and final ventilation
- cleaning of the cells from electrolyte residues even before the actual test cycle
With a test chamber of 1 l free volume (volume of the test chamber minus the volume of the test specimen), the typical preset measuring cycle of the ELT3000 PLUS consists of 5 s cleaning of the cells from electrolyte residues on their surface, 32 s evacuation of the vacuum chamber to approx. 5 mbar abs., 6 s tightness measurement and 4 s ventilation of the vacuum chamber - i.e. 47 s in total. Added to this are the process times for loading and unloading the test specimens from the chamber. If, on the other hand, an external pump with a capacity of 100 l per minute is used for the same test chamber, for example, the evacuation time is reduced from 32 s to 12 s. In the case of pre-cleaned test specimens (e.g. by laser cleaning), an additional 5 s of cleaning time can be omitted, resulting in a sizable overall reduction of the measuring cycle from 47 s to 22 s.
Testing systems with multiple vacuum chambers
A second, very effective option for increasing the throughput of leak testing on filled cells with a single ELT3000 PLUS is the parallel use of several test chambers. While a measurement is currently taking place in one chamber, a second test chamber can already be charged and a third (and possibly fourth, depending on the size of the chambers and the evacuation time) can already be pre-evacuated. The ELT3000 PLUS is almost exclusively in measuring mode, so that the time required for evacuation can be saved and the throughput significantly increased.
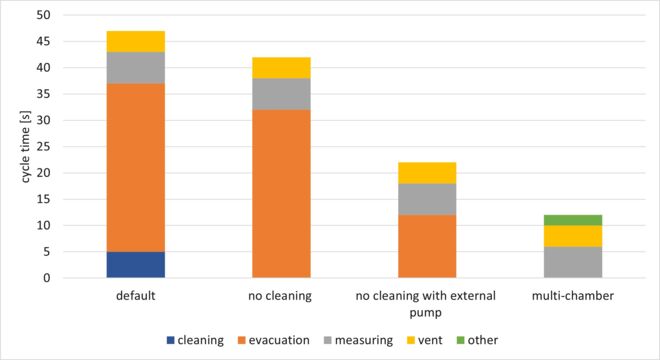
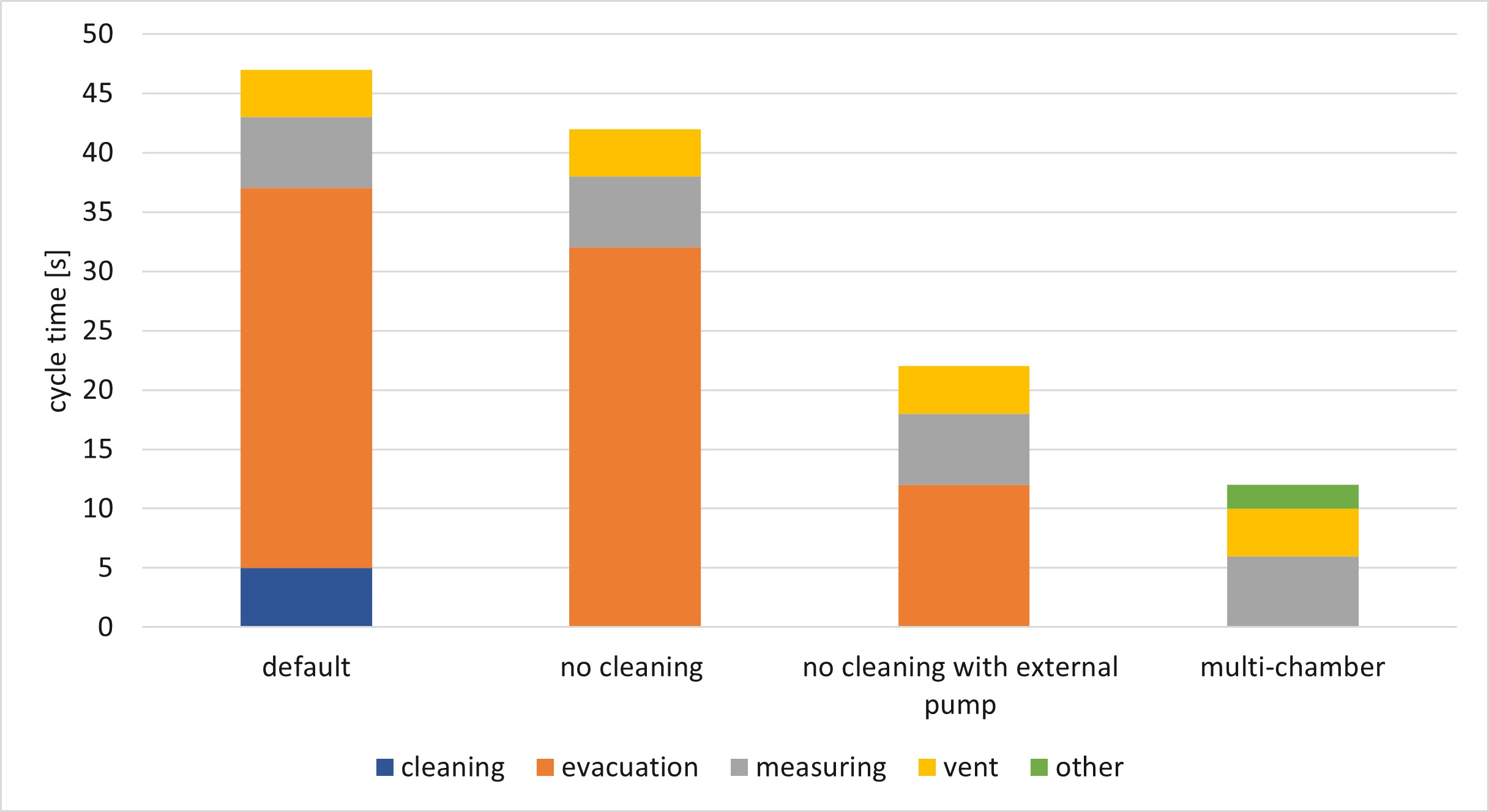
Batch testing for very high throughput testing
However, a closer look shows that for leak testing, throughput is often an even more important variable than pure cycle time. Throughput during testing can be decisively increased by a batch testing approach.
Let's assume that batches of 16 round cells of type 21700 each are to be tested in the described system with an external vacuum pump and with DMC as the essential solvent. With a cycle time of 22 s, this results in a test time of 1.4 s for each cell. If the batch is enlarged to 64 round cells, one cell is tested every 0.3 s. If a batch test reveals a leak, the leaky cell must be identified at a manual test station. To do this, the batch size is halved several times so that the batch that does not contain the leaking cell can always be ignored for further tests. Thus, in an iterative way, one approaches a batch of size 1: i.e., the one that contains the defective cell. With 16 cells in the original batch, this principle results in four further test stages; with 64 cells, six stages are necessary for separation.
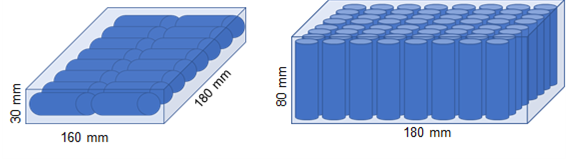
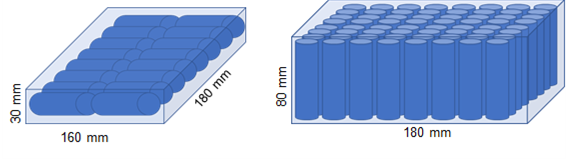
Cycle time [s] | Batch of 16 cells | Batch of 64 cells | |
---|---|---|---|
Standalone | 47 | 2.9 s / cell 20 cells / min | 0.7 s / cell 85 cells / min |
With external pump | 22 | 1.4 s / cell 42 cells / min | 0.3 s / cell 200 cells / min |
Determine the ideal batch size
Against this background, it is a question of optimization which batch size makes sense for a specific application. The ideal batch for quality assurance in line production can only ever be determined individually. For example, let's assume a typical cell defect rate of 0.5 percent of production. With a batch size of 16, around 20,900 cells can be inspected in one shift with a cycle time of 22 seconds. However, this includes an average of 105 batches of 16 that contain leaking cells. Assuming 30 s for each manual inspection after one of the four batch halving steps, this results in a time requirement of around 3.5 h for the manual identification of all leaky cells per shift. If, on the other hand, we work with a batch size of 64 cells in this example, 83,800 cells can be inspected per shift, but there will also be an average of 420 batches with defective cells. At the same time, the number of halving steps required increases to six for batches of 64. This results in a time requirement of around 20.9 h for manual identification of the leaky cells per shift.
The ELT3000 PLUS in the production line
Basically, for all types of lithium-ion cells, there are two process steps after which leak tests can usefully be carried out with the ELT3000 PLUS: after filling and sealing, and after forming the cells. The test after sealing makes it possible to avoid the formation effort for leaky cells and at the same time, exclude any risk due to the formation of leaky cells. A second test, after forming, can identify leaks caused by handling - which is particularly possible with pouch cells - and at the same time ensures that only leak-proof cells are processed further.
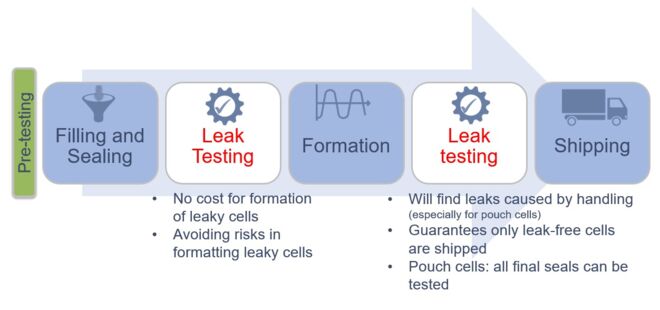
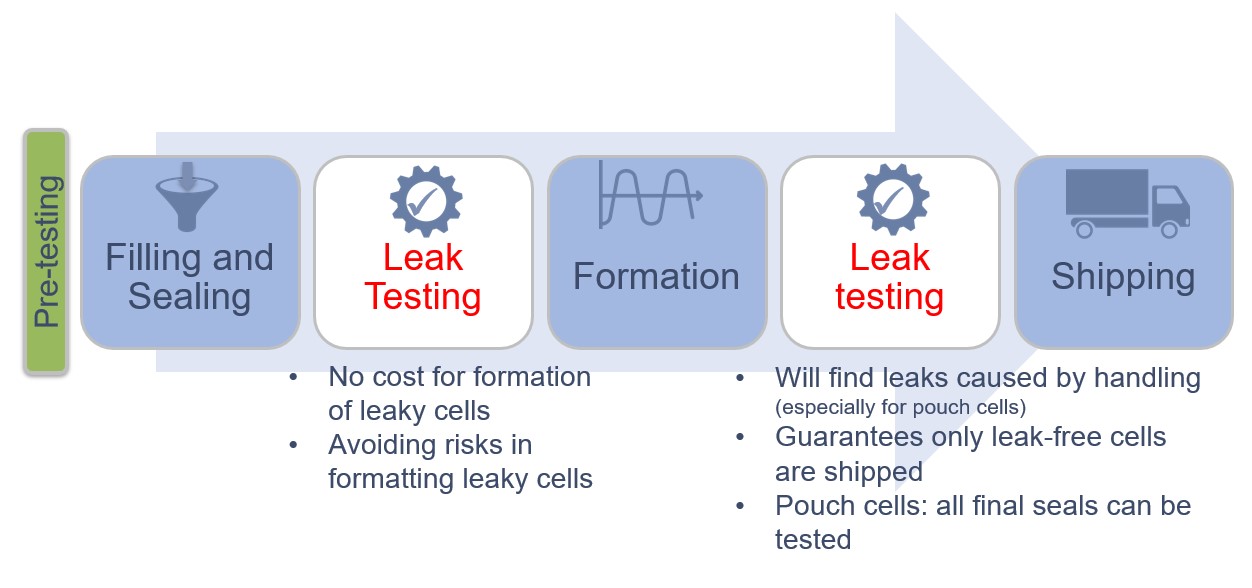
Direct detection of leaking electrolyte solvent |
---|
INFICON has developed and patented an innovative method that, for the first time, is able to detect leaks on ready-filled cells very reliably, whether on those with rigid housings such as prismatic, round or button cells or on soft pouch cells. The special feature of the new method is that it directly detects electrolyte solvent leaking from a cell into a vacuum test chamber. This makes it far more reliable than previous methods such as pressure testing or helium bombing. INFICON's patented ELT3000 PLUS leak tester can test lithium-ion cells for leaks of a few micrometers in diameter, which corresponds to a helium-equivalent leak rate of 1∙10-6 mbar∙l/s. A flexibly conforming foil chamber serves as a vacuum test chamber for soft pouch cells and prevents damage to the sensitive housings. This makes it possible for the first time to test pouch cells for leaks even after they have been filled. |
To learn more about how the ELT3000 PLUS can be used for high-speed testing, have a look at our on-demand webinar or call your nearest sales representative