Mobilität & Automotive
Zuverlässige Lecktests in einer sich entwickelnden Industrie
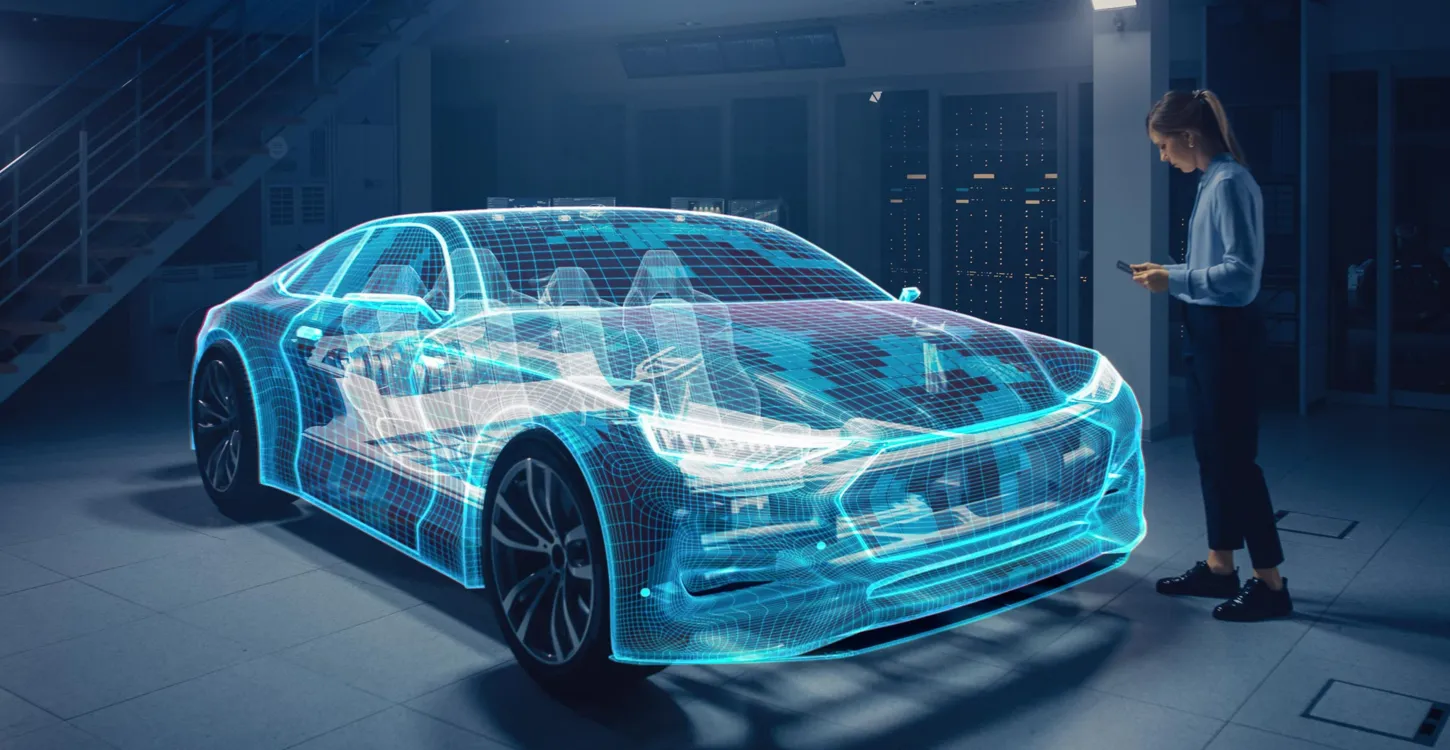
Der Wandel in der Automobilindustrie macht Dichtheitsprüfung noch bedeutsamer
Kraftstofftanks, Einspritzsysteme, Airbag-Gasgeneratoren – schon bisher hatten Sie es bei der Produktion automobiler Komponenten mit vielfältigen Dichtheitsprüfaufgaben zu tun. Neue, umweltfreundliche Antriebstechnologien bringen ähnliche und oft sogar noch schärfere Dichtheitsanforderungen mit sich. Ob es um einzelne Batteriezellen oder um Batteriepacks geht, um die Bipolarplatten von Wasserstoff-Brennstoffzellen oder um die ADAS-Sensoren autonomer Fahrzeuge. INFICON bietet Ihnen für alle industriellen Prüfaufgaben die optimalen Dichtheitsprüfgeräte.
Bei der Fertigung von immer mehr automobilen Komponenten ist die Dichtheitsprüfung heute ein unentbehrliches Element der Qualitätssicherung. Unsere Experten beraten Sie gern, wie die ideale Lösung für Ihren konkreten Anwendungsfall aussieht. Eine, die maximale Zuverlässigkeit, hohen Durchsatz und moderate Kosten miteinander verbindet.
Online-Seminar zur Dichtheitsprüfung
Im Antriebsstrang von Fahrzeugen mit Verbrennungsmotor gibt es unterschiedlichste Komponenten, die Sie während des Fertigungsprozesses auf ihre Dichtheit prüfen müssen. Ob es um die Vorprüfung noch leerer Getriebegehäuse geht oder um die Öldichtheit der Wandlerautomatik. Ein Zweimassenschwungrad müssen Sie ebenso auf seine Dichtheit testen wie etwa einen Ladeluftkühler.
Bei all diesen Prüfaufgaben stoßen traditionelle Verfahren wie etwa Druckabfallprüfungen an ihre Grenzen. Ladeluftkühler sind schon prinzipbedingt für Temperaturschwankungen empfindlich. Temperaturänderungen können das Resultat einer Druckprüfung aber völlig unbrauchbar machen. Viel zuverlässiger sind für Sie die prüfgasbasierten Methoden von INFICON – wie der LDS3000 im Zusammenspiel mit einer Vakuumkammer oder der LDS3000 AQ für die kostengünstige Akkumulationskammer.
Durch strengere Normen zur Vermeidung von Kohlenwasserstoffemissionen haben sich die Anforderungen an die Dichtheit von Kraftstofftanks und Treibstoffsystemen in den vergangenen Jahren weltweit stetig erhöht. Tanks und Leitungen werden darum oft gegen Leckraten von 10-4 bis 10-6 mbar∙l/s getestet. Wasserbad- und Druckverfahren sind hier überfordert. Nur prüfgasbasierte Methoden helfen Ihnen weiter.
Aber auch wenn Sie Einspritzventile oder Benzinpumpen fertigen, sind genaue Dichtheitstests unverzichtbar. Bei Common-Rail-Einspritzanlagen sind die Anforderungen wegen der hohen Betriebsdrücke oft noch strenger. Für diese Komponentenkategorien liegen die Leckraten, gegen die Sie prüfen müssen, im Bereich zwischen 10-4 bis 10-6 mbar∙l/s. Hier haben sich Geräte wie der INFICON LDS3000 und LDS3000 AQ im industriellen Einsatz immer wieder bewährt.
Nach der Endmontage kann es erforderlich sein, vorgeprüfte Komponenten noch einmal auf die Dichtheit ihrer Verbindungsstellen zu testen. Dafür bietet Ihnen INFICON diverse Schnüffellecksuchgeräte. Der Ablauf: Sie befüllen Ihre Komponente unter Druck mit dem Prüfgas und führen dann die Schnüffelspitze des Geräts entweder manuell oder automatisiert über die neuralgischen Punkte der Oberfläche. Als Prüfgase eignen sich Helium oder Formiergas ebenso wie die gasförmigen Betriebsmedien, etwa R1234yf oder CO2.
Für die Verbindungsstellen von Klimaanlagen, Einspritzsystemen oder Batteriekühlkreisläufen empfehlen sich INFICON Geräte wie der HLD6000 und der Ecotec E3000. Ein Schnüffellecksuchgerät wie der Sensistor Sentrac, der kostengünstiges Formiergas verwendet, kommt dagegen bei der Prüfung von Öl- und Wasserkreisläufen von Verbrennungsmotoren zum Einsatz. Geräte wie der INFICON XL3000flex und der Protec P3000XL eignen sich wegen ihres hohen Gasflusses sogar für die dynamische Roboterschnüffellecksuche.
Kostenloses E-Book downloaden
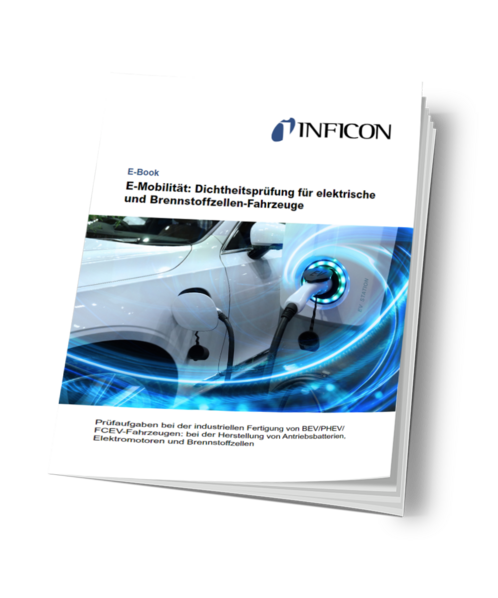
Kostenloses E-Book downloaden

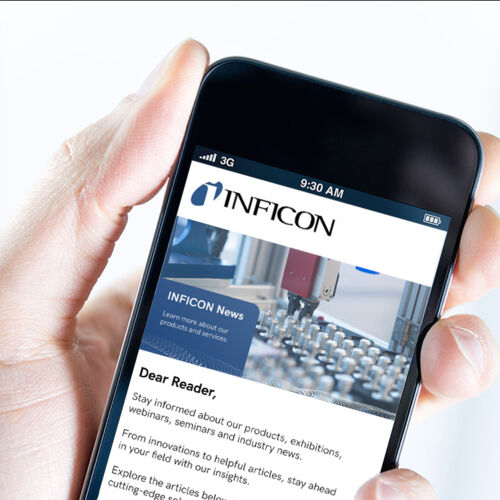