Factory Scheduler
Das leistungsstärkste, effizienteste und intelligenteste Scheduling-System für Industrie 4.0-Fabriken
Optimieren Sie den Output Ihrer Fabrik mit Scheduling: Produktionslinienbalance, Los-Bewegungen, Durchlaufzeit, Anlagendurchsatz und -auslastung, Bedienerproduktivität und Liefertreue.
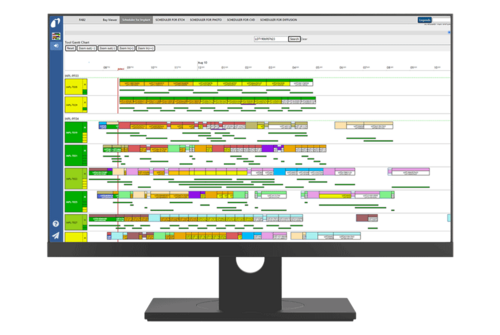
Intelligente Planung für intelligente Fabriken
Der INFICON Factory Scheduler basiert auf mehr als 20 Jahren Erfahrung in der Herstellung und im Betrieb von optimierten und robusten WIP-Schedulern für alle Bereiche des Fertigungsprozesses.
Der Factory Scheduler nutzt fortschrittliche Heuristiken, lineare Programmierung, Optimierung und intelligente Suchalgorithmen, um einen optimierten Produktionsplan in Echtzeit zu erstellen, der leicht an Ihre Produktionsanforderungen angepasst werden kann.
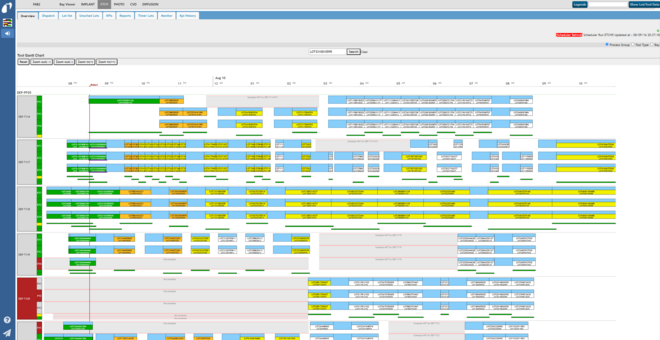
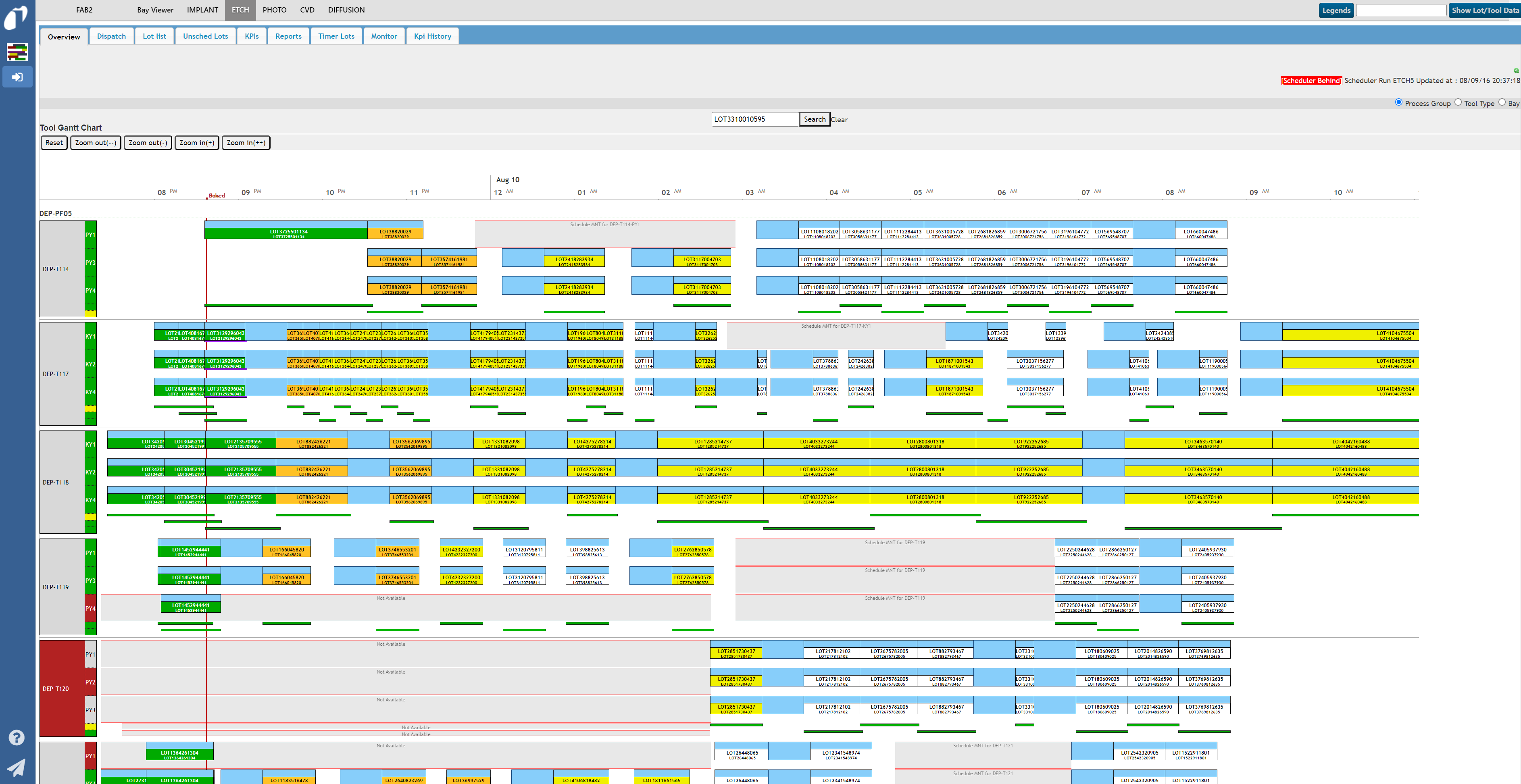
INFICON plant mehr als 2.000.000 Substrate pro Tag in Halbleiterfabriken auf der ganzen Welt.
Terminplanung ist KEINE Disposition
Dispatchregeln reichen nicht aus, um den WIP einer modernen Fabrik zu verwalten. Ihre Ausführung ist zwar einfach und besser als rein manuelle Entscheidungen, aber sie sind schwer zu pflegen, da sie sich nicht automatisch an veränderte Fertigungsbedingungen anpassen können. Im Vergleich zur Terminplanung haben Dispatchregeln erhebliche Nachteile:
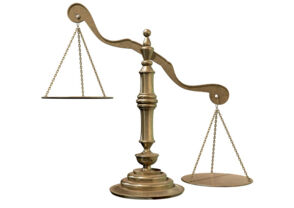
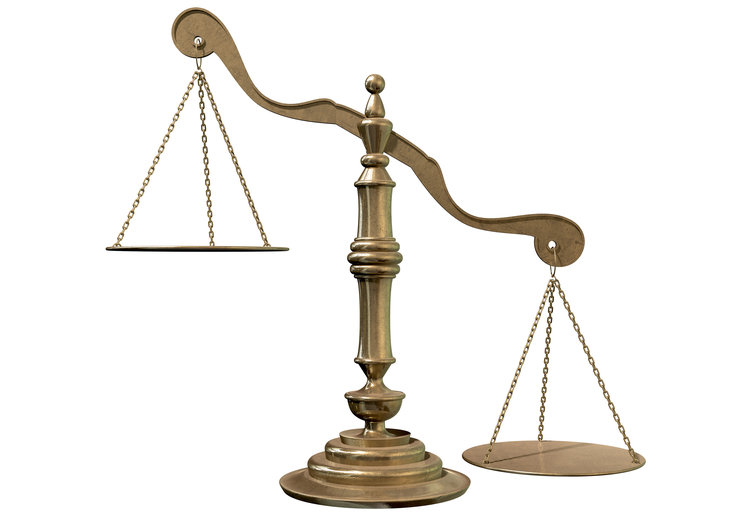
- Die Dispatch-Regeln sagen keine Ergebnisse voraus. Wenn ich dieses Werkstück jetzt bearbeite, wird es dann in der Lage sein, rechtzeitig die Liegezeit in 6 Schritten abzuschließen?
- Jeder lokale Schritt muss seine eigene Logik haben, die nicht synchron oder im Konflikt mit vor- oder nachgelagerten Regeln sein kann
- Regeln lassen sich nur schwer schnell an veränderte Anforderungen anpassen
- Globale Geschäftsziele lassen sich nur schwer in der Sprache der lokalen Dispatchregeln formulieren
- Die Regeln berücksichtigen in der Regel nur die Lose an der Anlage, nicht aber die in Kürze eintreffenden oder nachgelagerten.
- Die Ergebnisse geänderter Dispatchregeln lassen sich nur sehr schwer oder gar nicht im Voraus testen.
- Vorausschauen. Ein Scheduler hält an, wenn der Liegezeit eines Loses abläuft
- Sehen Sie die gesamte Linie. Faktoren wie das Gleichgewicht der Linie, defekte Maschinen, Inventar werden berücksichtigt.
- Berücksichtigen Sie Rüstzeiten, Reticle Wechsel, Transportzeiten usw.
- Erfassen Sie bevorstehende Wartungsereignisse
- Sorgen Sie für einen echten Ausgleich zwischen lokalen und globalen Prioritäten
- Erleichtern Sie die zentralisierte Geschäftslogik und geben Sie Fab-Managern die Kontrolle
- Ermöglichen Sie es, Änderungen hypothetisch zu testen, ohne die Produktion zu beeinträchtigen.
- Eröffnen Sie Möglichkeiten zur Integration intelligenter Fertigung - ein System, das "weiß", wo sich WIP befinden wird, schafft Möglichkeiten für die Verwaltung von Pumpen, Abgasreinigungsanlagen usw.
Terminplanung für Einrichtungen und Bereiche
Für kleine Fabriken kann ein einziger Area Scheduler ausreichen, um den gesamten WIP der Anlage zu planen. Für die meisten Fabriken mit hohem Produktionsvolumen installiert INFICON eine Gruppe von mehreren Area Schedulern, die zusammenarbeiten. Die Area Scheduler verfügen über eine modulare Logik, um die spezifische Komplexität des zu planenden Bereichs zu berücksichtigen - Lithographie, Diffusion, Implantation, Test, Dicing usw. Sie kommunizieren auch miteinander, um die globalen Prioritäten zu optimieren.
Entscheidungen verstehen
Das Gantt-Diagramm des Schedulers zeigt, wann und wo die Lose ausgeführt werden und wie die Entscheidung getroffen wurde. Die intuitive Benutzeroberfläche zeigt die Gründe an, die zur Platzierung des Loses im Zeitplan geführt haben, aufgeschlüsselt nach der Wichtigkeit der einzelnen Prioritäten. Auf diese Weise können die Ingenieure die Auswirkungen des aktuellen Produktionsplans auf die nachgelagerten Schritte erkennen.
Nicht nur ein Ersatz, sondern etwas Neues
INFICON Scheduler eröffnen Ihnen völlig neue Möglichkeiten in der Fabrik. Nehmen wir das Beispiel einer Anlage mit einem teuren Abgasreinigungssystem, das die Fabrikmanager zur Kostensenkung ins Visier genommen haben. Das System verfügt über einen Warmabschaltmodus, der die Betriebskosten um 95 % senkt, der aber nur während der Wartungsarbeiten an der Anlage genutzt wird. Der Factory Scheduler kann die Anlage nach Möglichkeit in die Planung einbeziehen und mit der richtigen Systemintegration automatisch den Abgasreinigungsmodus auslösen, wenn die Anlage nicht benötigt wird. So wie man das Licht ausschaltet, wenn man einen Raum verlässt. Fazit: Die Möglichkeiten, die der FPS Factory Scheduler bietet, sind ein Beispiel für die nächste Generation der KI-gestützten Fabrik der Zukunft.
Intelligente Back-End-Planung
Die WIP-Verwaltung und -Planung im Back-End-Bereich der Halbleiterindustrie wird immer wichtiger. Linienbalance, erhöhter Durchsatz und Auslastung sowie die genaue Einhaltung der Lieferziele sind im Back-End genauso wichtig wie im Front-End. Der INFICON Back-End Factory Scheduler verwendet fortschrittliche Algorithmen, die praktische Einschränkungen und Echtzeit-Informationen nutzen, um einen Zeitplan zu erstellen, der auf den aktuellen Bedingungen und Prioritäten basiert und kontinuierlich aktualisiert wird. Dies garantiert kontinuierlich relevante Ergebnisse inmitten der dynamischen Bedingungen der Backend-Anlage. Lieferinformationen aus früheren Operationen und Front-End-Einrichtungen werden als Input für die Back-End-Standorte verwendet und ermöglichen eine bessere Planung und Koordination von der Herstellung der Chips bis zur Montage und Prüfung.