Dichtheitstests an Li-Ionen-Zellen in der Serienfertigung
Kürzere Zykluszeiten und höherer Durchsatz in der Massenproduktion
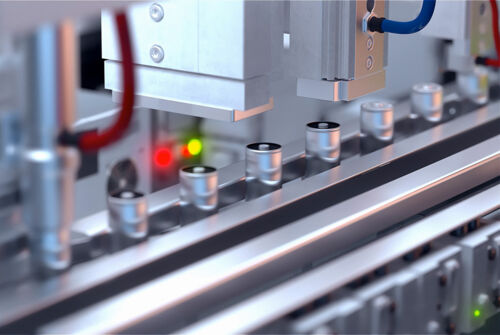
Für die Betriebssicherheit und Langlebigkeit moderner Traktionsbatterien ist auch die Dichtheit ihrer kleinsten Komponenten entscheidend: der Lithium-Ionen-Zellen. Es gilt, bei der Fertigung die Gehäuse sämtlicher Zellen auf ihre Dichtheit zu prüfen. Weder darf leicht entflammbares Elektrolyt austreten noch Luftfeuchtigkeit in die Zelle eindringen, denn Wasser kann mit dem Elektrolyt zu ätzender Flusssäure reagieren. In jedem Fall reduzieren undichte Zellen die Kapazität und die Lebensdauer von Traktionsbatterien. Bei der Fertigung ist zur Qualitätssicherung eine sorgfältige Dichtheitsprüfung unabdingbar.
Das ELT3000 PLUS Dichtheitsprüfgerät von INFICON erkennt direkt, wenn Elektrolytlösung aus einer Zelle in eine Vakuumtestkammer ausläuft. Dies macht es weitaus zuverlässiger als frühere Methoden, wie z. B. die Druckprüfung oder Heliumbombardierung. INFICON hat den ELT3000 PLUS so konzipiert, dass er sich für den Einsatz an manuellen Arbeitsplätzen in Entwicklungsabteilungen ebenso eignet wie für die Qualitätssicherung in automatisierten Fertigungslinien. Der ELT3000 PLUS erfüllt die Forderung nach hohem Durchsatz, der in der Serienfertigung ein wichtiger Faktor ist.
Hoher Durchsatz in der Serienfertigung durch leistungsfähige Vakuumpumpen
Zu den Maßnahmen, die die Zykluszeiten reduzieren, zählen
- ein möglichst kleines Totvolumen in der Vakuumkammer
- die Verwendung einer besonders leistungsfähigen externen Vakuumpumpe nebst zusätzlichen Ventilen für die Evakuierung und die abschließende Belüftung
- eine Reinigung der Zellen von Elektrolyt-Resten schon vor dem eigentlichen Testzyklus
Bei einer Prüfkammer von 1 l freiem Volumen (Volumen der Prüfkammer abzüglich des Volumens des Prüflings) besteht der typische voreingestellte Messzyklus des ELT3000 PLUS aus 5 s Reinigung der Zellen von Elektrolyt-Resten auf ihrer Oberfläche, 32 s Evakuierung der Vakuumkammer auf ca. 5 mbar abs., 6 s Dichtheitsmessung und 4 s Belüftung der Vakuumkammer – insgesamt also 47 s. Hinzu kommen die Prozesszeiten für das Beschicken mit und die Entnahme der Prüflinge aus der Kammer. Setzt man hingegen beispielsweise bei der gleichen Prüfkammer eine externe Pumpe mit einer Leistung von 100 l pro Minute ein, verkürzt sich die Evakuierungszeit von 32 s auf 12 s. Bei vorgereinigten Prüflingen (z.B. durch Laserreinigung) können zusätzliche 5 s Reinigungszeit entfallen und es ergibt sich insgesamt eine sehr deutliche Verkürzung des Messzyklus von 47 s auf 22 s.
Prüfanlagen mit mehreren Vakuumkammern
Eine zweite, sehr wirkungsvolle Option, den Durchsatz bei der Dichtheitsprüfung an befüllten Zellen mit einem einzelnen ELT3000 PLUS zu erhöhen, ist der parallele Einsatz mehrerer Prüfkammern. Während in der einen Kammer aktuell eine Messung stattfindet, kann eine zweite Prüfkammer bereits beschickt und eine dritte (und evtl. vierte, je nach Größe der Kammern und der Evakuierungszeit) bereits vorevakuiert werden. Der ELT3000 PLUS befindet sich dabei fast ausschließlich im Messbetrieb, so dass die zur Evakuierung benötigte Zeit eingespart werden kann und sich der Durchsatz deutlich erhöht.
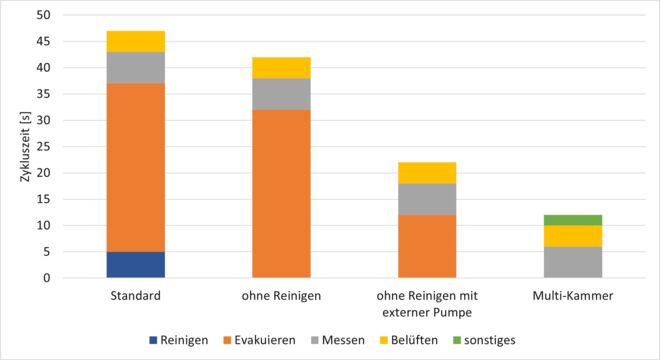
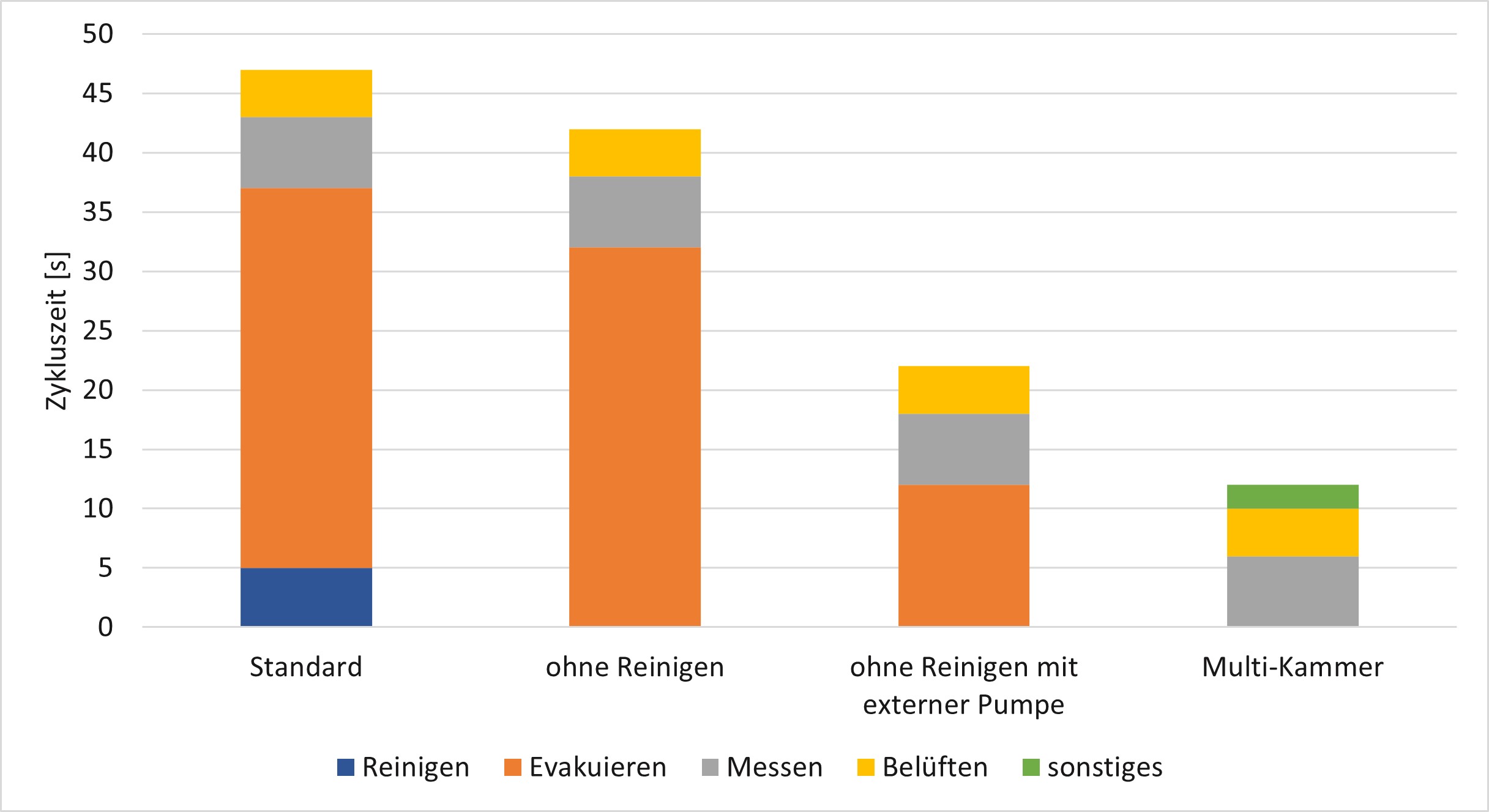
Batch-Testing für sehr hohen Durchsatz bei der Prüfung
Eine genauere Betrachtung zeigt allerdings, dass für die Dichtheitsprüfung der Durchsatz oft eine noch wichtigere Größe ist als die reine Zykluszeit. Der Durchsatz bei der Prüfung lässt sich durch einen Batch-Testing-Ansatz entscheidend reduzieren.
Nehmen wir an, in der beschriebenen Anlage mit externer Vakuumpumpe sollen Batches mit jeweils 16 Rundzellen vom Typ 21700 getestet werden, mit DMC als wesentlichem Lösungsmittel. Bei einer Zykluszeit von 22 s ergibt sich so eine Prüfzeit von 1,4 s für jede Zelle. Vergrößert man das Batch auf 64 Rundzellen, wird alle 0,3 s eine Zelle getestet. Ergibt ein Batch-Test ein Leck, gilt es, die undichte Zelle an einer manuellen Prüfstation zu identifizieren. Dazu wird die Batchgröße mehrmals halbiert, sodass immer das Batch, das die undichte Zelle nicht enthält, bei weiteren Tests ignoriert werden kann. Man nähert sich also auf iterativem Weg einem Batch der Größe 1: also dem, welches die schadhafte Zelle enthält. Bei 16 Zellen im ursprünglichen Batch ergeben sich nach diesem Prinzip vier weitere Prüfungsstufen, bei 64 Zellen sind sechs Stufen zur Vereinzelung nötig.
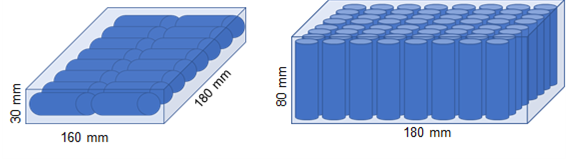
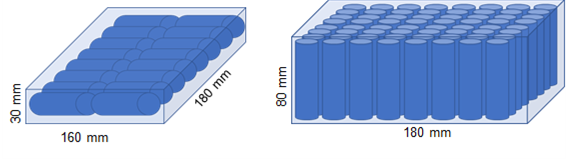
Zykluszeit [s] | Losgröße 16 Zellen | Losgröße 64 Zellen | |
---|---|---|---|
Standardgerät | 47 | 2,9 s / Zelle 20 Zellen / Minute | 0,7 s / Zelle 85 Zellen / Minute |
Mit externer Pumpe | 22 | 1,4 s / Zelle 42 Zellen / Minute | 0,3 s / Zelle 200 Zellen / Minute |
Die ideale Batchgröße bestimmen
Vor diesem Hintergrund ist es eine Optimierungsfrage, welche Batchgröße für einen bestimmten Anwendungsfall sinnvoll ist. Das ideale Batch für die Qualitätssicherung in der Linienfertigung lässt sich immer nur individuell bestimmen. Gehen wir beispielsweise von einer typischen Fehlerrate der Zellen von 0,5 Prozent der Produktion aus. Bei einer Batchgröße von 16 können bei einer Zykluszeit von 22 s in einer Schicht rund 20.900 Zellen geprüft werden. Darunter sind im Schnitt allerdings 105 16er-Batches, die undichte Zellen enthalten. Geht man von 30 s aus, die jede manuelle Prüfung nach einem der vier Batch-Halbierungsschritte benötigt, so ergibt sich für die manuelle Identifizierung aller undichten Zellen pro Schicht ein Zeitbedarf von rund 3,5 h. Arbeitet man in diesem Beispiel dagegen mit einer Batchgröße von 64 Zellen, lassen sich pro Schicht zwar 83.800 Zellen prüfen, aber es wird im Schnitt auch 420 Batches mit fehlerhaften Zellen geben. Gleichzeitig steigt die Zahl der erforderlichen Halbierungsstufen bei 64er-Batches auf sechs. Damit ergibt sich für die manuelle Identifizierung der undichten Zellen pro Schicht ein Zeitbedarf von rund 20,9 h.
Der ELT3000 PLUS in der Fertigungslinie
Grundsätzlich gibt es bei allen Arten von Lithium-Ionen-Zellen zwei Prozessschritte, nach denen Dichtheitsprüfungen mit dem ELT3000 PLUS sinnvollerweise durchgeführt werden können: einerseits nach dem Befüllen und Versiegeln und andererseits nach der Formierung der Zellen. Die Prüfung nach dem Versiegeln gestattet es, den Formierungsaufwand für undichte Zellen zu vermeiden und zugleich ein etwaiges Risiko durch die Formierung undichter Zellen auszuschließen. Eine zweite Prüfung, nach der Formierung, kann Lecks identifizieren, die durch das Handling entstanden sind – was besonders bei Pouch-Zellen möglich ist –, und sie stellt zugleich sicher, dass nur dichte Zellen zum Weitertransport kommen.
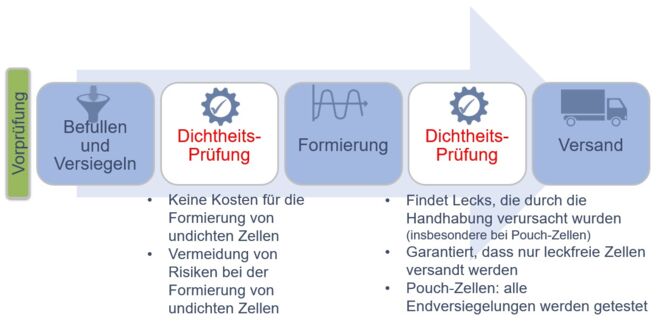
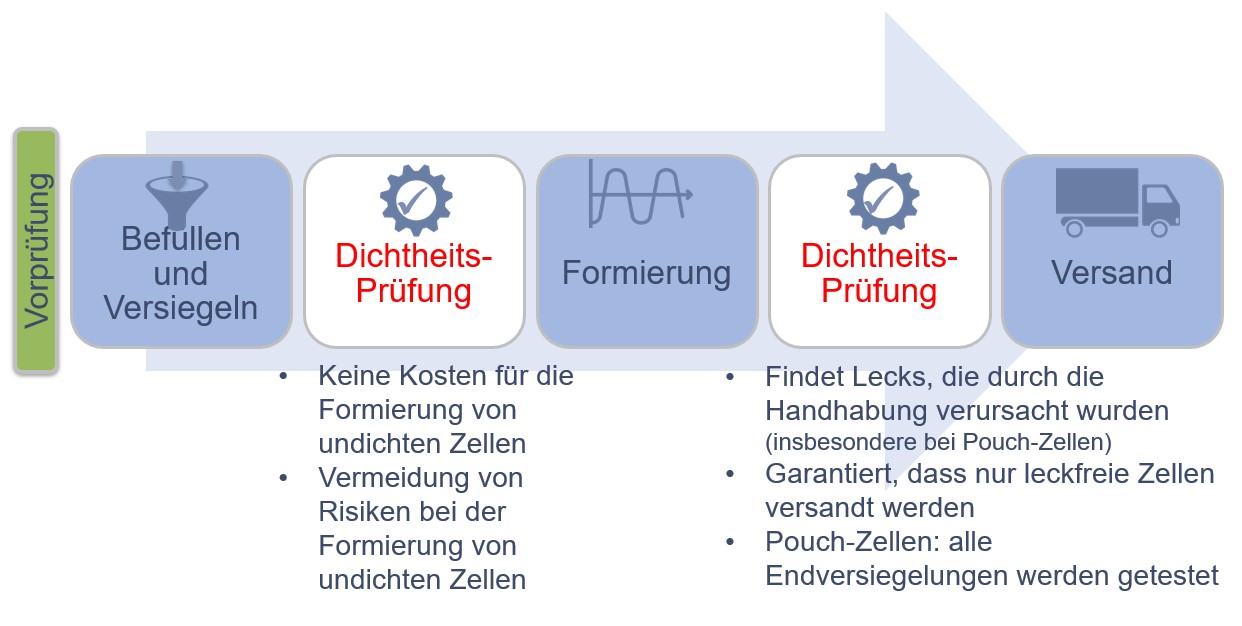
Direkter Nachweis von austretendem Elektrolyt-Lösungsmittel |
---|
INFICON hat ein neuartiges Verfahren entwickelt und patentiert, das erstmals in der Lage ist, Leckagen an fertig befüllten Zellen sehr zuverlässig zu detektieren, sei es an Zellen mit starrem Gehäuse wie prismatischen, Rund- oder Knopfzellen oder an flexiblen Pouch-Zellen. Das Besondere an der neuen Methode ist, dass sie direkt das Austreten von Elektrolytlösungsmittel aus einer Zelle in eine Vakuumprüfkammer nachweist. Damit ist sie weitaus zuverlässiger als bisherige Methoden wie Druckprüfung oder Heliumbombing. Das patentierte Dichtheitsprüfgerät ELT3000 PLUS von INFICON kann Lithium-Ionen-Zellen auf Lecks von wenigen Mikrometern Durchmesser prüfen, was einer Helium-Äquivalenz-Leckrate von 1∙10-6 mbar∙l/s entspricht. Eine flexible Folienkammer dient als Vakuumtestkammer für Pouch-Zellen und verhindert eine Beschädigung der empfindlichen Gehäuse. Damit ist es erstmals möglich, Pouchzellen auch nach der Befüllung auf Dichtheit zu prüfen. |
Wenn Sie mehr darüber erfahren möchten, wie der ELT3000 PLUS in der Serienproduktion eingesetzt werden kann, sehen Sie sich unser On-Demand-Webinar an oder wenden Sie sich an Ihren zuständigen Vertriebsmitarbeiter.