Foro de debate para suscriptores:
Boletín FabTime, Volumen 26, nº 2
Los suscriptores debaten sobre la variabilidad de las herramientas con y sin cuello de botella, los objetivos de equilibrio de turnos, las métricas para la linealidad del trabajo en curso, los lotes calientes y las limitaciones de los operarios.

Impacto relativo de la variabilidad del tiempo de llegada y de proceso para cuellos de botella frente a no cuellos de botella
Un nuevo suscriptor de Taiwán, tras estudiar los recursos de este boletín y consultar con un colega de la Universidad Nacional de Taiwán, observó que el impacto relativo de la variabilidad de la llegada frente a la variabilidad del tiempo de proceso dependerá de si un grupo de herramientas es un cuello de botella. Observó que
- Para las herramientas cuello de botella (alta utilización), un alto coeficiente de variación al cuadrado del tiempo efectivo del proceso resultará en un alto coeficiente de variación al cuadrado del proceso de salida, independientemente de si el coeficiente de variación del tiempo entre llegadas a la herramienta es alto o bajo. Esto se debe a que la cola casi constante en una herramienta cuello de botella absorberá la variabilidad de las llegadas. Cuando los lotes llegan al final de una larga cola, se amortigua el impacto de cualquier variación en el patrón de llegada de esos lotes.
- Para las herramientas que no son cuellos de botella (de baja utilización) y que no suelen tener una cola de espera, un coeficiente de variación al cuadrado elevado del proceso de llegada dará lugar a un coeficiente de variación al cuadrado elevado del proceso de salida, independientemente de que el coeficiente de variación del tiempo efectivo del proceso sea elevado o reducido.
Respuesta de Jennifer: Creo que estos puntos son intuitivamente razonables. He dicho muchas veces en mi clase de tiempo de ciclo que cuando los lotes llegan al final de una larga cola, el impacto de la variabilidad de la llegada es menor. En el caso de baja utilización, sin mucha cola para absorber la variabilidad de llegada, tiene sentido que esta variabilidad de llegada se transmita aguas abajo, potencialmente aumentada por la variabilidad del tiempo de proceso.
Considere las versiones más sencillas de las fórmulas de colas para generar curvas operativas, cuando estamos viendo el factor x en el grupo de herramientas actual. Para más detalles, consulte nuestro seminario web sobre los factores fundamentales de la duración del ciclo de fabricación de obleas (el vídeo se encuentra en la parte inferior de la página web enlazada). En este caso, no importa mucho si la variabilidad proviene del tiempo entre llegadas o de los tiempos de proceso, porque CVa y CVpse ponderan por igual en la fórmula (aunque la variabilidad efectiva del tiempo de proceso también se verá influida por la distribución del tiempo de inactividad cuando ampliemos un poco la fórmula, como se explica en el número 25.04).
Sin embargo, hay que tener en cuenta un par de puntos:
- Las fórmulas de las colas (tal y como se reflejan en la hoja de cálculo de la curva operativa) siguen mostrando que la variabilidad de las llegadas tiene un impacto significativo en el factor x del tiempo de ciclo a utilizaciones extremadamente altas. Sin embargo, en una fábrica real, este efecto se ve atenuado por el hecho de que no tenemos un WIP infinito. Nunca vemos (¡esperemos!) los factores x más altos que el modelo de colas predice a partir de una alta utilización y variabilidad, porque nuestro WIP está limitado.
- Aunque el tiempo medio de espera puede ser bajo para las herramientas sin cuellos de botella (porque los lotes suelen llegar cuando la herramienta no está ocupada), debemos recordar que la variabilidad no sólo afecta a la herramienta actual. La variabilidad de las llegadas a herramientas de baja utilización repercute en la variabilidad del proceso de salida, que se convierte en la variabilidad de las llegadas para los pasos posteriores.
Agradecemos esta contribución al debate. Siempre hay más cosas que aprender y sobre las que reflexionar para entender el comportamiento de los animales.
¿Cómo deben los supervisores asignar operadores para equilibrar los diferentes objetivos de tasa de turnos?
Un antiguo suscriptor escribió: "¿Cómo tratar a los supervisores de turno que deben rendir cuentas de los turnos? Podrían ser responsables de tres áreas (CMP, Epi, Implant), cada una de ellas con una expectativa de turnos muy diferente. Como somos una empresa ajustada, los empleados están formados para trabajar en las tres áreas.
La naturaleza humana hace que los supervisores envíen personal al área de mayor rotación. Esto puede causar problemas al área con menor tasa de turnos (Epi), que no puede ponerse al día si se queda rezagada. ¿Puede utilizar 'Gráficos de Salud de Área' que normalicen los turnos por hora superpuestos a cada área, mostrándole dónde enviar personal?"
Respuesta de Jennifer (tras consultar con Paul Campbell, nuestro especialista en fabricación inteligente):
Creo que las vueltas son más útiles a nivel de fábrica, como indicador del ritmo de la línea. Para una ruta determinada, el índice de vueltas, junto con un número aproximado de pasos por flujo, puede ser un indicador adelantado del tiempo de ciclo. Si el índice de turnos disminuye, es una advertencia temprana de que el tiempo de ciclo futuro aumentará.
La idea que subyace al uso de los turnos para las áreas es que los turnos tienen en cuenta la escasez y el exceso de trabajo en curso, por lo que no penalizamos a la persona que dirige el área por no cumplir un objetivo de movimientos cuando no hay suficiente trabajo en curso. Sin embargo, los turnos no son una métrica principal ideal para las áreas, porque utilizar turnos a nivel de área puede perjudicar el equilibrio de la línea y aumentar la variabilidad.
Un objetivo de turnos alto en un área significa que esperamos hacer un gran número de movimientos en esa área durante el turno o que esperamos tener un WIP bajo en el área. En este último caso, esto anima a las áreas con un WIP bajo a realizar movimientos que pueden no ser ideales desde la perspectiva de la fábrica. Por el contrario, un objetivo de turnos bajo significa que, o bien esperamos no hacer demasiados movimientos, o bien estamos reteniendo mucho WIP en el área. En este último caso, el uso de turnos desincentiva la realización de movimientos (y la asignación de asociados), aunque mantener ese WIP en movimiento sería útil para mejorar el tiempo de ciclo. Esto suena exactamente a lo que describes en el área de Epi (turnos bajos) frente a las otras.
Creo que el hecho de que la tasa de turnos dependa tanto de los movimientos como del WIP lo hace imperfecto para decidir dónde enviar personal. También tengo experiencia en que la tasa de turnos por hora en una zona puede ser muy variable. Parece una pregunta a la que debería responder un planificador (como el planificador de fábrica de INFICON), estableciendo objetivos para el trabajo en curso específico que debe moverse durante el turno. Si evitar que Epi se quede atrás es una prioridad o una restricción, entonces el programador debería dar prioridad a que alguien realice esos movimientos de Epi. De este modo se evita la parte de "naturaleza humana" de la decisión.
Otra forma de pensar en esto es ver qué grupos de herramientas son las herramientas de restricción para la fábrica. Esas son las herramientas que queremos asegurarnos de que no se queden paradas con WIP esperando porque no hay asociados para hacer funcionar la herramienta. Si los supervisores ven que esto ocurre, deberían enviar personal a esos lugares.
Otra idea para mejorar el rendimiento de las áreas es utilizar una métrica que desarrollamos con un cliente en 2013 llamada Horas de Plan Ganadas (EPH). EPH es una alternativa a los movimientos para el seguimiento de la actividad de producción. EPH da crédito tanto cuando los lotes se llevan a las herramientas como cuando se procesan en las herramientas. De este modo, EPH ofrece un incentivo para mantener las herramientas en funcionamiento, incluso cerca del cambio de turno. (Para más detalles, véase el número 14.01, disponible para suscriptores en el archivo del boletín FabTime).
Mi respuesta aquí no es compartir una forma mejor de utilizar los turnos para evitar este problema, sino proponer que otras métricas pueden ser mejor utilizadas para el seguimiento del rendimiento del área. Lo siento si no es de ayuda.
Me encantaría que otros abonados me dijeran si utilizan los turnos de esta manera o si tienen alguna sugerencia. ¿Alguien tiene algo que añadir?
Métricas para la linealidad de WIP
Un nuevo suscriptor ha preguntado: "¿Existe alguna métrica establecida para cuantificar y visualizar el balance WIP en una línea de fabricación que pueda utilizarse para mostrar una tendencia? Buscamos algo que destaque los movimientos que faltan en partes del flujo, así como los movimientos 'excesivos' en otras partes del flujo. Tal vez usted me puede apuntar a los documentos correspondientes".
Respuesta de Jennifer: Una métrica que tenemos en el software de reportes FabTime que podría capturar esto es WIP Goal Delta. Los datos para este gráfico se calculan inicialmente a nivel de objeto por lo que el cliente elige cortar y luego se pueden agregar en el tiempo para ver las tendencias. Para observar la linealidad de la línea, lo que se puede hacer si la fábrica se encuentra en un estado relativamente estable en términos de arranques es buscar por segmento o subsegmento de la línea (normalmente un segmento es aproximadamente una semana de flujo de proceso, mientras que los subsegmentos son más pequeños) y establecer un objetivo de WIP que sea el mismo para cada segmento. A continuación, puede observar el delta absoluto entre ese objetivo y el WIP real por segmento, sumado en todos los segmentos, e informado a lo largo del tiempo. Lo que se busca es un delta absoluto lo más cercano posible a cero. Tenga en cuenta que si los niveles de WIP en la fábrica cambian, y/o la tasa de inicio cambia significativamente, podría ser necesario ajustar los objetivos.
He aquí un ejemplo de una instantánea de este objetivo WIP Delta por segmento:


Podemos ver que los segmentos tempranos y tardíos cumplen bien el objetivo de trabajo en curso, pero los segmentos del medio son más variables. Y aquí tenemos una versión ampliada de la tendencia:


La altura de la barra situada más a la derecha en el gráfico inferior es la suma de los valores absolutos mostrados en el gráfico superior. Cuando los objetivos de los segmentos son los mismos, los valores más bajos de este gráfico indican una mejor linealidad. Me gusta esta métrica porque es flexible (puede definir los segmentos o subsegmentos como desee).
El Planificador INFICON y el Cuadro de Mando de Fábrica también utilizan una métrica de equilibrio de líneas para garantizar la Linealidad WIP. Los cálculos se basan de forma similar en el valor absoluto del mayor delta efectivo al objetivo WIP o el mayor objetivo WIP de la instalación, el que sea mayor.
¿Algún otro suscriptor tiene otras métricas que sugerir aquí para mantener la linealidad WIP?
¿Por qué no aparecían los lotes calientes en la lista de factores que influyen en el tiempo de ciclo en el número anterior?
Un antiguo suscriptor escribió en respuesta al número de febrero: "Me pregunto por qué los pasillos prioritarios (por ejemplo, los lotes calientes) no aparecen en la lista de factores perjudiciales para la duración del ciclo de fabricación de obleas, ya que complican la entrega a tiempo y aumentan la variación de la duración del ciclo de fabricación para los lotes normales".
Respuesta de Jennifer: Gracias por notar que los lotes calientes no estaban en la lista del gráfico. Se debe a un error de edición por mi parte. Revisé la hoja de cálculo que utilicé para compilar los resultados, que había reformateado desde la publicación del número anterior sobre este tema, y descubrí que había combinado lotes calientes con retenciones. En la siguiente figura aparecen correctamente separados (nueve respuestas para las reservas y tres para los lotes calientes).
Esta pregunta de la encuesta, que estuvo durante un tiempo en el sitio web de FabTime, recibió 123 respuestas en total. Como sólo se podía elegir un factor, no me sorprende que no se eligiera con frecuencia el lote caliente. Creo que el tiempo de inactividad, la utilización de herramientas y la mezcla de productos tienen un mayor impacto en la mayoría de las fábricas, aunque estoy de acuerdo en que los lotes calientes aumentan la variabilidad (y a veces causan pérdidas de capacidad), y por lo tanto tienen un impacto en el tiempo de ciclo de la fábrica.
Para más información sobre el impacto de los lotes calientes en el tiempo de ciclo, véanse los números 19.03 y 25.01.

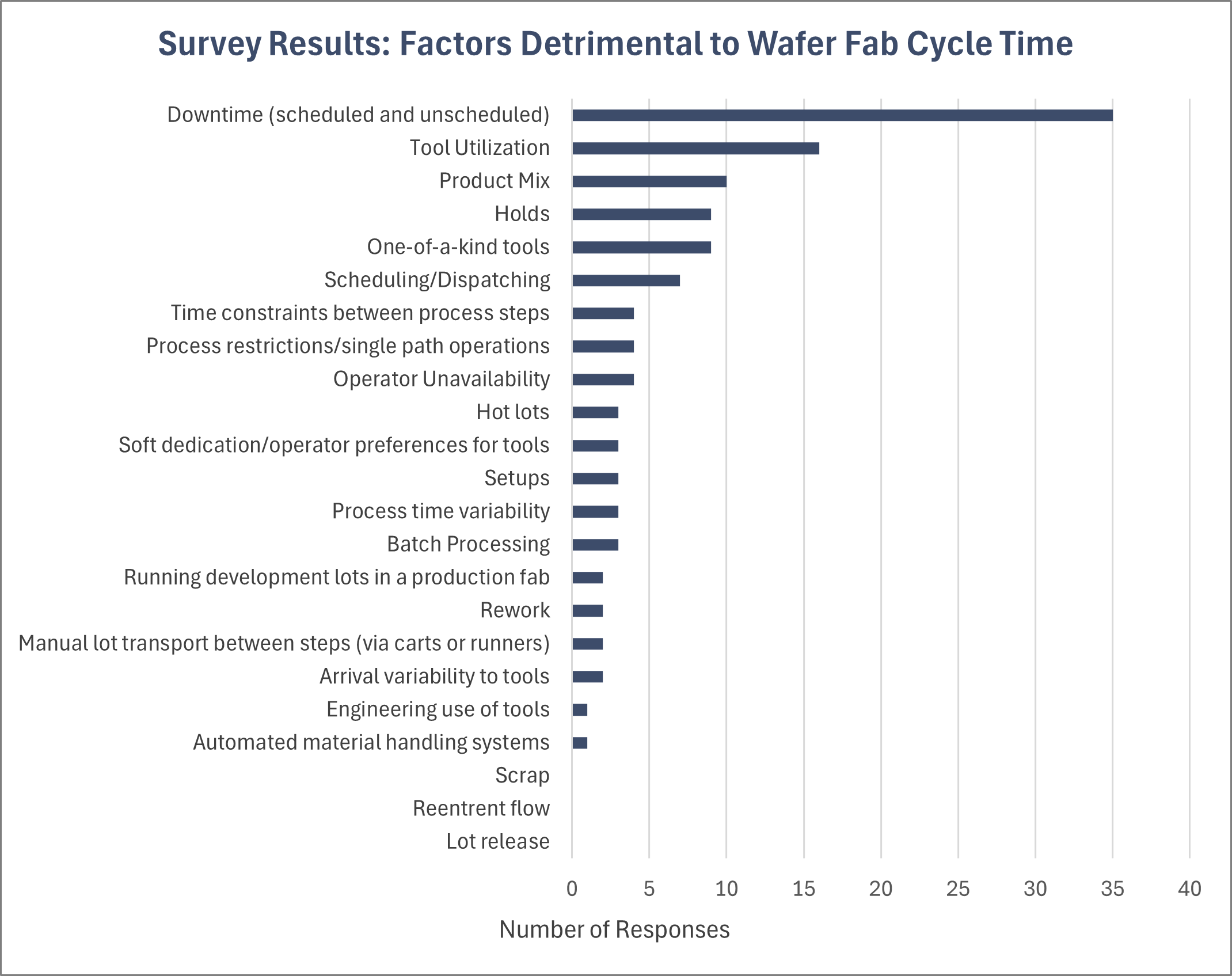
¿Cómo puedo modelar las restricciones del operador?
Un nuevo suscriptor escribió: "Una de las áreas que me interesan no es sólo la utilización de los equipos, sino también la utilización de las personas. He encontrado su boletín sobre este tema, pero también me interesaría saber cómo modelizar eficazmente esta limitación junto con los otros tres factores que influyen en el tiempo de ciclo".
Respuesta de Jennifer: No tenemos mucho contenido sobre el impacto de los operadores más allá de lo que se incluye en nuestros boletines anteriores sobre ese tema, aunque también discutimos esto en nuestra clase de tiempo de ciclo.
En general, se puede pensar en cómo los operadores afectan a los tres impulsores fundamentales del tiempo de ciclo.
- Los operarios aumentan efectivamente la utilización porque se acaba teniendo:
a. Tiempo de proceso inflado porque no hay operario disponible para descargar la herramienta (que a veces se puede medir como tiempo de post-proceso); o
b. Capacidad desperdiciada debido a que las herramientas están paradas con trabajo en curso delante de ellas porque no hay operario para cargar la herramienta (que puede medirse como tiempo de espera de trabajo en curso, como se muestra a continuación).
- Los operarios aumentan la variabilidad. Sin embargo, esto puede ser difícil de cuantificar.
- Los operarios pueden reducir el número de herramientas cualificadas disponibles. Esto ocurre cuando no se pueden poner en marcha herramientas porque no hay suficientes operarios, o cuando los operarios simplemente no ponen en marcha tantas herramientas como se espera, lo que da lugar a una dedicación blanda.


Yo me centraría sobre todo en el número 1. Intentar medir en qué puntos los operarios aumentan la utilización de las herramientas, sobre todo en las herramientas que suponen un cuello de botella. A continuación, intente reasignar a los operarios allí donde el tiempo de ciclo sea mayor. INFICON puede ayudarle a extraer estos datos con FabTime y Factory Dashboard, pero puede que sus supervisores ya sepan dónde está ocurriendo esto. ¿Otros suscriptores tienen algo más que sugerir aquí?
Agradecemos la oportunidad de publicar las preguntas y respuestas de los suscriptores.
Los suscriptores pueden descargar los números anteriores del boletín en formato PDF. Los suscriptores actuales pueden encontrar el enlace al archivo en su boletín electrónico más reciente. Los nuevos suscriptores verán el enlace al registrarse.
- Artículo principal del Volumen 26, nº 2: ¿Es posible una definición estándar de los movimientos?
- Página de anuncios comunitarios del Volumen 26, nº 2
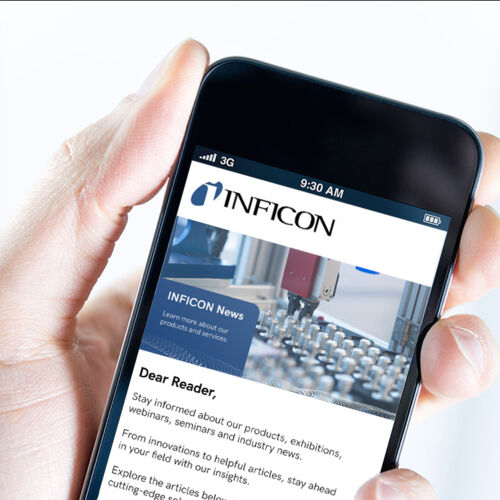
¿Quiere saber más sobre los controladores del tiempo de ciclo en su fábrica?
