Cómo una calibración adecuada puede mejorar la calidad de su producción
Movimientos sencillos con gran impacto.
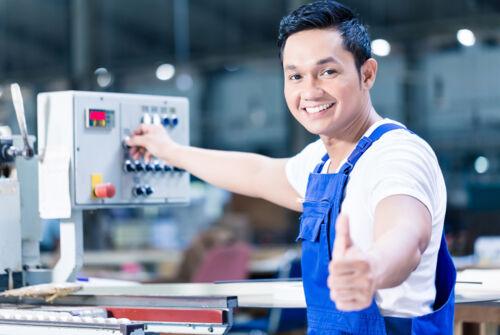
David Xu, un diligente y dedicado ingeniero de producción que trabaja en una renombrada empresa de fabricación de celdas de baterías de iones de litio, tiene una responsabilidad crucial: es el encargado de realizar las pruebas de fugas de helio en las celdas de las baterías antes de llenarlas de electrolito.
Para llevar a cabo esta importante tarea, David confía en un sistema automatizado de comprobación de fugas de helio diseñado por sus colegas del departamento de integración de sistemas. Sin embargo, a pesar de utilizar este sistema de alto rendimiento, persisten los problemas de calidad. Algunas celdas de batería no superan la prueba de final de línea o presentan problemas poco después de ser enviadas, lo que da lugar a reclamaciones de garantía y a la insatisfacción del cliente.
Decidido a resolver estas cuestiones, David decidió investigar más a fondo el problema. Se dio cuenta de que la clave podía estar en el proceso de calibración del sistema de comprobación de fugas de helio. En colaboración con sus compañeros, David se aseguró de que el sistema se calibrara al principio de cada turno utilizando una fuga de prueba que coincidiera con la fuga más pequeña que necesitaban detectar.
A pesar de sus esfuerzos, los problemas de calidad persistían y David se sentía cada vez más frustrado. Fue entonces cuando se topó con un seminario web sobre pruebas de fugas de helio que le abrió los ojos. El seminario puso de relieve la importancia de la ubicación de la fuga de prueba.
Movido por la curiosidad, David inspeccionó la configuración del sistema de prueba de fugas de helio y descubrió que la fuga de prueba estaba instalada muy cerca de la entrada del detector de fugas. Consciente del impacto potencial de esta configuración en la precisión de los resultados, David se puso inmediatamente en contacto con su departamento de integración de sistemas.
Juntos, intentaron primero conectar la fuga de prueba directamente a la cámara e iniciar la medición. Para su sorpresa, el sistema no detectó la fuga. Esto sólo podía significar que también podía haber un problema con el detector de fugas. Decididos a resolver este problema, decidieron cambiar el detector de fugas y volver a calibrar el sistema con la fuga de prueba conectada a la cámara. Esta vez, el sistema detectó con éxito la fuga, lo que confirmó su sospecha de que la configuración anterior no era tan eficaz como esperaban y ahora están seguros de que por fin tienen un tiempo de medición adecuado y una calibración correcta del sistema.
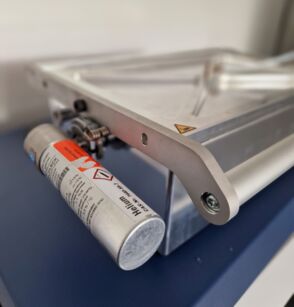
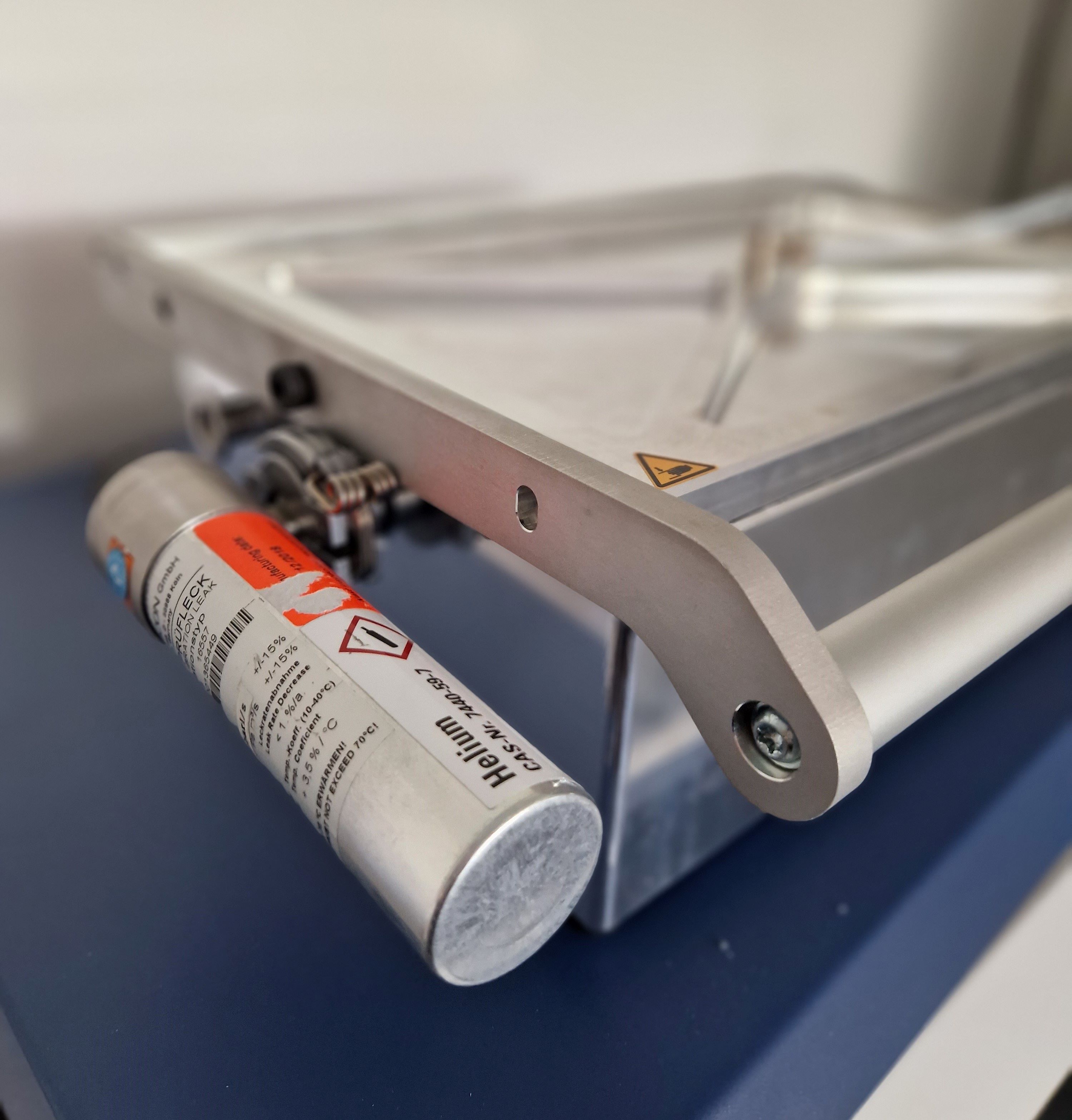
Con la implantación de estos cambios en el proceso -nuevo detector de fugas y ubicación de la prueba de fugas directamente en la cámara-, la empresa es testigo no sólo de una reducción significativa de los fallos de las baterías durante la prueba de final de línea, sino también de los fallos tempranos sobre el terreno. Las pruebas de baterías son más fiables y acaban cumpliendo los estándares de calidad que esperan los clientes.
Reconociendo el compromiso de David, su capacidad para resolver problemas y su contribución a la mejora de la calidad de los productos de la empresa, recibió una recompensa de control de calidad por este gran logro. Su dedicación y perseverancia no sólo habían resuelto un problema crítico, sino que también habían supuesto un gran reconocimiento a su trabajo.
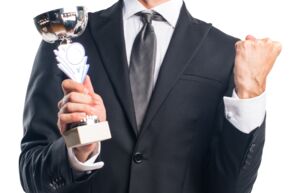
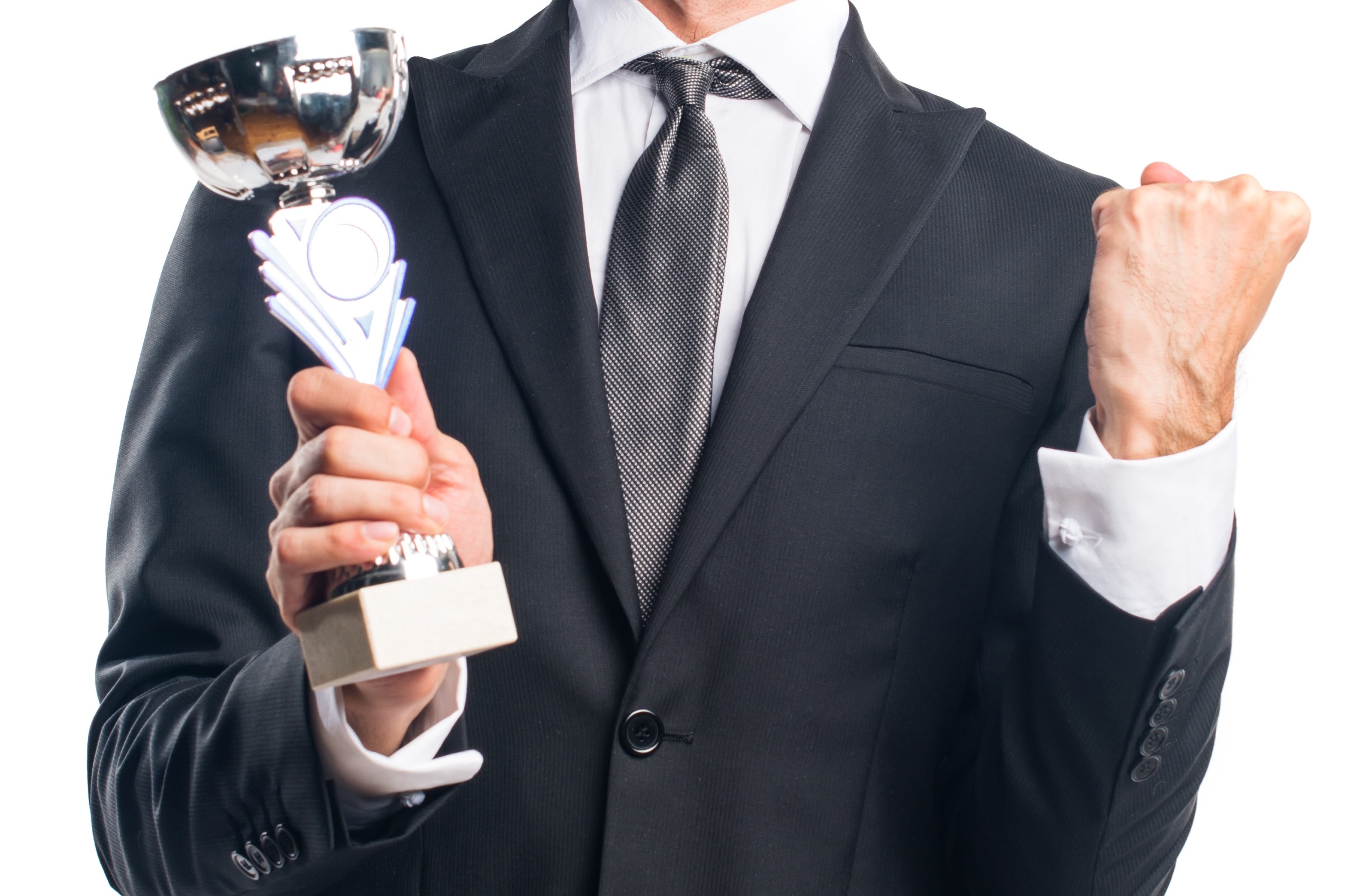
Así pues, la historia de David Xu sirve para recordar la importancia de la mejora continua, la atención al detalle y el impacto que incluso los pequeños cambios pueden tener en la calidad general del producto.