ウェハ製造工場におけるワディントン効果
定期メンテナンスの実施により、予定外のダウンタイムが短期的に増加する可能性があるという状況を探る。
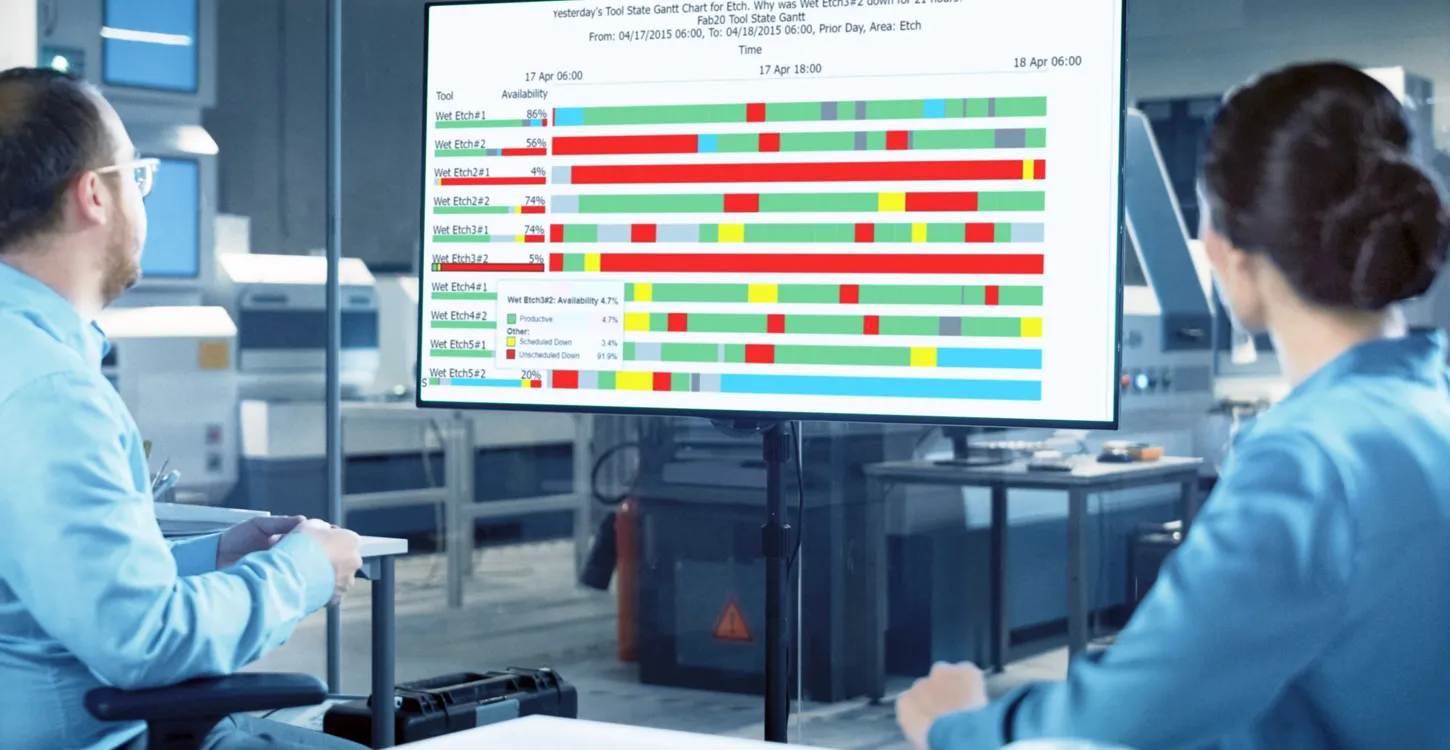
ジェニファー・ロビンソン
我々が推奨してきたように ダウンタイムが工場のサイクルタイムに与える影響を軽減するための測定基準, 私たちが不思議に思っているのは、ワディントン効果の影響である。 著者ジェームズ・P・イグニツィオによって命名され、広められた「ワディントン効果」は、第二次世界大戦時の英国空軍のB-24リベレーター爆撃機の整備に関する研究に基づいている。 研究者C.H.ワディントンと彼のチームは、これらの航空機の定期整備があまりに頻繁であれば、"比較的満足のいく状態を乱すことによってプラスの害をもたらす "可能性があることを発見した。 具体的には、ワディントンは、定期整備後に予定外のダウンタイムイベントが減少するのではなく、むしろ増加することを発見した。 参照マイク・ブッシュによるスポーツ・アビエーション誌の記事 を参照されたい)。
この結果は、このニュースレターで推奨していることと矛盾する可能性がある。22.01号, 例えば)そして、メンテナンスイベントをグループ化することを控えるためのサイクルタイムコース。 私たちは、利用できない時間が長い方が短いよりもサイクルタイムにとってずっと悪いという観察に基づいて、そのように主張してきた。 他のすべての条件が同じであれば、これは確かに真実である。 しかし、定期メンテナンスの頻度が高くなると、予定外のダウンタイムが長くなり、サイクルタイム全体が悪化する可能性があります。
この記事では、ワディントン効果とワディントン効果プロットを紹介します。 そして、より頻繁なメンテナンスを推奨する私たちと、より少ない頻度でメンテナンスを行うことを推奨するワディントンの暗黙の推奨との間の明らかな矛盾に対する解決策を提案します。 いつものように、ご意見をお待ちしております。
ワディントン効果とは何ですか?
に掲載されたジェームズ・イグニツィオの記事によると、この記事には次のように書かれている。 PHALANXマガジン2010年9月号 (Military Operations Research Societyの季刊誌)によると、C・H・ワディントンは遺伝学者で、第二次世界大戦中にイギリスの軍事作戦研究グループに配属された。 作戦研究グループは、航空機が飛行と飛行の間に地上で過ごす時間を短縮することによって、イギリスの爆撃機司令部の効果を高めるよう要請された。
イグニツィオは次のように報告している:
「ワディントンと彼のチームは、うまくいくかもしれないし、うまくいかないかもしれない計画について慌ただしく説明する前に、立ち止まって考える大胆さを持っていた。 彼らは裏付けとなるデータを要求し、分析し、メンテナンスクルーと話し、実際のメンテナンスの様子を注意深く個人的に観察する時間をとった。
イグニツィオは、彼らが発見したものを「ワディントン効果」と呼んだ。 彼らは、予定外のダウンタイムイベントの数を、直近に予定されていたメンテナンスイベントからの時間と共にプロットした。 彼らのグラフによると、定期メンテナンス・イベントの直後から、必要な修理の回数は増加し、次のメンテナンス・イベントが予定される頃まで、時間とともに減少していった。
ワディントンは次のように結論づけた(イグニツィオの引用による):
「検査は故障を増加させる傾向があるが、これは検査が比較的満足のいく状態を乱すことによって害を及ぼしているからにほかならない。 第二に、40~50時間の飛行時間の後、故障率が再び増加し始める兆候はない。
言い換えれば、イグニツィオは言う:
"ワディントン効果とは、予定されたイベントの後に予定外のイベントが "密接に "発生し、その数と頻度が "急増 "し、その後、予定外のイベントの発生率が "より正常なレベル "まで徐々に低下し、次の予定されたメンテナンス・イベントの後にこの同じ厄介な効果が繰り返されることである。"
この効果に対してワディントンのチームが提案した解決策は、メンテナンス・イベントの実行とそのスケジューリングを改善することであり、これにははるかに優れた文書の追加も含まれた。 これらの改善の結果、装備や人員を増やすことなく、イギリス沿岸軍航空隊の有効規模を60%増加させることができた。 産業工学がなし得ることは驚くべきことではないだろうか。
ワディントン効果は、多くの機械装置で観察される浴槽型の故障率曲線のうち、低下する故障率(DFR)の一部と考えられる。 初期不良による故障率の低下期には、比較的一定の故障率(CFR)の期間が続きます。 その後、システムが老朽化し、磨耗し始めると、故障率が増加する期間(IFR)が観察される。 (詳細はHopp and SpearmanのFactory Physicsのテキスト(Irwin, 1996)を参照)。 ウェハーファブでは、IFRの結果は高いので、PMは理想的には、故障率が増加するその後の期間の前に行われる。
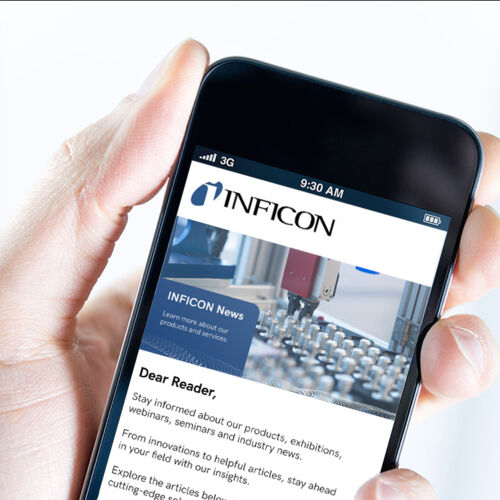
ワディントン効果図とは何ですか?
Ignizio 氏の著書、"Optimizing Factory Performance" (McGraw Hill, 2009) の中で、彼は、工場における機器のダウンタイムを分析し、削減するために、ワディントン効果プロットの使用を提案している。 ワディントン効果プロットは、ワディントンと彼のチームが使用したようなグラフであり、予定外のダウンタイムの増加が予防メンテナンスイベント(PM)に密接に続いている状況を識別するためのものです。
ツールのワディントン効果プロットを作成するために、Ignizio氏は、各時間をX軸に沿った棒グラフを作成し、棒グラフの高さがその時間のダウンタイム量を示し、スケジュール済みかスケジュール外かを色分けすると言います。 イグニツィオは、40時間ごとに5時間(平均)のPMを必要とする工具の実際の工場データに基づいた例を著書で紹介している。 この例では、PMの直後に予定外のダウンタイムがかなり発生し、その後12時間かけて漸減していくことを示している。
エクセルで作成した同様の例を以下に示す。 最初の長いPM(黄色で表示)は3.8時間続き、その後すぐに2.7時間の予定外のダウンタイムが続く。 さらにダウンタイムが続き、その後先細りとなる。 2回目の長いPMは4.5時間続き、同様に予定外のダウンタイムが増え、その後先細りとなる。
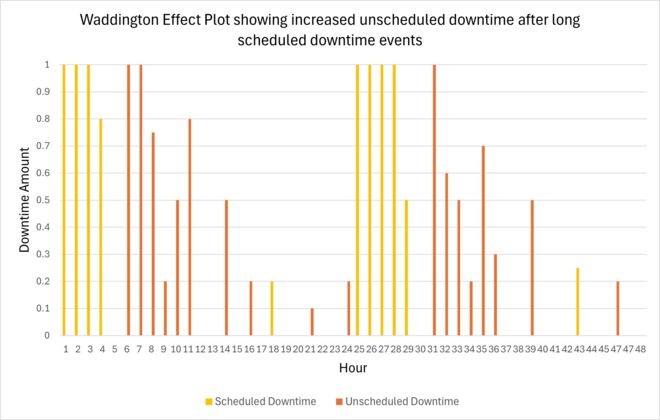
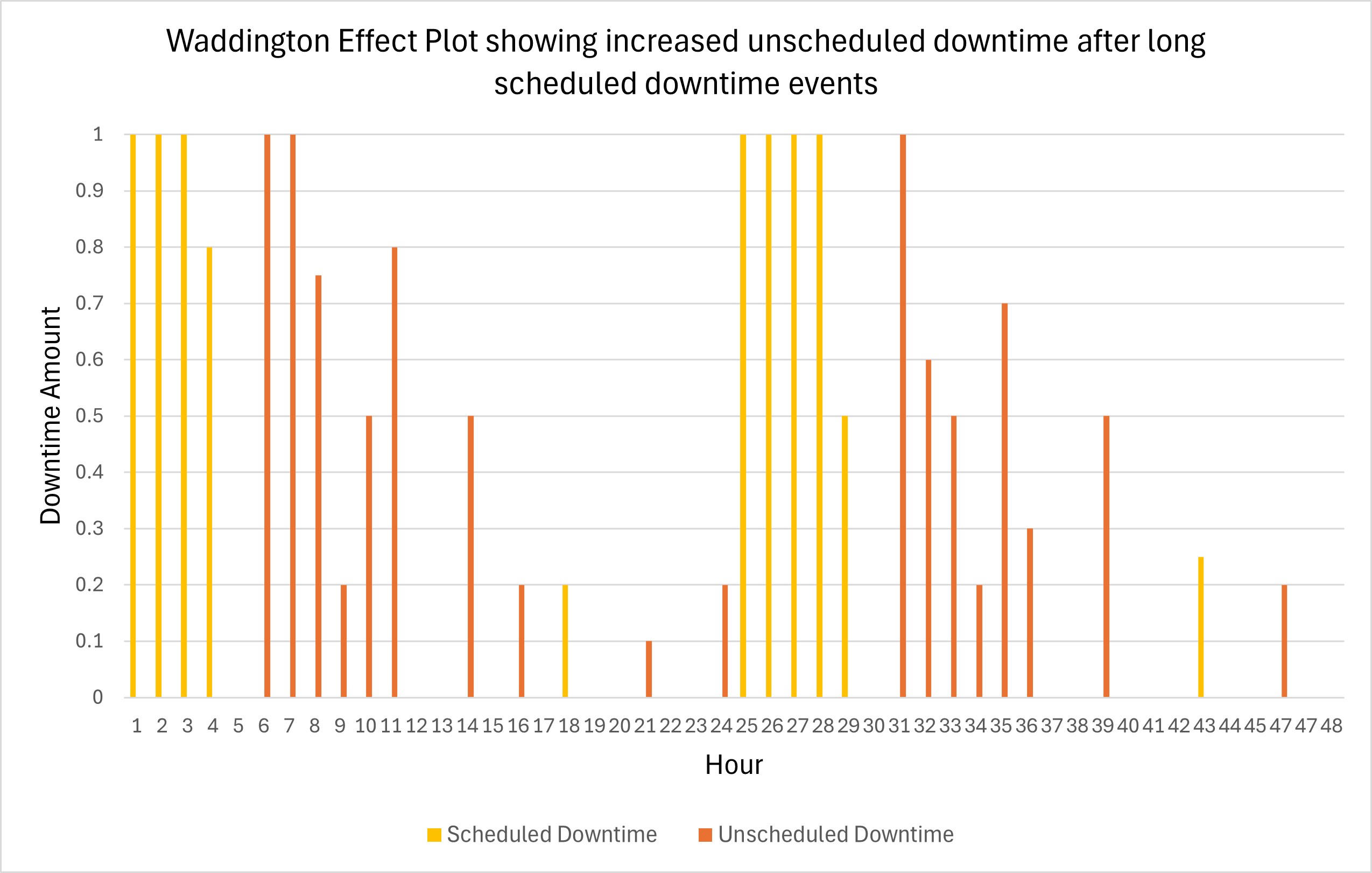
この作為的な例では、チャートを見ただけで、ワディントン効果が起こっている可能性があると推測するのは簡単である。 しかしもちろん、これらのプロットを実際に使うのであれば、a) 継続的に簡単にプロットを作成する方法、b) データから自動的にワディントン効果を検出する方法、c) ワディントン効果を検出した場合に次に何をすべきかのアドバイスが欲しい。 これらを順番に見ていきましょう。
FabTimeを使用してワディントン効果図を作成するには
私たちはワディントン効果区画を直接には持っていないが FabTimeレポートモジュール, スケジュールされたダウンタイムとスケジュールされていないダウンタイムのみを含むようにフィルタリングされた場合、同様の情報を伝えるツール状態のガントチャートがあります。 下のチャートは、5日間にわたる2つのツールのスケジュールされたダウンタイムとスケジュールされていないダウンタイムのパターンを示しています。 この例は、私たちのデモサーバーからのもので、各ツールのスケジュールされたダウンタイムの直後に、スケジュールされていないダウンタイムの大きなブロックが発生していることを示している。 このチャートを見て、スケジュールされたダウンタイムがスケジュールされていないダウンタイムに影響を与えたと結論づけることができるかもしれません(実際にはもっと長い期間のデータを見たいところですが)。
FabTimeソフトウェアユーザーは、Tool State Ganttチャートをフィルタリングして目的のツールを含め("Tool"、"ToolGrp"、または "Area "フィルタを使用)、目的の時間ウィンドウを選択し、"E10St "フィルタに "Sched, Unsch "を入力することで、同様のビューを簡単に作成できます。 そして、そのチャートをホームページのタブに追加して保存することができる。
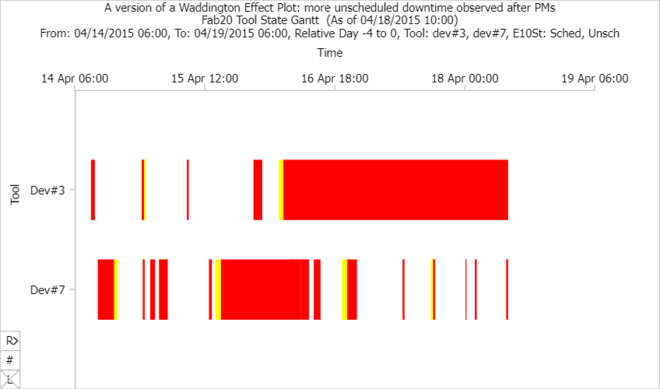
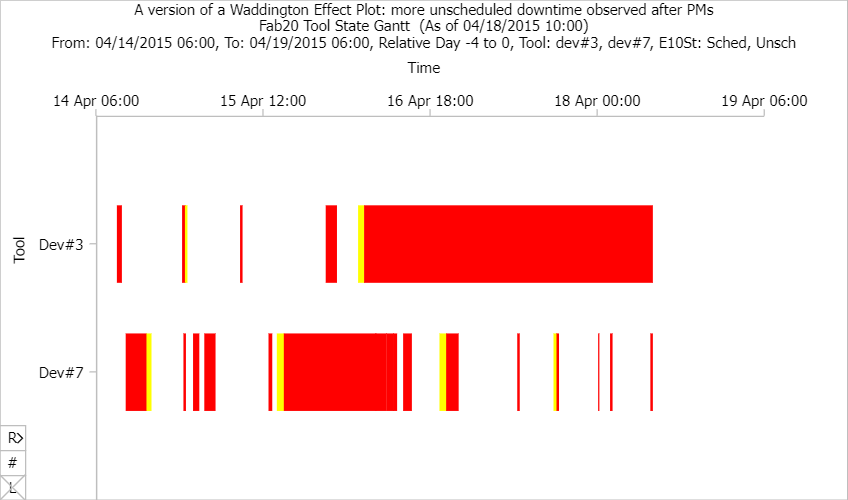
進行中のワディントン効果をどのようにして検知できるでしょうか?
Ignizioは、ワディントン効果の存在を特定するために、目視検査または「自動パターン認識分析」を使用することを推奨しています。 FabTimeのツール状態ガントチャートを使用してワディントン効果プロットを作成する次のステップは、特定のツールについて誰かが視覚的に気づくことに頼るのではなく、何らかの方法で自動的にワディントン効果を検出することです。
これを行うための1つのアイデアは、スケジュールされたダウンタイムイベントの後、定義された時間ウィンドウ内で発生したスケジュールされていないダウンタイムのパーセンテージを記録し、それをツールのスケジュールされていないダウンタイム全体のパーセンテージと比較することです。 しかし、どの時間枠を使うべきだろうか? すべてのPMに対して行うべきなのか、それともある時間より長いPMに対してのみ行うべきなのか?
幸いなことに、INFICONにはこれらの疑問について慎重に考え、実行するソリューションを提案できるメンバーを擁する新しいデータサイエンスチームがあります。 もし購読者の中に、ワディントン効果検出を考えたり実装したりしたことがあり、あなたの考えを共有したい人がいれば、Jennifer Robinsonまで送ってください。 このトピックについては、将来の号でフォローアップする予定です。
では、ワディントン効果は、このニュースレターで以前に推奨したサイクルタイム改善の提案と矛盾するのでしょうか?
ワディントン効果を発見した場合の対処法に移る前に、ワディントンの結果が、このニュースレターで推奨しているメンテナンスイベントの分離と矛盾するかどうかという疑問に戻りましょう。
ワディントン効果は、場合によっては、物事が順調に進んでいる場合、PMを行うことでシステムが乱れ、問題が発生する可能性があることを示しています。 この効果が発生する場合、PMをグループ化するという考えを支持することができる。 もし、それぞれのPMが予定外のダウンタイムが発生する可能性を高めるのであれば、PMの回数を少なくした方がよいかもしれません。
しかし、私たちは、サイクルタイム動作曲線の研究から、一般的に、使用できない時間が長い方が短いよりもサイクルタイムにとってはるかに悪いことも知っています。 例えば、下のグラフは、同じ総使用不能時間に対して、より短く、より頻繁なPM(青のグラフ)と、より長く、より頻繁でないPM(緑と赤のグラフ)の影響を表しています。 長いPMの方がサイクルタイムに与える影響ははるかに悪く、毎週のPMの1回あたりのサイクルタイムは毎日のPM(7分の1の長さ)の1回あたりのサイクルタイムの2倍近くになります。
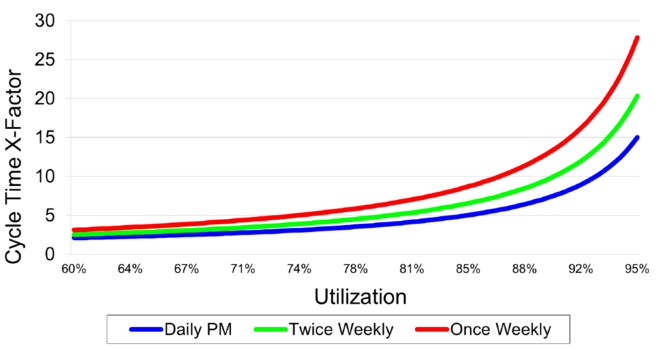
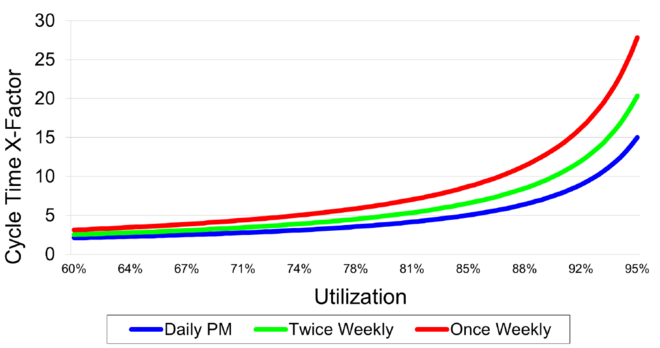
というわけで、私たちは次のような質問を繰り返している。 サイクルタイムコース.同じ量の定期メンテナンスの場合、PMをグループ化すべきでしょうか?
この質問に対する答えは、一般的にはノーであると考えます。 しかし、私たちは、あなたのファブでワディントン効果が起こっているかどうかを定期的にチェックすることを提案します。 ワディントン効果が観察されない工具グループについては、PMをグループ化しないことを推奨します。 (工具を待っているWIPがない場合、工場がエンジニアに厳しい制約がある場合、追加クオールが非常に高価である場合など、特殊な状況では例外があるかもしれません)。
潜在的なワディントン効果が観察される場合、答えはできるだけPMを少なくすることではありません。 これは、車のエンジンでポンポンと音がするのを聞いて、それを聞かないようにラジオを大きくしようと決めるようなものです。 ワディントン効果は、メンテナンスのアプローチに何か問題があることを意味する。 したがって、このツールグループのワディントン効果の原因を突き止め、それを取り除くことが答えとなるはずです。
ワディントン効果を検出した場合、どうすればよいでしょうか?
PHALANX誌の記事に戻ると、イグニツィオ氏は、ワディントン効果の背後にある原因を特定し、不必要な複雑性と過剰な変動性をターゲットにすることによって、その影響を排除または低減することに焦点を当てている。 彼は、メンテナンス仕様を明確に文書化することが特に重要であるとしている。
このアドバイスに基づき、私たちが工場に推奨することは以下の通りである。 ワディントン効果が検出された場合、以下のことを行うべきである:
- 利用可能なあらゆるデータを分析し、効果の背後にある根本的な原因を特定する。
- 特にばらつきを減らすことに重点を置いて、それらの根本的な原因を取り除く。
- この経験から学び、将来問題を回避する方法をチームに伝える。
逸話的な例として、ある工場に勤務していたエンジニアに話を聞いた。その工場では、特定のクラスタツールの大規模なPM(40時間に及ぶ)の後に、ワディントン効果が観察された。 この効果の根本原因を取り除くための広範な努力にもかかわらず、この工場は問題を取り除くのに苦労した。 彼らは最終的に、後のプロセスフローからそのツールを削除した。 しかし、他のケースでは、品質と再現性に焦点を当てることで、ワディントン効果の可能性を減らすことができた。
この研究チームは、一般的に、より短いPMの方が "横道にそれる "リスクが少なく、より短く、より頻繁なPMの方が長いPMよりもパディントン効果の影響を受けにくいことを発見した。 これはもちろん、私たちが推奨している、全体的に利用できない時間を短くすることと一致している。
ここで、ワディントン効果を長年推進してきたイグニツィオが、PMがサイクルタイムに与える影響を減らすために、工場内でPMを「脱クラスタ化」することも提唱していることは、注目に値するだろう。
結論
第二次世界大戦中、C.H.ワディントンと彼のオペレーション・リサーチ・グループは、英国製航空機の機器の信頼性向上に取り組んだ。 同チームは、機器の性能が良好な場合に、予防整備を実施するために介入すると、その後すぐに予定外のダウンタイムが発生する可能性が高まる場合があることを発見した。 ジェームズ・イグニツィオ教授は後に、この行動をワディントン効果とみなし、現代の工場でこれを検出するためにワディントン効果プロットの使用を提案した。 イグニツィオは、根本原因を特定し、複雑さとばらつきを減らし、文書化を改善することによって、ワディントン効果を排除することを提唱した。
ワディントン効果について読んだ後、私たちは当初、このニュースレターで繰り返し推奨している、メンテナンスイベントをグループ化するのではなく、より短く、より頻繁に実施することと矛盾するのではないかと懸念しました。 しかし、よく考えてみると、私たちは、工場がワディントン効果を防止し、それが観察された場合にはそれを排除する一方で、使用できない期間をより短くする努力を続けることが理にかなっているという結論に達した。
この記事では、FabTimeレポートモジュールを使用してどのようにワディントン効果プロットを作成できるかを示しました。 また、ワディントン効果を自動的に識別する方法についても説明しました。 また、ワディントン効果を緩和するための推奨事項についても簡単に議論した。 私たちは、今後さらなる結果を共有することを楽しみにしており、その間のフィードバックを歓迎する。