工厂运营优化
Factory Digital Twin
智能数据仓库
查看正确的信息 - 制定正确的时间表 - 采取正确的行动
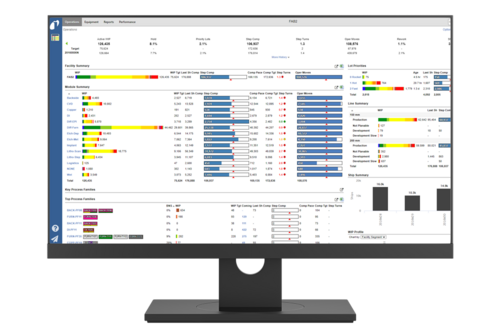
FPS 数字孪生系统是开发智能工厂最关键的组成部分。它收集所有实时操作事件,计算周期时间和吞吐量数据,从而推动功能强大的应用。
自动循环时间和吞吐量
FPS 数字孪生系统可根据批次和基质事件数据自动计算周期时间(CT)和吞吐量(THP)。数字孪生系统可计算多步操作的流程结束时间和到达时间。周期时间和吞吐量数据是 FPS 工厂调度员用来展望未来和优化在制品流程的依据。这也是 Next Move 用来提醒操作员即将采取的必要行动的依据。数字孪生系统和工厂仪表板还提供了了解数字孪生系统中数据的质量和准确性所需的所有工具。通过综合分析,系统可快速确定哪些工具集的事件数据不够可靠,无法生成所需的状态信息,以及哪些地方应使用外部数据或手动覆盖数据。
二十多年的改进和行业智慧
数字孪生系统是整个行业的工业工程知识和最佳实践的宝库。除了增强工具性能状态、增强周期时间和吞吐量等关键功能外,还有其他统计数据,如:运输时间、批次运输、生产线平衡数量、测试晶圆数据等。